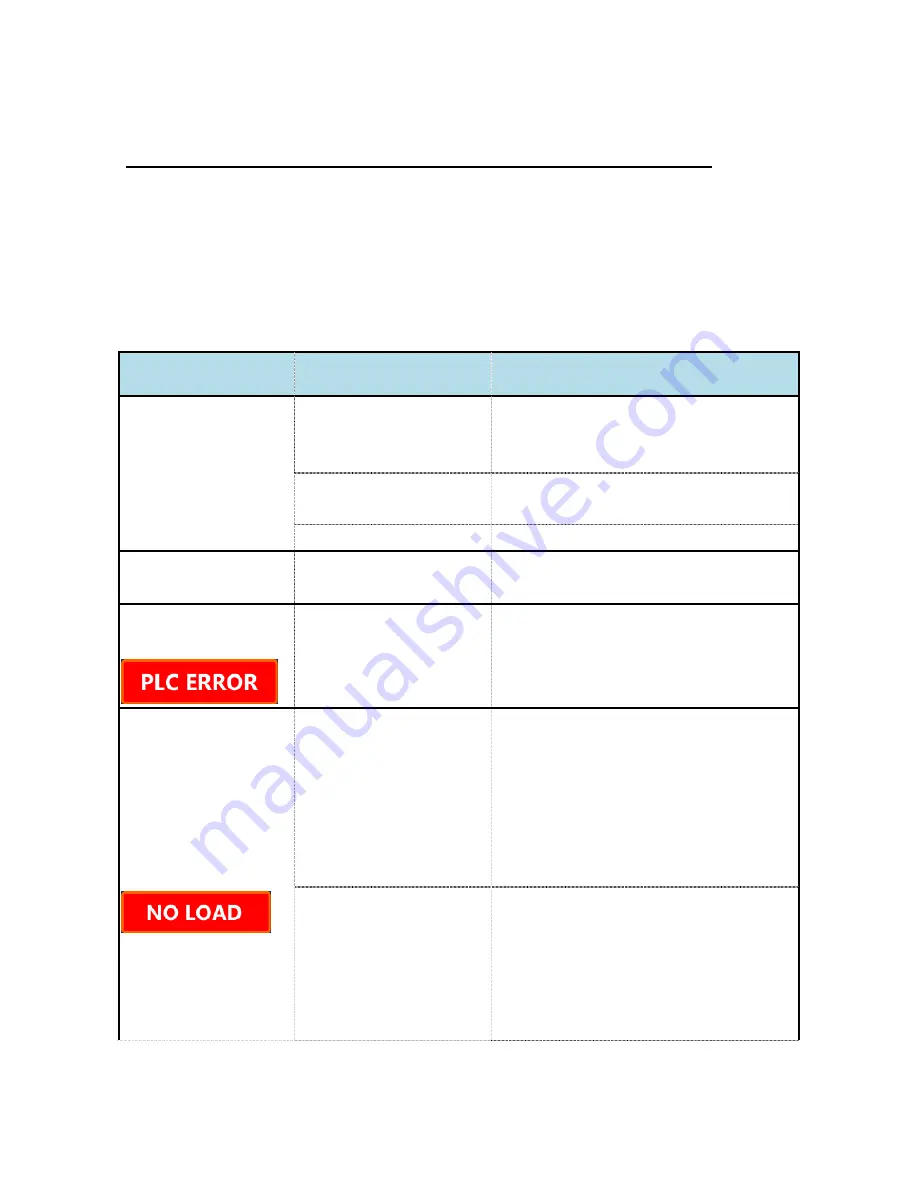
20
Section 5
Trouble shooting and Maintenance
Many operating problems may be solved by carefully reading and following the
instructions in this manual accordingly. Some suggestions for troubleshooting are given
below. Should these suggestions not resolve the problem, contact our SERVICE
DEPARTMENT or a distributor in your region for assistance. If troubleshooting service is
required, please include a full description of the problem.
Problem
Possible Causes
Solution
No Display / lights
No AC power
Ø
Check if PowerPro power supply is
plugged, or AC power source has
problem.
AC power cord is not
connected
Ø
Check AC power cord connections at
both ends. Use the correct cords.
The fuse has blown
Ø
Replace the fuse.
Repeated fuse broken
Hardware failure
Ø
Contact Cleaver Scientific service
department
Operation stops and the
screen displays
Communication wires on
circuit board have loosen or
broken.
Ø
It is recommended to send the
machine back to local distributor or
our Service Department for
maintenance.
Operation stops with
alarm: The screen
displays
Electrophoresis leads are
not connected to the
power supply or to the
electrophoresis unit(s), or
there is a broken circuit in
the electrophoresis cell
Ø
Check the connections to the power
supply and on your electrophoresis cell
to make sure the connection is intact;
check condition of wires in
electrophoresis unit. Close the circuit
by reconnecting the cables. Press
START/STOP to restart the run.
High resistance due to tape
left on a pre-cast gel,
incorrect buffer
concentration, or incorrect
buffer volumes in the
electrophoresis cell
Ø
Make sure the tape is removed from
the pre-cast gel, buffers are prepared
correctly, and the recommended
volume of buffer is added to the
electrophoresis unit.