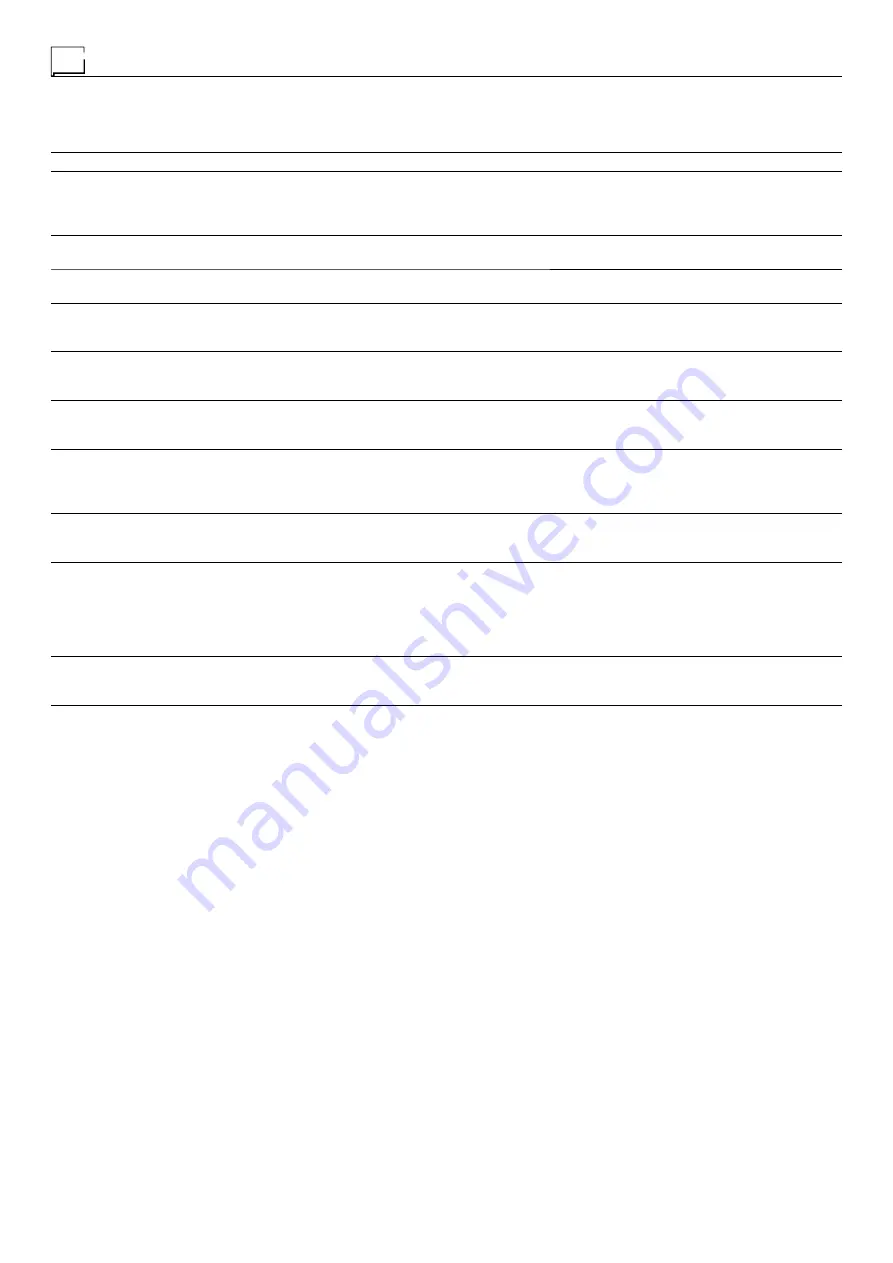
11
Troubleshooting table
WARNING:
Any internal inspections or repairs are only to be done by qualified personnel!
IMPORTANT:
Remember to disconnect the mains power supply and wait for the internal capacitors to discharge (about 2 min-
utes) before starting to check and repair the machine if necessary.
Defect
Solution
The welding machine does
not switch on, TX control
panel switched off.
• Check that the welding machine is installed correctly and that the mains
supply has sufficient power to supply the welding machine.
• Check the switch, cable and plug on the power supply line and replace them if necessary.
• Check, and if necessary replace, the digital interface PCB or the control PCB.
Line fuses fused
“instantaneously”.
• Check that the welding machine is installed correctly.
• Check and if necessary replace the motor, transformer, or rectifier.
Line fuses fused after
a work period.
• Check that you have fitted line fuses of adequate absorption capacity.
Welding machine on, TX
control panel on, fan stopped.
• Check the wiring that powers the fans.
• Check that there are no mechanical impediments blocking the fans.
• Check and if necessary replace the digital interface PCB.
Welding machine on, display
does not show correct values.
• See the error codes and signals shown in the manual for the TX control panel.
• Check the wiring that powers the various boards.
• Check, and if necessary replace, the digital interface PCB or the control PCB.
No gas coming out of the torch.
• Check and if necessary replace the solenoid valve or gas hose.
• Check the wiring that powers the gas solenoid valve.
• Check, and if necessary replace, the digital interface PCB or the control PCB.
The wire feed motor does not
work during MIG-MAG welding.
• Check the wiring that powers the wire feed motor.
• Check that there are no mechanical impediments blocking the motor.
• Check that the motor is working correctly and if necessary replace it.
• Check and if necessary replace the digital interface PCB.
Welding current insufficient
or not constant.
• Check the power supply line.
• Check and if necessary replace the wires (section or length inadequate).
• Check the line voltage using a voltmeter.
Arc ignition difficult, the arc
switches off immediately
after ignition during MIG-
MAG welding.
• Use the TX control panel manual to make sure you have
set the various welding parameters correctly.
• Check compatibility of the torch and the wire used.
• Check that the torch and all its components are working correctly
and replace them if necessary (e.g. worn components).
• Check and if necessary replace the digital interface PCB.
The wire sticks to the
workpiece to be welded.
• Check that there are no mechanical impediments blocking correct unwinding of the wire.
• Check that the motor is working correctly and if necessary replace it.
• Check and if necessary replace the digital interface PCB.
Summary of Contents for TREO 1800 Synergic MIG-MAG
Page 12: ...12 Electro topographical diagram 2101AB10...
Page 14: ......
Page 22: ......
Page 42: ......