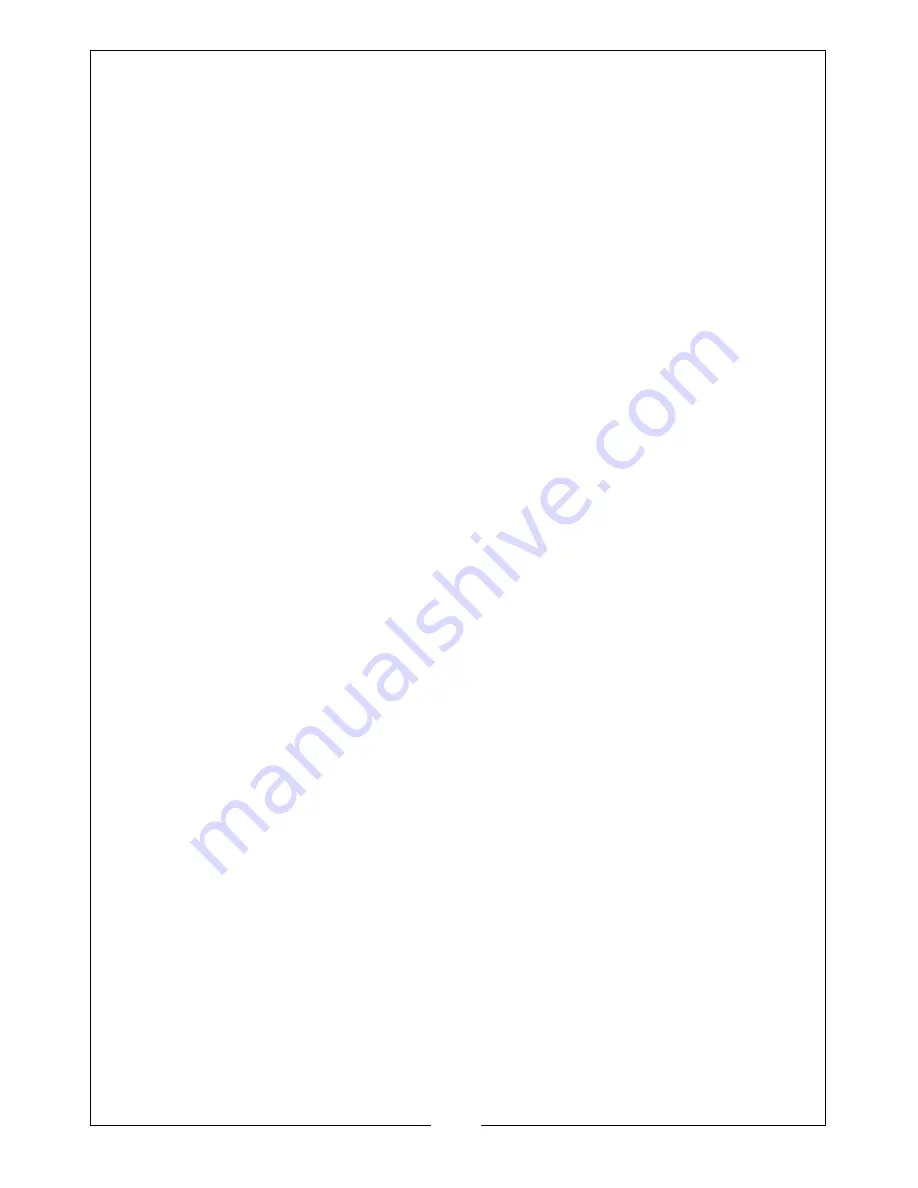
6
Parts & Service: 020 8988 7400 / E-mail: [email protected] or [email protected]
substances likely to generate a
dangerous vapour.
• The welding arc can cause serious
burns. Avoid contact with skin.
• Sparks and molten metal are
ejected during welding. Take
precautions to prevent fire.
• Sparks and molten metal can pass
through gaps. Be aware that fire
can start out of sight.
• Do not weld pressurised containers.
or containers containing
flammable vapours e.g. fuel tanks.
• Always have appropriate fire
fighting equipment to hand
suitable for use in electrical
environments.
• Avoid carrying any fuels with you
e.g. cigarette lighters or matches.
PERSONAL PROTECTION
• The body should be protected by
suitable clothing.
• The use of neck protection may be
necessary against reflected
radiation.
• Arc machines generate a
magnetic field which is detrimental
to pacemakers. Consult your
doctor before going near active
welding equipment/operations.
• The UV and IR radiation generated
by welding is highly damaging to
the eye, causing burns. This can
also affect the skin.
• Always use suitable welding shields
equipped with appropriate
protection filters.
• Where there are pedestrians and
traffic ensure a protective screen is
used to avoid accidental arc glare.
• Do not weld in the vicinity of
children or animals and ensure no
one is looking before striking an
arc.
• Wear hearing protection if
required.
• Allow the weld time to cool. Hot
metal should never be handled
without gloves.
• Take care when adjusting or
maintaining the torch, that it has
had time to cool sufficiently and
the welder is disconnected from
the mains supply.
• First aid facilities and a qualified first
aid person should be available
unless medical facilities are close
by, for immediate treatment of
flash burns of the eyes and skin
burns.
• A hard hat should be worn when
others are working overhead.
• Flammable hair sprays/gels should
not be used by persons intending
to weld or cut.
PROTECTIVE CLOTHING
• Wear gauntlet gloves designed for
use in welding.
• Wear an apron, and protective
shoes.
• Wear cuffless trousers to avoid
entry of sparks and slag.
• Avoid oily greasy clothing.
• Protective head and shoulder
coverings should be worn when
overhead welding.
• Wear helmet with safety goggles or
glasses with side shields
underneath, appropriate filter
lenses or plates (protected by clear
glass). This is a MUST for welding
Summary of Contents for MIG 240
Page 28: ......