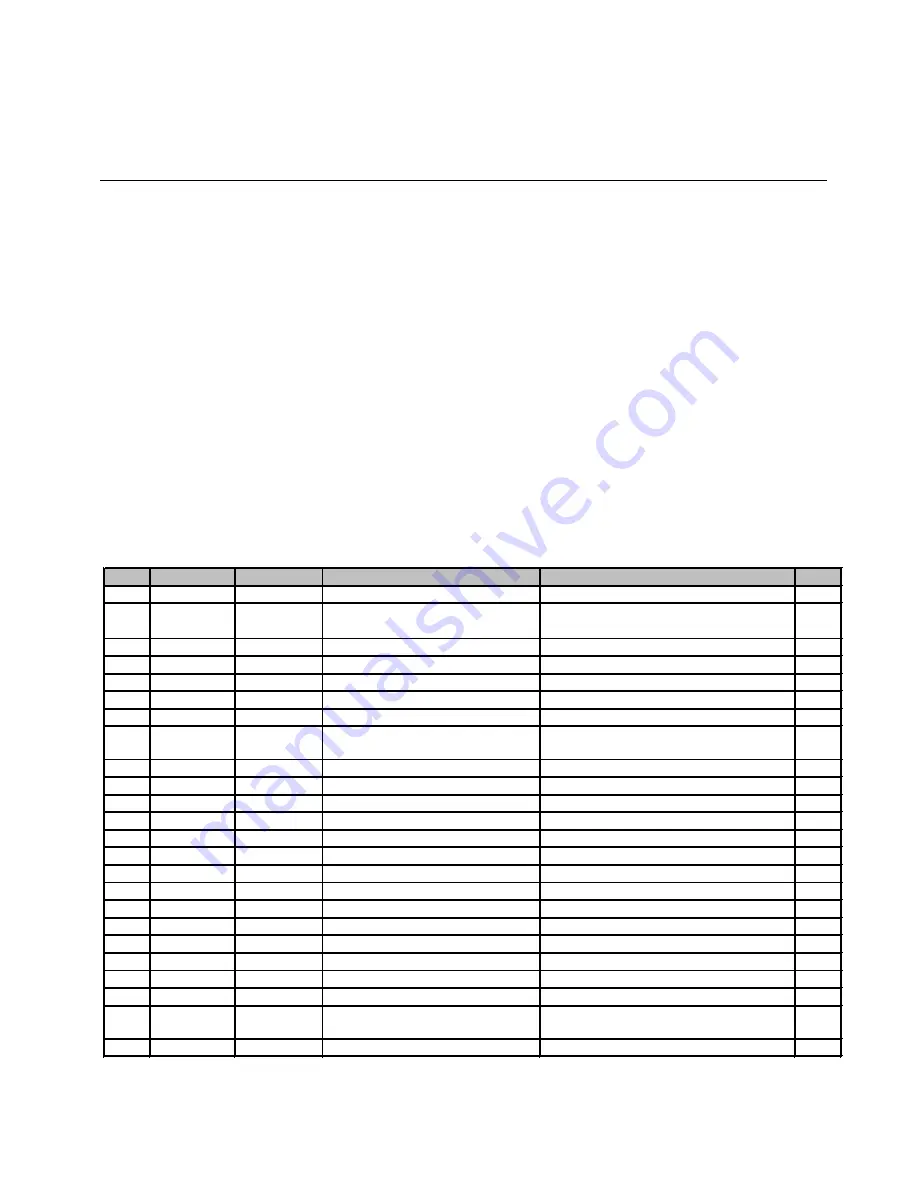
APPENDIX 1 PARTS LIST
1
Equipment Identification
All identification numbers as described in the
Introduction chapter must be furnished when
ordering parts or making inquiries. This infor-
mation is usually found on the nameplate
attached to the equipment. Be sure to include
any dash numbers following the Part
or Assembly numbers.
2
How To Use This Parts List
The Parts List is a combination of an illustra-
tion and a corresponding list of parts which
contains a breakdown of the equipment into
assemblies, subassemblies, and detail parts.
All parts of the equipment are listed except for
commercially available hardware, bulk items
such as wire, cable, sleeving, tubing, etc., and
permanently attached items which are sol-
dered, riveted, or welded to other parts. The
part descriptions may be indented to show part
relationships. To determine the part number,
description, quantity, or application of an item,
simply locate the item in question from the
illustration and refer to that item number in the
corresponding Parts List.
PART NUMBER:
TRANSTIG
300AC
/
DC
700723
No.
DWG No.
Part No.
Description
Additional Information
QTY.
1
CC1
W7001382
Coupling Coil, gen 3.1, IPS
F3A073800 300A AC CC
1
2
CON1
W7001666 Socket, Remote, gen 3.1, IPS
MS3102A20-27S (NIC) 14P with
Wiring Assembly (Remote Socket)
1
3
CT1
W7001304
Transformer, gen 3.1, IPS
F2A503001 CT 1:40
2
4
D1
10-6628
Diode, gen 3.1, IPS
DFA50BA160 (Primary Diode)
1
5
D2-7
10-6629
Diode, gen 3.1, IPS
DBA200UA60 (Secondary Diode)
6
6
FAN1
W7001307
Fan, gen 3.1, IPS
109E5724H507 DC 24V 16.8W
1
7
FCH1
W7001681
Inductor, gen 3.1, IPS
F3A040701 300A AC FCH
1
8
HCT1
10-5003
Sensor, Current, gen 3.1, IPS
HC-TN200V4B15M 200A 4V (Hall
Current Sensor)
1
9
HF.UNIT1
W7001399
HF, Unit, gen 3.1, IPS
HF.UNIT (WK-4840 U04)
1
10
10-6633
HF, Gap, gen 3.1, IPS
U0A601100
1
11
L1
W7001309
Reactor, gen 3.1, IPS
GP-7 (Ring Core)
1
12
L101
W7001400
Reactor, gen 3.1, IPS
ZCAT-3035-1330 (Ring Core)
1
13
L102
W7001672
Reactor, gen 3.1, IPS
F2A734000
1
14
L103
W7001605
Reactor, gen 3.1, IPS
SNG-25B-600
1
15
L105
W7001400
Reactor, gen 3.1, IPS
ZCAT-3035-1330
1
16
PCB1
W7001312
PCB, gen 3.1, IPS
WK-5493 U01 MAIN PCB
1
17
PCB2
W7001678
PCB, gen 3.1, IPS
WK-5597 U02 LINK PCB
1
18
PCB3
W7001314
PCB, gen 3.1, IPS
WK-5548 U01 DDC PCB
1
19
PCB4
10-6635
PCB, gen 3.1, IPS
WK-4819 U01 DETECT PCB
1
20
PCB5
W7001417
PCB, gen 3.1, IPS
WK-5551 U01 CON
N
ECT PC
B 1
21
PCB6
W7001739
PCB, gen 3.1, IPS
WK-5549 U01-1 DC CTRL PCB
1
22
PCB7
W7001423
PCB, gen 3.1, IPS
WK-5550 U01 FILTER PCB
1
23
PCB8-11
W7001318
PCB, gen 3.1, IPS
WK-5479 U01 GATE PCB (with
IRGP20B60PD)
4
24
PCB12
W7001319
PCB, gen 3.1, IPS
WK-5527 U05 PANEL PCB
1
TRANSTIG 300 AC/DC
SERVICE MANUAL
June 30, 2008
A-1
Summary of Contents for TRANSTIG 300 AC/DC
Page 8: ......
Page 20: ...TRANSTIG 300 AC DC SERVICE MANUAL 2 6 June 30 2008 THIS PAGE LEFT INTENTIONALLY BLANK...
Page 34: ...TRANSTIG 300 AC DC SERVICE MANUAL 5 2 June 30 2008 NOTES...
Page 56: ...TRANSTIG 300 AC DC SERVICE MANUAL 11 2 June 30 2008 NOTES...
Page 78: ...THIS PAGE LEFT INTENTIONALLY BLANK TRANSTIG 300 AC DC SERVICE MANUAL 13 18 June 30 2008...
Page 125: ...THIS PAGE LEFT INTENTIONALLY BLANK TRANSTIG 300 AC DC SERVICE MANUAL June 30 2008 A 7...