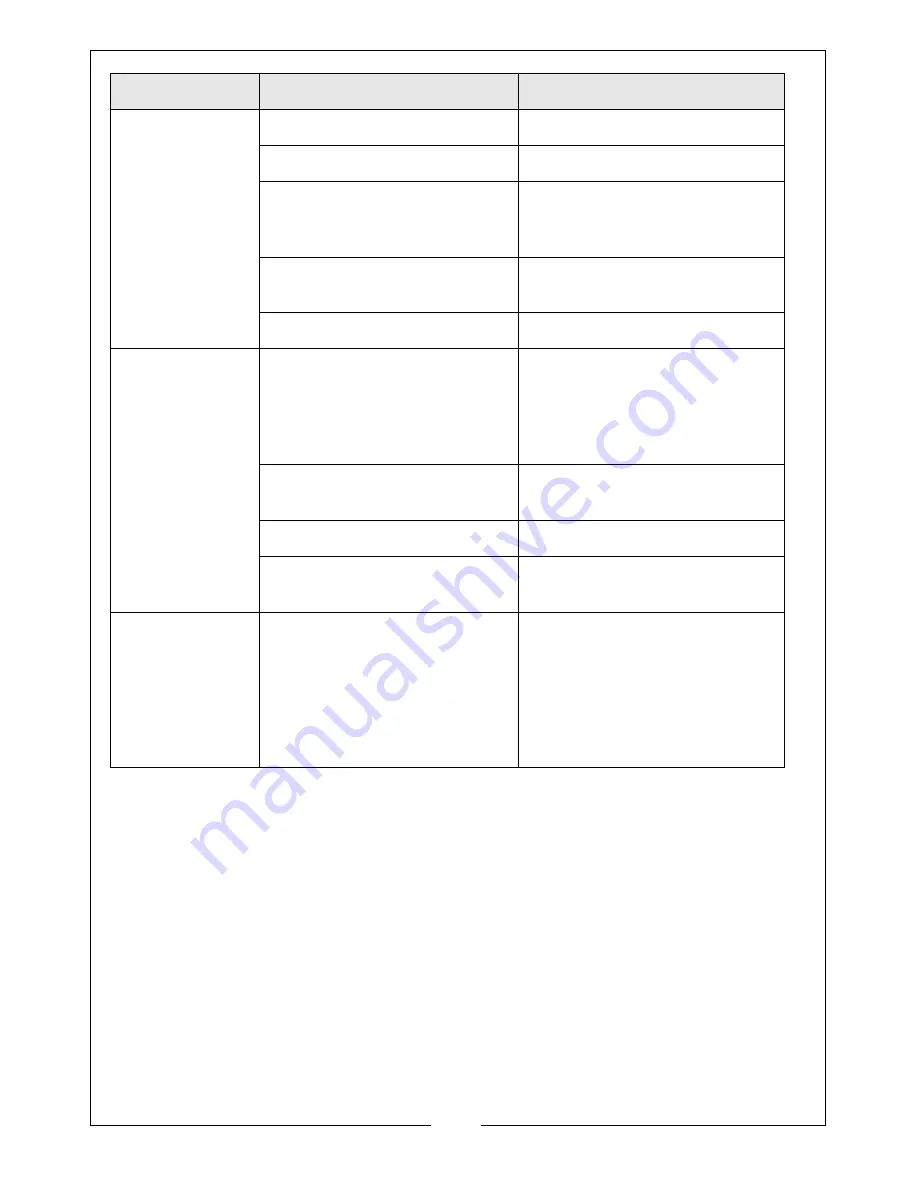
26
Parts & Service: 020 8988 7400 / E-mail: [email protected] or [email protected]
If you have any problems which cannot be resolved by reference to the above, or if you
require spare parts for your welder please contact your local Clarke dealer.
Erratic wire feed.
Tensioning Knob too tight.
Loosen Tensioning Knob slightly.
Tension roller worn.
Check and replace if necessary.
Insufficient pressure on tension
roller.
Increase pressure on tension
roller
Caution: Do not over-tighten.
Wire dirty, rusty, damp or bent.
Re-cut wire and ensure it is
clean.
Liner partially blocked.
Clean with compressed air.
Poor quality
welds.
Insufficient gas at weld area.
Check that gas is not being
blown away by draughts and if
so move to a more sheltered
work area. If not increase gas
supply.
Rusty, painted, damp, oil or
greasy workpiece.
Ensure workpiece is clean and
dry.
Rusty/dirty wire.
Ensure wire is clean and dry.
Poor earth contact.
Check earth clamp/workpiece
connection.
Welder cuts out
whilst in use.
Duty cycle exceeded (auto
cut-out operates).
Allow welder to cool 15-30 mins
before continuing.
Note: If duty cycle is continually
exceeded, damage to the
welder may result and welder
output is probably too small for
application.
PROBLEM
CAUSE
SOLUTION
Summary of Contents for MIG 240
Page 28: ......