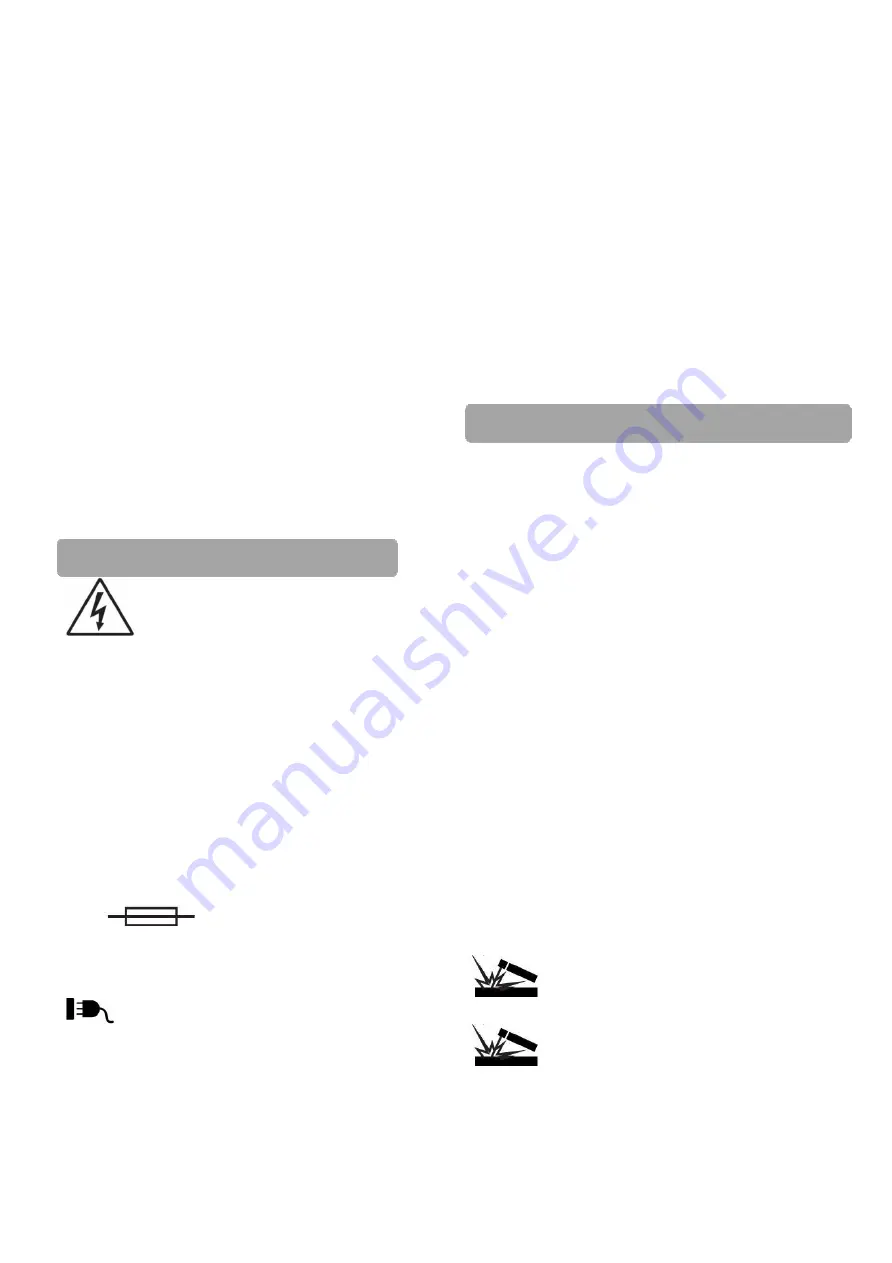
G)
Power supply data:
U1
Input voltage (permitted tolerance: +/- 10%)
I1 eff
Effective absorbed current
I1 max Maximum absorbed current
H)
Welding circuit performance:
U0V
Minimum and maximum open circuit voltage
(open welding circuit).
I2, U2 Current and corresponding normalised voltage
delivered by the welding machine.
X
Duty cycle. Indicates how long it must rest for
in order to cool down. The time is expressed in % on
the basis of a 10 minute cycle (e.g. 60% means 6 min.
work and 4 min.
rest).
A / V
Current adjustment field and corresponding
arc voltage.
I)
European
reference
standard
for
the
construction and safety of welding equipment.
J)
Serial number.
K)
Safety symbols: Refer to safety warnings.
L)
Weight
Starting up
- Connections to the mains must be made by expert or
qualified personnel.
- Make sure that the welding machine is switched off
and the plug is not in the power socket before carrying
out this procedure.
- Make sure that the power socket that welding
machine is plugged into is protected by safety devices
(fuses or automatic switch) and grounded.
Assembly and electrical connections
- Check that the electrical supply delivers the voltage
and frequency corresponding to the welding machine
and that it is fitted with a fuse suited to the maximum
delivered rating current (I2max)
Fig.3
- Plug. If the welding machine is not fitted with a plug,
fit a normalised plug (2P+ T for 1Ph) of suitable
capacity to the power cable
Fig.3.
Connecting to motor generators
- Some welding machines may be powered by a motor
generator. Make sure that this as a power of at least 6
KVA and does not deliver a voltage greater than 270V.
Preparing the welding circuit MMA
- Connect the ground cable** to the welding machine
and to the piece to be welded, as close as possible to
the point to be welded.
- Connect the cable with electrode holder gripper** to
the welding machine and mount the electrode on the
gripper. Refer to the electrode manufacturer’s
instructions concerning connection and welding
current.
- i In welding machines that deliver direct current, most
of the electrode are connected to the positive pole,
and only some electrodes (such as Rutile coated
ones) are connected to the negative pole.
Preparing the welding circuit TIG
- Connect the ground cable** to the welding machine
and to the piece to be welded, as close as possible to
the point to be welded.
- Connect the TIG torch power connector to the
negative pole of the welding machine and mount the
electrode. The torch must be fitted with a gas flow
adjustment valve.
- Connect the TIG torch gas pipe to the output of the
pressure reducer mounted on an ARGON protection
gas cylinder or mixture of Ar+He or Ar+H2, depending
on the material to be welded.
-i The recommended sections (mm2) of the welding
cable, based on the maximum delivered rated current
(I2 max), are shown in Fig.3.
** (This component may be not included with some
models).
Welding process: description of controls and
signals
Once you have put the welding machine into
operation, switch it on and carry out the required
adjustments.
CEL, BAS, TIG ** selector
Select the welding process to be used:
BAS: welding with coated electrode.
CEL: welding with cellulose-coated electrode, suited to
welding high-pressure tanks and piping.