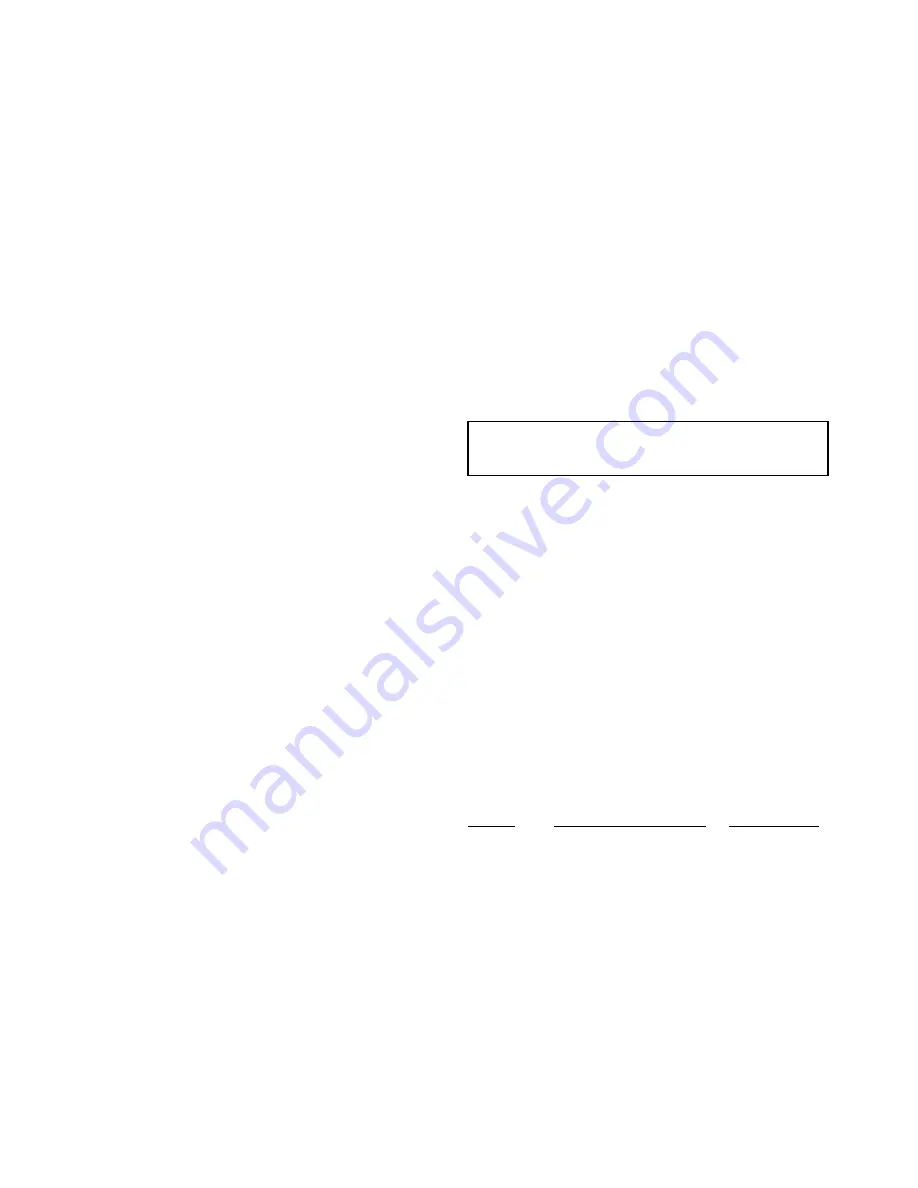
36
STAGED COOLING — The staging function is used for two
position valves or DX cooling (1 or 2 stages). The staging
function uses the cooling submaster reference from the PID
and compares the value to the supply-air temperature to calcu-
late the required number of output stages to energize.
For DX cooling, configurable Time Guard delays are pro-
vided to allow for up to 2 stages of compression. Also a
DX Lockout will prevent operation of the DX cooling if the
outdoor-air temperature is below this value.
NOTE: Outdoor-air temperature must be provided through a
CCN broadcast over the network.
Once cooling is active, a maintenance decision indicates
that cooling is in effect. Also the cooling capacity is then calcu-
lated based upon the supply-air temperature, the space temper-
ature, and a minimum supply air temperature limit of 50 F.
The cooling algorithm controls the valve or stages of DX
cooling to prevent the space temperature from exceeding the
current cooling set point (which includes any calculated offset
value from a T56 or T57 sensor slide bar during occupied peri-
ods). Also, the cooling is controlled so that the supply-air tem-
perature does not fall below 50 F when cooling is active.
Number of Stages:Range
1, 2
Default Value
1
The Time Guards must be set to Enable for output to a com-
pressor, and set to Disable for output to a valve or compressor
unloader.
Stage 1
Time Guard:
Range
Disable/Enable
Default Value
Enable
Stage 2
Time Guard:
Range
Disable/Enable
Default Value
Disable
The stage outputs will send a 24 VAC signal to the device
when turned on if these configurations are set to normal. The
device will be sent a 24 VAC signal in the Off state if Inverted
logic is applied.
Two-Position
Valve Logic Type: Range
Normal/Inverted
Default Value
Normal
Stage 2 DX
Logic Type:
Range
Normal/Inverted
Default Value
Inverted
HEATING TYPE — The Heating Type configuration sets the
type of heating that the fan coil will use. Heating type has four
selections available: 0 = None, 1 = Modulating Valve, 2 = Two-
Position Valve, 3 = Electric Heat, 4 = Pipe Changeover with
Electric Heat.
Heating Type:
Range
0 to 4
Default Value
0
HEATING CONTROL — The fan coil controller determines
if a heating demand exists in the space. The zone controller
reads the space temperature sensor and compares the tempera-
ture to the current low set point (including any calculated offset
value from a T56 or T57 sensor) during occupied periods. If it
is below the set point, and heating is configured and available,
it then calculates the required supply air temperature to satisfy
the given conditions. The calculated value (heating submaster
reference) is compared to the actual supply-air temperature and
the output is then adjusted to satisfy conditions. A Proportional
/ Integral / Derivative (PID) loop is used. The modulating con-
trol function compares the submaster reference from the PID
loop to the supply-air temperature and then calculates the di-
rection and time to position the valve.
The staging function is used for two-position valves or elec-
tric heating (1 or 2 stages). The staging function uses the heat-
ing submaster reference from the PID and compares the value
to the Supply Air Temperature to calculate the required number
of output stages to energize.
For units using floating point valves, the floating point func-
tion compares the submaster reference from the PID loop to the
supply-air temperature to calculate the direction and time to
position the valve. Both outputs are not allowed to be ON
simultaneously.
The heating algorithm will control a modulating heating
valve to maintain the space temperature at the midpoint be-
tween the current low and high set points whenever dehumidi-
fication is active and reheat has been enabled. During this time,
a maintenance parameter will be set (reheat flag).
For two pipe changeover systems, the valve/DX output ter-
minations are used for a single water valve. IF/THEN logic de-
termines the routing of the control signals from the appropriate
heating or cooling algorithm to the cooling valve hardware out-
puts. The decision to route either heating or cooling is based
upon the Changeover Mode and the 2-pipe Changeover Sys-
tem configuration equal to Yes. The actual control type output
is determined by the configured Heat Type.
The Heating PID includes the following set points: Propor-
tional Gain, Integral Gain, Derivative Gain, Starting Value and
Fan Off Value.
Proportional Gain:Range
0.0 to 40.0
Default Value
8.0
Integral Gain:
Range
0.0 to 10.0
Default Value
0.3
Derivative Gain: Range
0.0 to 20.0
Default Value
0.0
Starting Value:
Units
Degrees F
Range
40.0 to 90.0
Default Value
80.0
Fan Off Value:
Units
Degrees F
Range
35.0 to 120.0
Default Value
55.0
NOTE: Default values are shown for Type 1 modulating
Heating. For other heating types, refer to the following:
Variable
2 Position/1 Stage Electric
2 Stage Electric
PG
40.0
40.0
IG
0.0
0.5
Starting
85.0
85.0
Value
To maintain a minimum temperature that may prevent a coil
freeze up on units located on an exterior wall, a configured fan
off value is used when the unit is Off. This feature is only appli-
cable to modulating heating and the Changeover Mode must be
Heating for two pipe changeover systems. Heat capacity will
be displayed as 0% and the Heating in Effect maintenance pa-
rameter will display NO during minimum duct temperature
control.
IMPORTANT: For 2-pipe systems, both heating and
cooling types must be the same (for example, both set to
1, modulating, or both set to 2, two-position).
→
1001