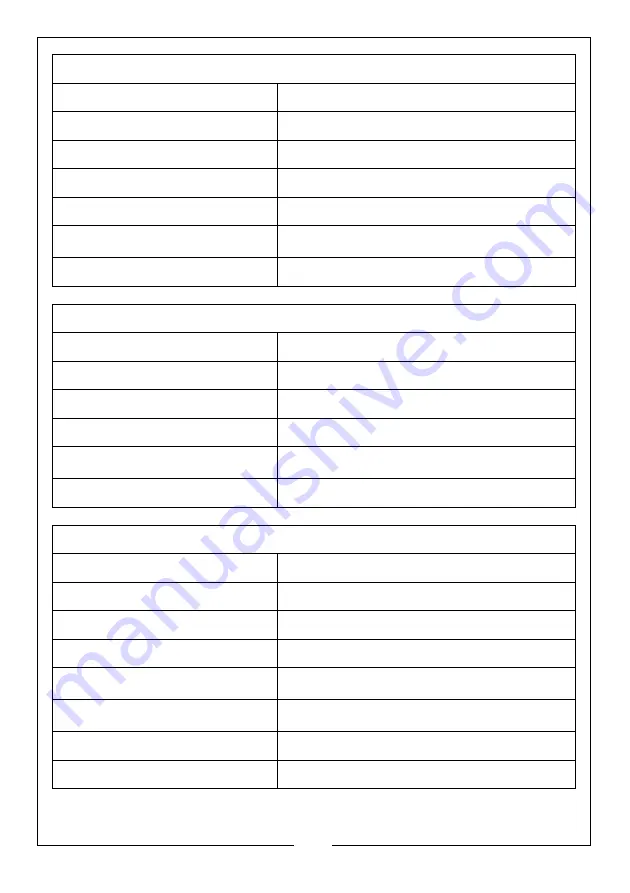
4
Parts & Service: 020 8988 7400 / E-mail: [email protected] or [email protected]
REVERSIBLE DRILL
Chuck Size
1.5 - 10 mm
Air Consumption
6 cfm
Max Speed
1800 rpm
Sound Pressure Level (LpA dB)
87 dB(A)
Sound Power Level (LwA dB)
98 dB(A)
Vibration Levels
1.2 m/s
2
(K= 1.25 m/s
2 )
Dimensions (L x W x H) & Weight
191 x 42 x 144 mm Weight 1.15 kg
DIE GRINDER
Air Consumption
4 cfm (1151 l/min)
Max Speed
22000 rpm
Sound Pressure Level (LpA dB)
83.5 dB(A)
Sound Power Level (LwA dB)
94.5 dB(A)
Vibration Levels
1.2 m/s
2
(K=0.35 m/s
2
)
Dimensions (L x W x H) & Weight
173 x 46 x 68 mm Weight 0.64 kg
DUAL-ACTING SANDER
Air Consumption @ 6.3 bar
2-16 cfm (56-452 l/min)
Pad size
150 mm
Sound Power Level
98.2 dB LWA
Sound Pressure Level
87.2 dBA
Vibration Level
2.5 m/s
2
Uncertainty Factor (K)
1.25 m/s
2
Dimensions (L x D x H) & Weight
223 x 73 x 123 mm Weight = 1.81 kg
Max Speed
10,000 rpm
Summary of Contents for 3110876
Page 32: ......