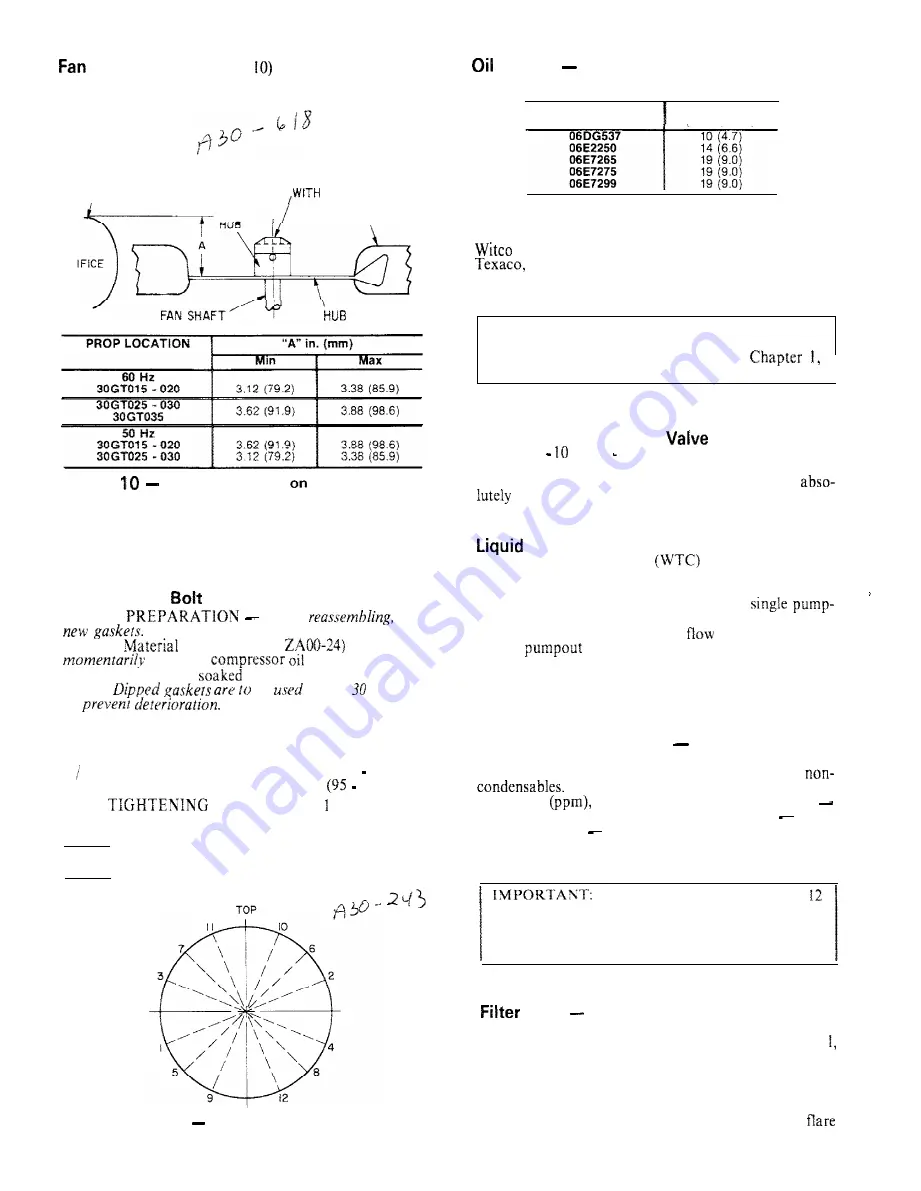
Adjustment
(See Fig.
Charge
Compressors are factory charged with
oil as follows:
TOP OF FAN ORIFICE
I
FILL HOLE IN FAN HUB
PERMAGUM
O R
FAN BLADE
PLATE
COMPRESSOR
A M O U N T
pints (titers)
When additional oil or a complete charge is required,
use only Carrier-approved compressor oil:
Chemical Corp.
. . . . . . . . . . . . . . .
Suniso 3GS
Inc.
. . . . . . . . . . . . . . . . . . . . .
Capella WF-32
Shrieve Chemical Co. . . . . . . . .
Zero1 150 (Synthetic)
IMPORTANT: Do not use drained oil or use oil that
has been exposed to atmosphere. Refer to Carrier
Standard Service Techniques Manual,
Refrigerants, for procedures to add or remove oil.
Fig.
Location of
Prop
Motor
Shaft
from Outside
of Orifice
Ring
Thermostatic Expansion
is factory set to
maintain 8
F (4.4 5.6 C) superheat of vapor leaving
cooler to control flow of liquid refrigerant to cooler.
Superheat can be reset but should be done only if
necessary.
Cooler Head
Tightening
GASKET
When
use
Compressed asbestos
neoprene gaskets
(Carrier
Specification
a r e t o b e
dipped in
prior to assembly.
Gaskets are nut to be
in oil as gasket deterioration
results.
be
within
minutes
to
BOLT TORQUE
The following torques are to be
applied during the bolt tightening sequence described
below:
I Z-in. diameter flange bolts . . . . . . . . . . . . 70 90 lb-ft
122
N-m)
BOLT
SEQUENCE (Fig. I)
The fol-
lowing is a recommended bolt tightening sequence:
Step I
Tighten moderately (without torquing) all the
flange bolts in the sequence shown.
Step 2
Repeat Step 1, tightening the bolts to the
specified torque.
Fig. 11
Tightening Sequence,
Cooler Head
Bolts
Line Solenoid Valve
is interlocked with the
water temperature controller
to shut off the flow
of refrigerant to the cooler when the water temperature
controller is satisfied. It is located immediately upstream
of the thermostatic expansion valve. With
out control, the compressor continues to run after WTC
is satisfied and the refrigerant
is shut off. This
causes
of refrigerant from the cooler and sub-
sequent shutdown of the compressor on low-pressure
control. The compressor does not restart until WTC
again calls for cooling.
Moisture-Liquid Indicator
Clear flow of liquid
refrigerant indicates sufficient charge in system. Bubbles
indicate undercharged system or presence of
Moisture in the system, measured in parts
per million
changes color of indicator: Green
moisture is below 45 ppm; chartreuse (caution)
45 to
130; yellow (wet)
above 130. Change filter drier at first
sign of moisture in the system.
Unit must be in operation at least
hours before moisture indicator can give an accurate
reading. With unit running, the indicating element
must be in contact with liquid refrigerant to give true
reading.
Drier
Whenever the moisture-liquid indicator
shows presence of moisture, replace filter drier. Refer to
Carrier Standard Service Techniques Manual, Chapter
Refrigerants, for details on servicing filter driers.
Liquid Shutoff/Charging Valve
is located imme-
diately ahead of filter drier, provided with I/4-in.
connection for field charging.
11