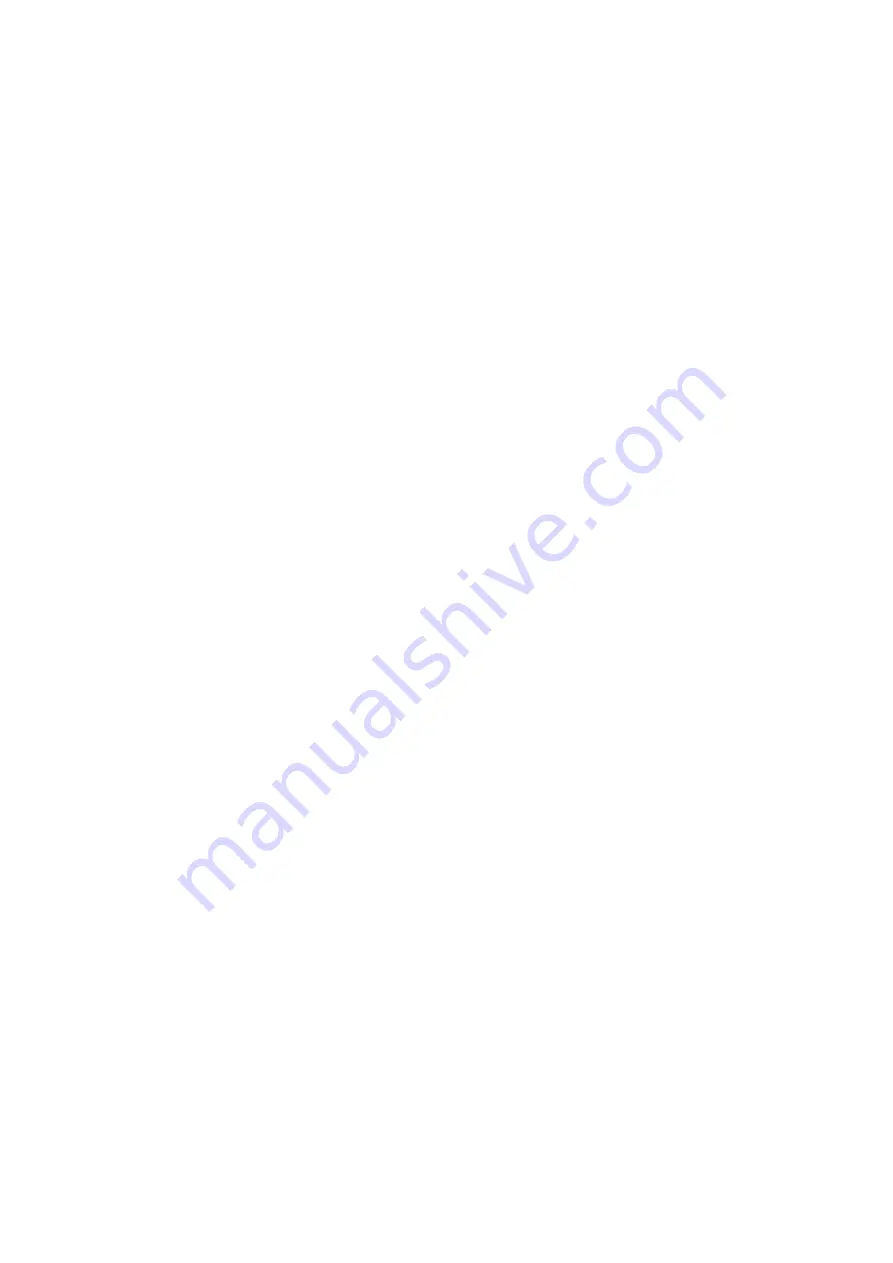
10
2 - PrElIMInary chEcks
2.1 - check equipment received
•
Check that the unit has not been damaged during
transport and that no parts are missing. If the unit has
been damaged or the shipment is incomplete, send a
claim to the shipping company.
•
Compare the name plate data with the order. The name
plate is attached in two places to the unit:
-
On one of the unit sides on the outside
-
On the control box door on the inside.
•
The unit name plate must include the following
information:
-
Version number
-
Model number
-
CE marking
-
Serial number
-
Fluid being transported
-
Year of manufacture and test date
-
Refrigerant used and refrigerant class
-
Refrigerant charge per circuit
-
Containment fluid to be used
-
PS: Min./max. allowable pressure (high and low
pressure side)
-
TS: Min./max. allowable temperature (high and
low pressure side)
-
Pressure switch cut-out pressure
-
Unit leak test pressure
-
Voltage, frequency, number of phases
-
Maximum current drawn
-
Maximum power input
-
Unit net weight
•
Confirm that all accessories ordered for on-site
installation have been delivered and are complete and
undamaged.
The unit must be checked periodically during its whole
operating life to ensure that no shocks (handling accessories,
tools etc.) have damaged it. If necessary, damaged parts must
be repaired or replaced. See also chapter - “Standard
maintenance”.
2.2 - Moving and siting the unit
2.2.1 - moving
See chapter 1.1 “Installation safety considerations”.
2.2.2 - Placing the unit
The machine must be installed in a place that is not accessible
to the public or protected against access by non-authorised
persons.
In case of extra-high units the machine environment must
permit easy access for maintenance operations.
Always refer to the chapter 3 “Dimensions, clearances” to
confirm that there is adequate space for all connections
and service operations. For the centre of gravity coordinates,
the position of the unit mounting holes, and the weight
distribution points, refer to the certified dimensional
drawing supplied with the unit.
The support points under the chassis must have at least the
size of the chassis opening at the lifting point (minimum 220
x 180 mm) in order to prevent a deformation of the chassis.
Typical applications of these units are in refrigeration
systems, and they do not require earthquake resistance.
Earthquake resistance has not been verified.
CAUTION: Only use slings at the designated lifting points
which are marked on the unit.
Before siting the unit check that:
•
The permitted loading at the site is adequate or that
appropriate strenghtening measures have been taken.
•
The unit is installed level on an even surface
(maximum tolerance is 5 mm in both axes).
•
There is adequate space above the unit for air flow
and to ensure access to the components.
•
If the support structure is sensitive to vibration and/
or noise transmission, it is advisable to insert anti-
vibration mounts (elastomeric mounts or springs)
between the unit and the structure. Selection of these
devices is based on the system characteristics and
the comfort level required and should be made by
technical specialists.
•
The number of support points is adequate and that
they are in the right places.
•
The location is not subject to flooding.
•
For outdoor installations, where heavy snowfall is
likely and long periods of sub-zero temperatures are
normal, provision has to be made to prevent snow
accumulating by raising the unit above the height of
drifts normally experienced.
•
Baffles may be necessary to deflect strong winds. They
must not restrict air flow into the unit.
CAUTION: Before lifting the unit, check that all casing
panels are securely fixed in place. Lift and set down the
unit with great care. Tilting and jarring can damage the
unit and impair unit operation.
If 30XAV-ZE units are hoisted with rigging, it is advisable
to protect coils against crushing while a unit is being
moved. Use struts or spreader bar to spread the slings
above the unit. Do not tilt a unit more than 15°.
WARNING: Never push or lever on any of the enclosure
panels of the unit. Only the base of the unit frame is
designed to withstand such stresses.
No force or effort must be applied to pressurised parts,
especially via pipes connected to the evaporator.
2.2.3 - Checks before system start-up
Before the start-up of the refrigeration system, the complete
installation, including the refrigeration system must be
verified against the installation drawings, dimensional
drawings, system piping and instrumentation diagrams and
the wiring diagrams.
Heat exchange fluid temperatures above the maximum
recommended can lead to an increase in the refrigerant
pressure and can cause a loss of refrigerant due to the
relief valve discharge.