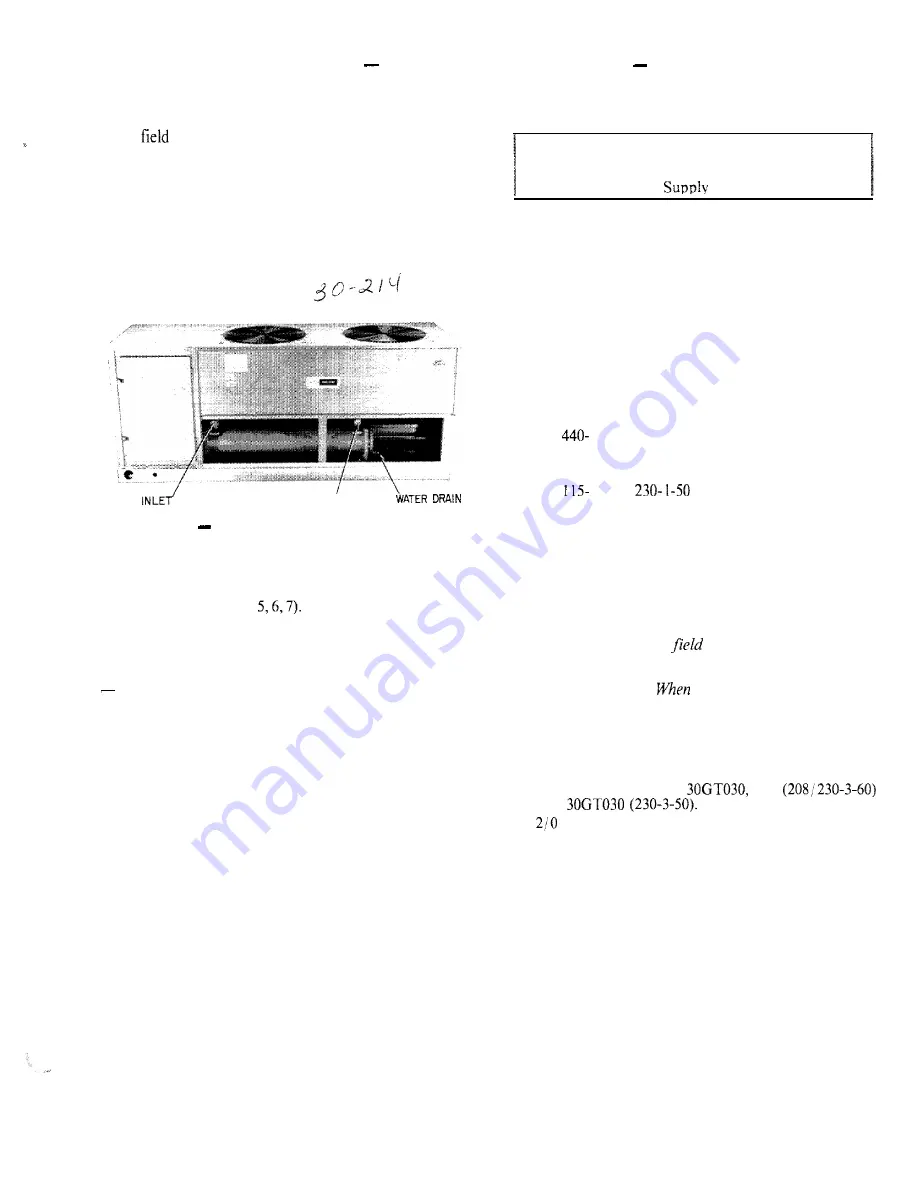
Chilled Water and Drain Piping
Facing the
cooler side of the unit, the return water connection is on
the left and the leaving water connection is on the right.
See Fig. 4, 5, 6, 7. A means of venting air from the high
point of the field-installed piping should be provided.
After
piping is complete, in area where piping is
exposed to low ambient temperatures (32F or below),
freeze-up protection is recommended using ethylene
glycol or electric heat tapes. Heat tapes should possess a
rating for area ambients and covered with a suitable
thickness of closed cell insulation. Route power for
heating tapes from a separate fused disconnect. Identify
disconnect as heat tape power source with warning that
power must not be turned off except when unit is being
serviced.
WATER
WATER OUTLET’
Fig. 4
Water Connection Locations
The cooler drain connection is at the opposite end from
the compressor (see Fig.
Insulate the drain piping,
similar to the chilled water piping, for at least one foot
(305 mm) from cooler.
PREPARATION FOR YEAR-ROUND OPERATION
If unit is on year-round operation, add sufficient
ethylene glycol to chilled water to prevent freezing under
operating ambient conditions. Consult local water
authority on characteristics of area water and add a
recommended inhibitor to the chilled water.
PREPARATION FOR WINTER SI-IIJTDOWN
Do
not shut off control power disconnect during off-season
shutdown.
At end of cooling season, drain water from
system. Replace drain plug and put 2 gallons (8 liters) of
ethylene glycol in cooler to prevent freezing of residual
water. Remove plug on top of leaving chilled water
nozzle to add glycol. At beginning of next chilling
season, refill cooler and add recommended inhibitor.
Power Supply
Electrical characteristics of avail-
able power supply must agree with unit nameplate rating.
Supply voltage must be within limits shown in Table 2.
IMPORTANT: Operating unit on improper supply
voltage, or with excessive phase imbalance, con-
stitutes abuse and may affect Carrier warranty. See
Unbalanced 3-Phase
Voltage, page 4.
Power Wiring
All power wiring must comply with
applicable local and national codes. Install field-supplied
branch circuit fused disconnect(s) per NEC (National
Electrical Code, U.S.) of a type that can be locked OFF
or OPEN. Disconnect(s) must be within sight from and
readily accessible from unit in compliance with NEC
Article
14.
GENERAL WIRING NOTES
1.
2.
3.
4.
5.
6.
The
l-60 or
control circuit power must be
from a separate source, through a field-supplied fused
disconnect rated at 7 amps.
Crankcase and cooler heaters are wired in the control
circuit so they are always operable as long as control
power supply disconnect is on, even if any safety
device is open or unit stop-start switch is off. Heaters
are wired ahead of stop-start switch. They are pro-
tected by 7-amp fuse in control power supply
disconnect.
The control circuit
supply disconnect should
never be open except when unit is being serviced or is
to be down for aprotongedperiod in which case cooler
should be drained.
operation is resumed, crank-
case heater should be energized for 24 hours before
start-up.
Power entry is at one end only.
Maximum field wire sizes allowed by lugs on terminal
block are:
350
MCM for Models
035
and
AWG for all other models.
Terminals for field power supply are suitable for
copper, copper-clad aluminum or aluminum con-
ductors. Insulation must be rated 167 F (75 C)
minimum.