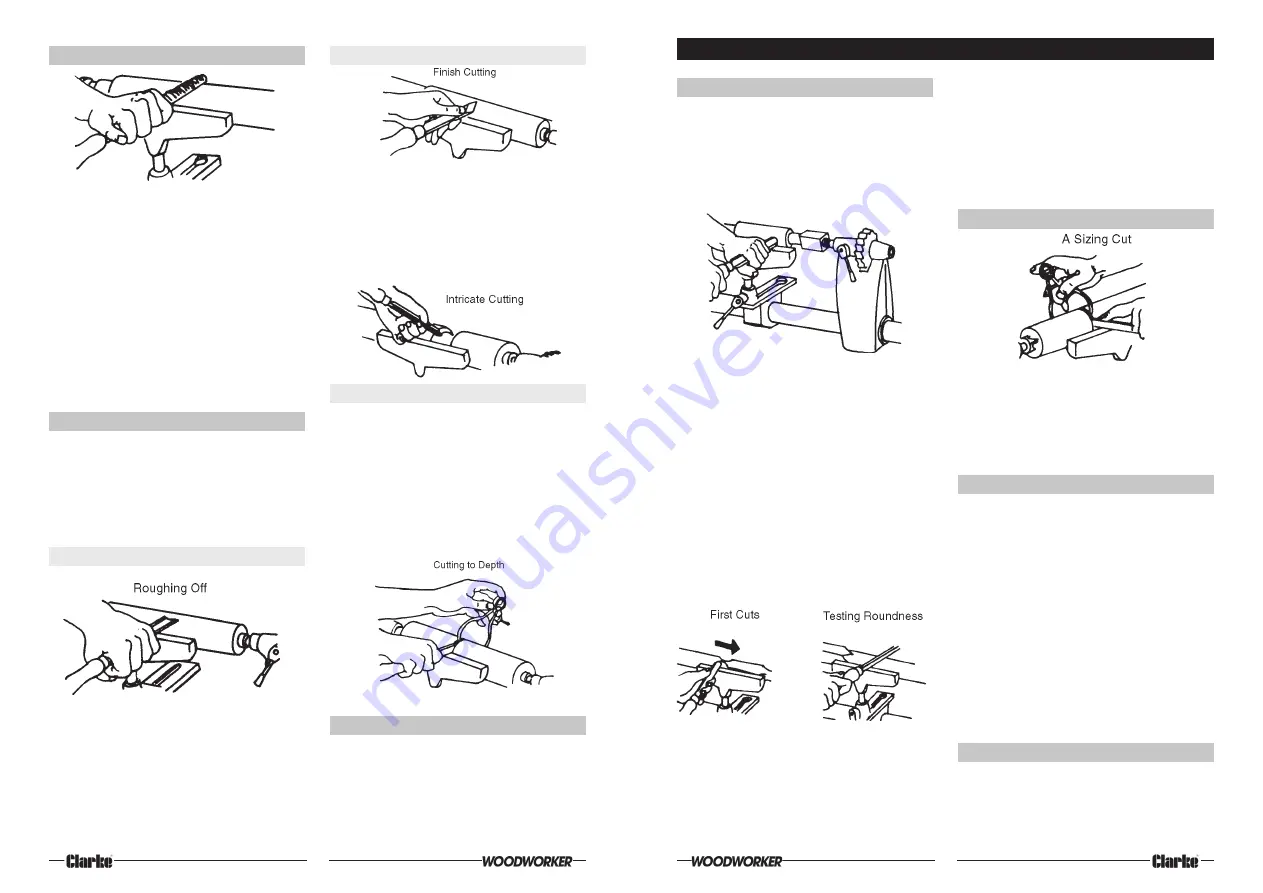
O
9. USING WOOD RASPS AND FILES
10.2 Finish Cutting
A wood rasp will remove stock quickly when held
against the revolving workpiece. Care should
be taken to support the rasp firmly against the
tool rest however, as it can tear the hands
painfully if caught by a rough edge of the
workpiece and kicked back. The rasp will leave
a very rough finish.
Finer finishes (similar to those produced by
scraping), can be obtained by using files in the
same manner. Various shape files can be used
for shaping vees, beads, coves etc. If pressed
into the wood too hard, however, a file can burn
the workpiece surface. Keep the file clean to
keep it cutting uniformly. Files work best on hard
woods.
10. HAND POSITIONS
When handling a chisel, the hand takes a
natural position, being nearer or farther from the
end depending upon the amount of leverage
required. The position of the tool rest hand is a
matter of individual liking, but there are three
generally accepted positions, each best for
certain types of operations.
10.1 Roughing Off
Roughing off and other heavy work requires a
firm grip and solid positioning of the chisel
against the rest. This is best obtained by the tool
rest hand position as illustrated. The wrist is
dropped down so that the heel of the hand
below the little finger acts as a sliding guide
against the rest. The handle hand controls chisel
position.
Finish cutting requires more control with less force
and is better done with the palm of the tool rest
hand turned up. The wrist is still held down, and
the side of the index finger acts as a guide along
the rest. In this position, control of the chisel is
shared by both hands, the fingers of the tool rest
hand being free to assist in positioning the tool.
10.3 Intricate Cutting
Intricate, delicate cutting requires extreme
control, with practically no force. This is best
accomplished by guiding the chisel with the
fingers of the tool rest hand. The hand is held
palm up, with the wrist high, and the little finger
placed against the rest to steady the hand. The
chisel does not touch the rest and the handle
hand is completely secondary to the tool rest
hand.
The first and second positions are equally good
for scraping operations, but the third position is
never used for scraping.
11. CUTTING TO DEPTH
Many scraping operations and cutting to depth
with the parting tool can be easily done with
one hand. The chisel is grasped firmly with the
index finger on top, to press it down against the
rest, and is thrust straight into the work. Holding
the tool thus leaves the other hand free to hold
a pattern , callipers etc., to check work progress.
16
Fig. 21
Fig. 23
Fig. 20
Fig. 24
Fig. 22
MAKING STANDARD CUTS
1. THE ROUGHING OFF-CUT
Reducing a square or odd shaped workpiece
down to a cylinder of approximate size for finish
turning is called roughing-off. Faceplate
turnings and large diameter spindles should first
be partly reduced by sawing , but small spindles
are easily turned down entirely with the large
(3/4”) gouge.
Start the first cut about 50mm from tailstock and
then run it toward the tailstock and off the end
of the workpiece.
Next, start another cut 50mm nearer the
headstock and run it also toward tailstock to
merge with first cut.
Continue in this manner until 50mm to 100mm
from the headstock end, then reverse the
direction of tool travel and work one or two cuts
in succession toward the headstock and off this
end of the workpiece.
Never start a cut directly at the end. If the chisel
catches the end, it will damage the workpiece.
Never take long cuts while corners remain on
the work, as this tends to tear long slivers from
the corners.
The first series of cuts should not be too deep. It
is better to partially reduce the work to a cylinder
along its complete length, then start a second
series of cuts to reduce it to a cylinder. Once a
cylinder has been formed, step the lathe up to
its next fastest speed. Further reductions in size
can now be carried out by cutting as deeply
17
as desired at any spot along the work.
At this stage long cuts from the centre of either
end can also be taken. Roughing-off generally
is continued until the cylinder is approximately
3mm larger than the desired finished size.
Roundness can be tested by laying the gouge
on top of the work - it will not ride up and down
when cylinder is perfectly round.
2. ROUGH-CUTTING TO SIZE
Fig. 26
Fig. 27
Fig. 25
The roughing-off cut can be made to accurately
size the cylinder to a given diameter.
Another method is to make a number of sizing
cuts at intervals along the work, then use the
gouge to reduce the whole cylinder down to
the diameter indicated by these cuts.
3. MAKING SIZING CUTS
Sizing cuts are useful to establish approximate
finish-size diameters at various points along a
workpiece. The work can then be turned down
to the diameters indicated and be ready for
finishing.
Diameters for sizing cuts should be planned to
be about 3mm greater than the desired finished
diameters.
A sizing cut is made with the parting tool.
Hold the tool in one hand and use the other
hand to hold an outside calliper, preset to the
desired sizing-cut diameter.
As the cut nears completion, lower the chisel
point more and more into a scraping position.
When the callipers slip over the workpiece at
the cut, the cut is finished.
4. SMOOTHING A CYLINDER
The final 3mm can be removed in two ways.
Either use the 3/4” skew, working from the centre
toward both ends and taking lighter and lighter
cuts until finished.