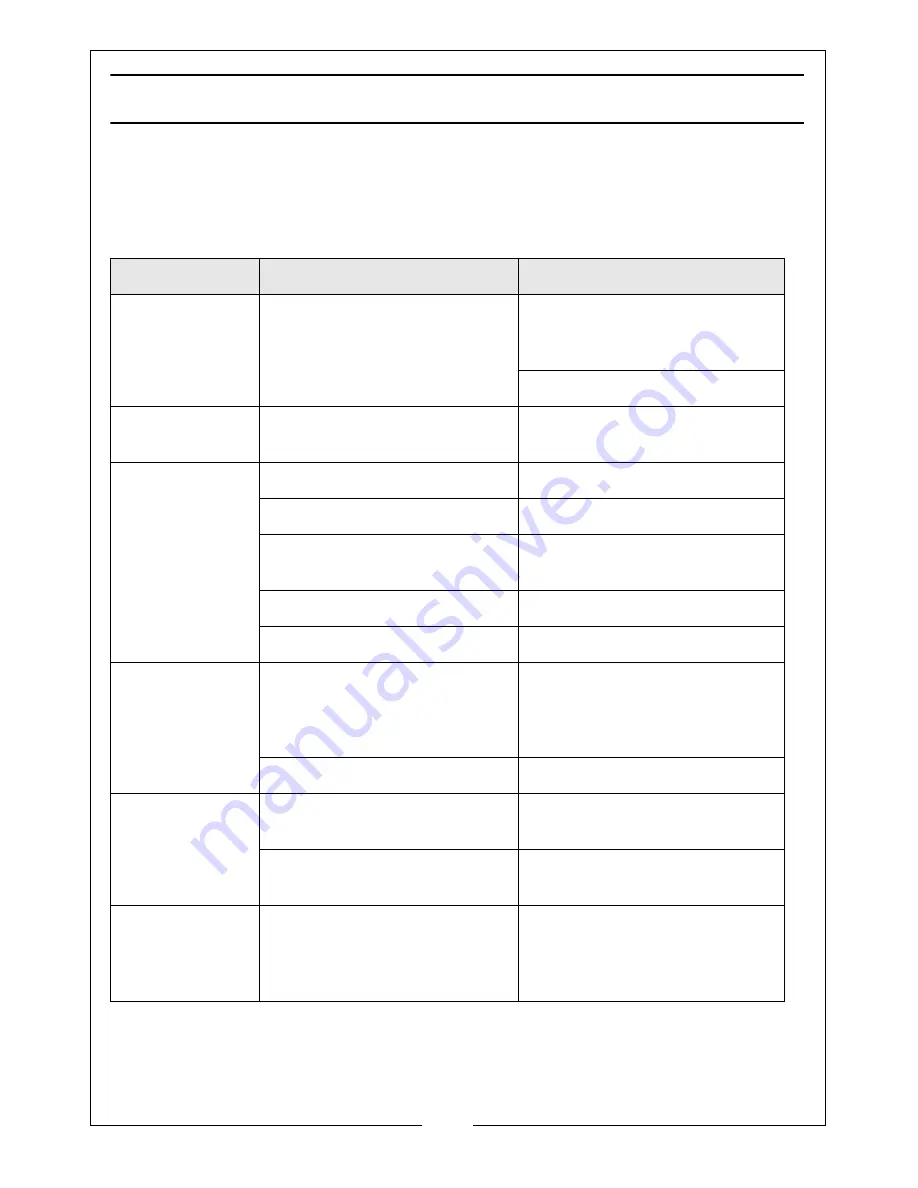
25
Parts & Service: 020 8988 7400 / E-mail: [email protected] or [email protected]
TROUBLESHOOTING
Your CLARKE MIG Welder has been designed to give long and trouble free
service. If, however, having followed the instructions in this booklet carefully,
you still encounter problems, the following points should help identify and
resolve them.
PROBLEM
CAUSE
SOLUTION
No response from
welder.
Check fuses and mains lead.
Replace fuses as necessary, If
problem persists return welder to
your local dealer.
Check fuse size.
Welder does not
feed wire.
Feed motor has malfunctioned.
Return welder to your local
dealer.
Feed motor
running but no
wire being fed
from welder tip.
Insufficient Feed Roller pressure.
Increase roller pressure.
Burr on end of wire.
Re-cut wire square with no burr.
Liner blocked or damaged.
Clean with compressed air or
replace liner.
Inferior wire.
Use only good “clean” wire.
Roller worn out.
Replace roller.
Wire welds itself
to tip.
Wire feed speed too low.
Unscrew tip, cut wire and fit new
tip.
Increase wire speed before
operating again.
Wrong size tip.
Fit correct size tip.
Wire feeds into
‘birds nest’
tangle.
Wire welded to tip.
As above plus reduce feed roller
pressure.
Wire liner damaged preventing
smooth operation.
Renew wire liner.
Loose coils of
wire tangle
around wire drum
inside machine.
Locking knob too slack.
Tighten Locking Knob slightly. Do
not over-tighten.
Summary of Contents for MIG 240
Page 28: ......