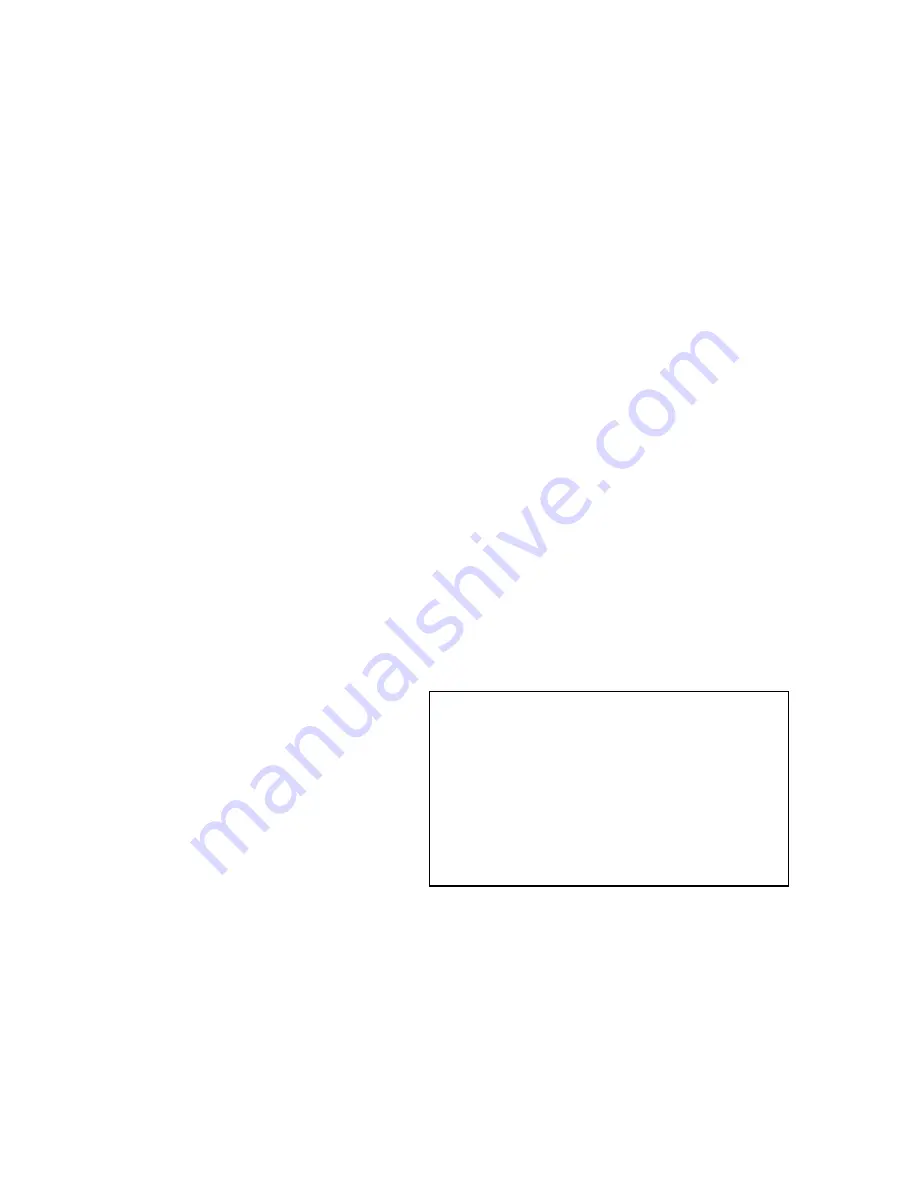
Model 21 -CET-8 Service Manual Page 51
• For best cooking results, use shallow, 2-1/2 inch deep,
perforated pans without covers (Cleveland Range model
number PP-2.5). These give the best heat transfer and
shortest cooking time.
4. Close the steamer door and start manual mode steaming by
pressing the MANUAL (bottom) end of the TIMED/MANUAL
switch.
• The steam generator begins heating the water to steam.
• Steam fills the cooking compartment and begins cooking the
food.
5. If the timer
is used
as a conventional kitchen timer
a. Set the required cooking time by turning the timer dial
clockwise until it points to the correct time mark.
b. When the dial points to zero, a buzzer sounds for 3
seconds. The cooking time is complete.
Remember, in manual mode, the timer does not stop the
steaming functions.
6. To stop manual mode steaming, press the TIMED (top) end of
the TIMED/MANUAL rocker switch, and turn the timer dial to
the 0 mark. The controls will now be set so:
• The ON/OFF switch is in the ON (top) position.
• The TIMED/MANUAL switch is in the TIMED (top) position.
• The timer dial points to 0.
The generator stops steaming, and steam flow to the cooking
compartment gradually stops.
WARNING
SEVERE BURNS may result from exposure to
steam.
Do not open the steamer door before steam flow
stops. Stand back when opening the compartment
door. Open the door slightly to allow steam to vent
before looking or reaching into cooking
compartment Do not reach into cooking compart-
ment until the steam has cleared. Do not reach into
steamer or handle hot items without wearing heat-
proof gloves. Wet or damp gloves conduct heat,
and may cause bums when touching hot items.
7. Carefully open the cooking compartment door, and remove
the pans from the slide racks.
• If the SteamCraft 3.1 will be used again in a few minutes, shut
the door to maintain the cooking compartment temperature.
Printed 12/90
Summary of Contents for steamcraft 21-CET-8
Page 9: ......
Page 53: ...Model 21 CET 8 Service Manual Page 45 Printed 12 90 ...
Page 104: ...Model 21 CET 8 Service Manual Page 97 Printed 12 90 ...
Page 109: ...Figure 6 1 Major Component Groups Printed 12 90 ...
Page 112: ...Page 106 21 CET 8 Service Manual Figure 6 3 Steamer Compartment Group Printed 12 90 ...
Page 114: ...Figure 6 4 Compartment Door And Hinge Assemblies Printed 12 90 ...
Page 120: ...Page 114 21 CET 8 Service Manual Figure 6 7 Electrical Components Assembly Printed 12 90 ...
Page 122: ...Figure 6 8 Steam Generator Assembly Printed 12 90 ...
Page 124: ...Figure 6 0 Heater Assembly Printed 12 90 ...
Page 130: ...Figure 6 11 Water Inlet System Printed 12 90 ...
Page 132: ...Figure 6 12 Condenser And Drainage Systems Printed 12 90 ...
Page 134: ...Figure 6 13 Equipment Stand Printed 12 90 ...
Page 136: ...Figure 6 14 SteamCraft 3 1 Wiring Diagram Electronic Time Printed 12 90 ...
Page 137: ...Figure 6 15 SteamCraft 3 1 Schematic Diagram Electronic Timer Printed 12 90 ...
Page 138: ...Figure 6 16 SteamCraft 3 1 Wiring Diagram Mechanical Timer Printed 12 90 ...
Page 139: ...Figure 6 17 SteamCraft 3 1 Schematic Diagram Mechanical Timer Printed 12 90 ...