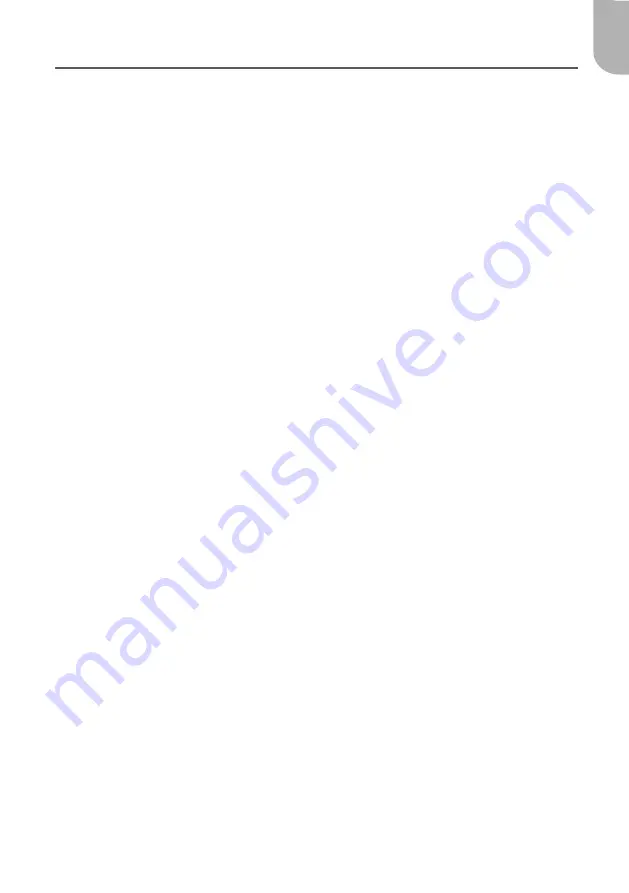
EN
4.9.1 -
Optional balancing valves
Two-way valve with water flow balancing function is
embedded with a differential pressure controller (with
or without pressure test points to control the water flow
settings). The setting of the valve is shown in Fig. 16.
The manual control knob (16a) is ready fitted to protect
valve stem and pre-set mechanism and facilitates
manual control of valve during commissioning.
Setting procedure:
- Remove control knob from the valve (16a)
- Loosen knurled nut (16b).
-
Adjust the desired dial setting with the white knob
(16c) - see table below.
- Retighten knurled nut by hand (16d).
WARNING: The valves have to be open when
flushing or pressure testing the system. Strong
pressure impacts can damage closed valves.
Differential pressure across the valve’s control path
is not allowed to exceed 400 kPa.
4.9.2 -
230 V - Actuators
Two types of valve actuators are provided: electro
thermal actuator (on/off control) or modulating actuator
(3-point).
The actuator supply is 230 V a.c.
4.9.3 -
24 V - Actuators
Three types of valve actuators are provided: one electro
thermal actuator (on/off control) or two modulating
actuators (3-point or 0-10V).
Both modulating actuators can be operated manually
with a hexagonal key. The 0-10V command voltage
range of the modulating actuator can also be adjusted.
The actuator supply is 24 V a.c.
NOTE: 24V actuators are not compatible with Carrier
controllers (Thermostats A/B/C/D, WTC & NTC).
4.9.4 - Actuator replacement procedure
The actuators on both the chilled water and the hot water
valves may be replaced in case of failure.
WARNING: Do not connect on the same neutral wire
the valve actuator 24 Vac and the controller.
- Disconnect the power supply to the unit before
carrying out any work on a unit.
- Disconnect the actuator power supply cable.
• 230 V type actuator used with the Carrier
numeric controller: Disconnect the actuator
power supply cable fitted with a quick connector.
• 230 V actuator used with an electronic
thermostat: Remove the plastic protection cover
held in place with two screws. Disconnect the
actuator power supply cable connected to the
quick connector. This can be done by pressing
down the spring tongue using a screwdriver and
pulling out the wire from the appropriate terminal.
-
Uncouple the faulty actuator. Refitting is by the
reversal of the procedure described above.
WARNING: Ensure that the actuator is firmly screwed
to the valve body (maximum torque 15 N·m).
4.9.5 - Valve body replacement procedure
- Disconnect the power supply before carrying out
any work on a unit.
- Close the isolating valves on the manifolds.
-
Remove flexible water pipes.
- Remove the valve actuators taking care to identify
the cooling and heating valves.
-
Disconnect the flexible condensate drain pipe which
is held in place by a collar (the collar is not supplied
by Carrier).Remove the two-way or four-way water
flow control valve bodies. Depending how the unit is
configured, the four-way valve coupling may be fitted
with a heating/cooling changeover switch, if so do
not remove it.
-
Fit the new valve body to the coil (fit new gaskets).
-
Reconnect the flexible condensate drain pipe
which is held in place by a collar (the collar is not
supplied by Carrier).
-
Refit the valve actuators taking care to ensure that
they are correctly fixed to the valve body.
-
Reconnect the flexible water pipes by tightening
the union nuts. Retighten all the water connections
and ensure that all gaskets have been changed
and correctly fitted (maximum torque 15 N·m).
- Open the isolating valves on the manifolds and
purge all air from the system.
- Check that there are no leaks and reconnect the
power to the unit.
WARNING: When replacing a valve always ensure
that the direction of flow through the valve is as
shown by the arrow on the valve body. If the
direction of flow is wrong, the valve body will
deteriorate rapidly and the flow control will be
distorted.
4.10 - Flexible pipe option
■
Minimum bending radius:
- Non-insulated pipes 72 mm
- Insulated pipes 106 mm.
Connections 1/2” diameter (female)
4 - COMPONENTS AND MAINTENANCE
19
Summary of Contents for 42EP
Page 2: ......
Page 7: ...EN Floor unit 10 a 10 b 10 2 11 a 11 a 11 7...
Page 8: ...Ceiling unit a b 12 1 Floor unit b a 12 2 a a Ceiling unit Floor unit 13 8...
Page 9: ...EN a b c d c 16a 16b 16c 16d 14 15 16 9...
Page 10: ...d Voir DETAIL A SEE DETAIL DETAIL A ECHELLE 3 10 a 17 18 19 10...
Page 25: ...FR Unit pour faux plancher 10 a 10 b 10 2 11 a 11 a 11 25...
Page 27: ...FR a b c d c 16a 16b 16c 16d 14 15 16 27...
Page 28: ...d Voir DETAIL A SEE DETAIL DETAIL A ECHELLE 3 10 a 17 18 19 28...
Page 43: ...DE Bodenger t 10 a 10 b 10 2 11 a 11 a 11 43...
Page 44: ...Deckenger t a b 12 1 Bodenger t b a 12 2 a a Deckenger t Bodenger t 13 44...
Page 45: ...DE a b c d c 16a 16b 16c 16d 14 15 16 45...
Page 46: ...d Voir DETAIL A SEE DETAIL DETAIL A ECHELLE 3 10 a 17 18 19 SIEHE DETAIL A MASSSTAB 3 10 46...
Page 61: ...SP De suelo 10 a 10 b 10 2 11 a 11 a 11 61...
Page 62: ...De techo a b 12 1 De suelo b a 12 2 a a De techo De suelo 13 62...
Page 63: ...SP a b c d c 16a 16b 16c 16d 14 15 16 63...
Page 64: ...d Voir DETAIL A SEE DETAIL DETAIL A ECHELLE 3 10 a 17 18 19 VER DETALLE A ESCALA 3 10 64...
Page 75: ......