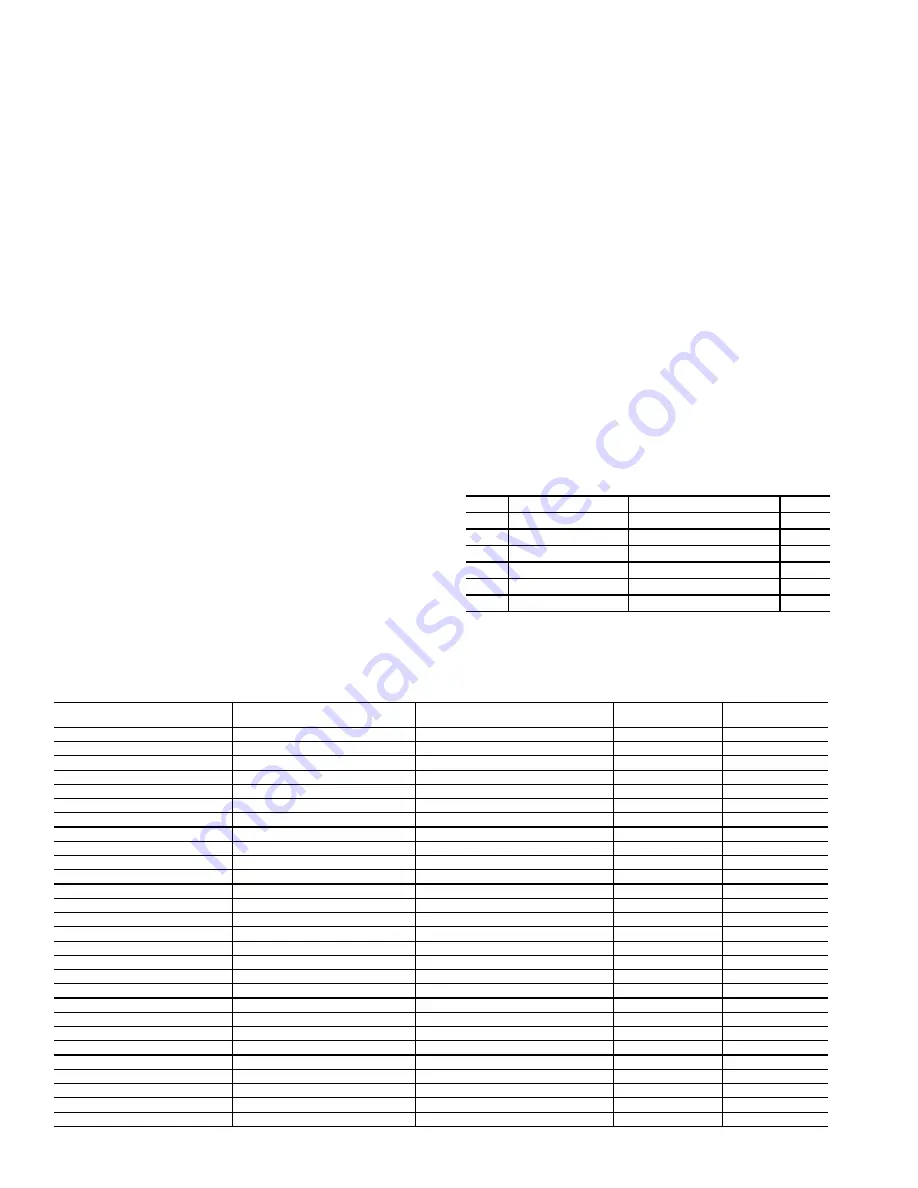
54
OPERATION
Sequence of Operation —
With a command to start
the chiller, the cooler and condenser pumps will start. After
verifying water flow, the control will monitor the entering and
leaving water temperatures. If the need for mechanical cooling
is determined, the control decides which circuit and compres-
sor to start. The control will start the required compressor com-
pletely unloaded. The control will continue to load this circuit
by moving the slide valve to satisfy cooling requirements.
Once fully loaded, the control will start an additional circuit to
satisfy the load as required. Shutdown of each circuit under
normal conditions occurs in the opposite sequence to loading.
Once the circuit is fully unloaded the compressor is shut off
and the EXV will close completely.
Dual Chiller Sequence of Operation —
With a
command to start the chiller, the master chiller determines
which chiller will become the lead chiller based on the configu-
ration of
Lead Lag Select
, LLBL
and
Lead/Lag Balance Da-
ta
, LLBD
. The lead chiller is always started first and the lag
chiller is held at zero percent capacity by the master chiller
forcing the lag demand limit value to 0%. If Lead Pulldown
Time (
Lead Pulldown Time
, LPUL
) has been configured, the
lead chiller will continue to operate alone for that specified
time. After the Lead Pulldown Time timer has elapsed and
when the lead chiller is fully loaded, either all available com-
pression is on or at the master demand limit value, then the lag
start timer (
Lag Start Timer
, LLDY
) is initiated. When the
pulldown timer and lag start timer has elapsed and the Com-
bined Leaving Chilled Water Temperature is more than 3° F
(1.7° C) above the set point, then the lag chiller is started. If the
lag chiller’s water pump was not started when the machines
went into occupied mode, the lag chiller water pump will be
started. The lag chiller will start with the master chiller forcing
the lag chiller demand limit value (LAG_LIM) to the master’s
demand limit value. If lead/lag capacity balance is selected,
once the lag chiller has started, the master shall try to keep the
difference in capacity between lead and lag less than 20%. The
master shall then be responsible for water loop capacity
calculation, and will determine which chiller, the lead or lag,
will increase or decrease capacity. When the load reduces, the
lag chiller will be the first chiller to unload. To accomplish this,
the lead chiller set point is decreased by 4° F (2.2° C) until the
lag chiller unloads.
PUMP OPERATION — For parallel chiller pump operation,
the lead chiller’s water pump will be started. The lag chiller’s
water pump will be maintained off if
Lag Unit Pump Control
,
LAGP
=
0
. The internal algorithm of lead chiller will control ca-
pacity of the lead chiller.
For series chiller operation, the pump is always controlled
by the master chiller.
Operating Modes —
Operating modes are override
modes that affect normal operation of the equipment. More
than one operating mode can be in effect at the same time.
Some operating modes have corresponding capacity control
overrides in the Capacity Control Overrides section on
page 43.
For the Touch Pilot display, the status of the operating
modes can be found in the
MODES
submenu, which is under
the
STATUS
menu. Each operating mode and its status (Yes =
active, No = inactive) is listed.
For the Navigator display, the status of the operating modes
can be found in the
MODE
submenu under the
OPERATING
MODES
menu. The 6 top priority operating modes are dis-
played in
MD01
through
MD06
. To view the modes with the
Navigator display:
See Table 37 for a list of operating modes.
Table 37 — 30XW Operating Modes
ITEM
ITEM EXPANSION
PATH
VALUE
MD01
First Active Mode
Operating modes
MODE 0-32
MD02
Second Active Mode Operating modes
MODE 0-32
MD03
Third Active Mode
Operating modes
MODE 0-32
MD04
Fourth Active Mode
Operating modes
MODE 0-32
MD05
Fifth Active Mode
Operating modes
MODE 0-32
MD06
Sixth Active Mode
Operating modes
MODE 0-32
NAVIGATOR OPERATING
MODE NUMBER
NAVIGATOR EXPANSION
TOUCH PILOT DISCRIPTION
TOUCH PILOT
LINE NUMBER
TOUCH PILOT
VALUE
01
Startup Delay in Effect
Startup Delay in Effect
2
Yes/No
02
Second Setpoint in Use
Second Setpoint in Use
3
Yes/No
03
Reset in Effect
Reset in Effect
4
Yes/No
04
Demand Limit Active
Demand Limit Active
5
Yes/No
05
Ramp Loading Active
Ramp Loading Active
6
Yes/No
06
Cooler Heater Active
Cooler Heater Active
7
Yes/No
07
Cooler Pumps Rotation
Cooler Pumps Rotation
8
Yes/No
08
Pump Periodic Start
Pump Periodic Start
9
Yes/No
09
Night Low Noise Active
Night Low Noise Active
10
Yes/No
10
System Manager Active
System Manager Active
11
Yes/No
11
Mast Slave Ctrl Active
Mast Slave Active
12
Yes/No
12
Auto Changeover Active
Auto Changeover Active
13
Yes/No
13
Free Cooling Active
Free Cooling Active
14
Yes/No
14
Reclaim Active
Reclaim Active
15
Yes/No
15
Electric Heat Active
Electric Heat Active
16
Yes/No
16
Heating Low EWT Lockout
Heating Low EWT Lockout
17
Yes/No
17
Condenser Pumps Rotation
Condenser Pumps Rotation
18
Yes/No
18
Ice Mode in Effect
Ice Mode in Effect
19
Yes/No
19
Defrost Active on Cir A
Defrost Active on Cir A
20
Yes/No
20
Defrost Active on Cir B
Defrost Active on Cir B
21
Yes/No
21
Low Suction Circuit A
Low Suction Circuit A
22
Yes/No
22
Low Suction Circuit B
Low Suction Circuit B
23
Yes/No
24
High DGT Circuit A
High DGT Circuit A
25
Yes/No
25
High DGT Circuit B
High DGT Circuit B
26
Yes/No
27
High Pres Override Cir A
High Pres Override Cir A
28
Yes/No
28
High Pres Override Cir B
High Pres Override Cir B
29
Yes/No
30
Low Superheat Circuit A
Low Superheat Circuit A
31
Yes/No
31
Low Superheat Circuit B
Low Superheat Circuit B
32
Yes/No