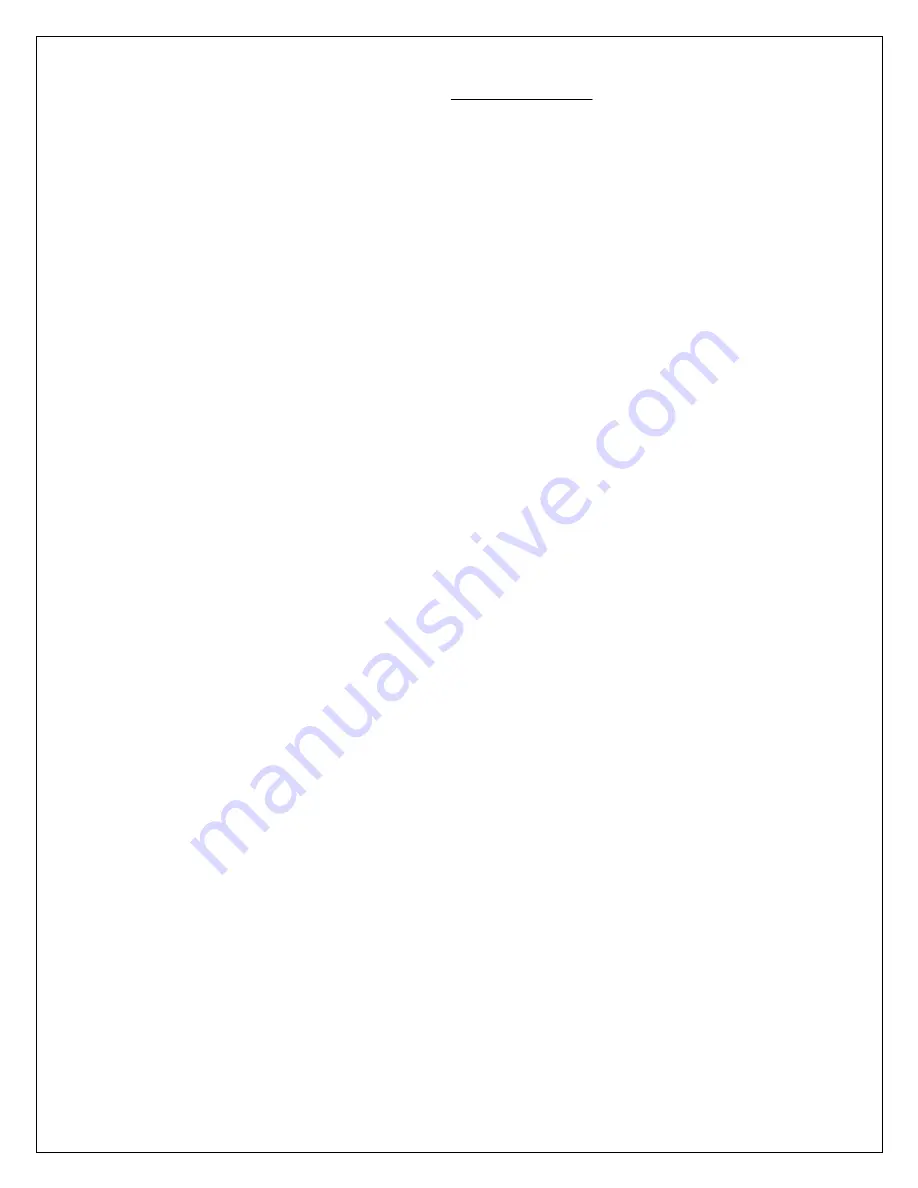
17
%
100
diameter
maximum
diameter
core
(446)
Core
×
=
6.5.3 (Note: This step can be skipped if
Diameter Select (442)
is set to External Diameter
Ratio). With an empty core loaded on the winder, start the line and run at full line
speed. Use a hand tachometer to measure the surface speed of the line. While
monitoring the surface speed of the empty core with the hand tachometer, increase
the speed reference to the Elite Pro (Analog Input 1 by default) until it matches the
surface speed of the line. Make note of the value of
Velocity Feedback Filtered
(198)
parameter in the Setup|Programming|Velocity Loop Section. Enter this value
into the
100% Winder Speed (444)
in the Setup|Programming|Applications|CTCW
Section. Decrease the reference to the Elite Pro and stop the line.
6.5.4 (Note: This step can be skipped if
Diameter Select
is set to Line/Winder. The
following assumes that the external diameter sensor is connected to Analog Input #2.
If other than this input is used, make changes to the following setup accordingly.)
Typically, the external diameter sensor should be configured to provide minimum
signal with an empty core and maximum signal with a full roll. In the
Setup|Programming|Inputs|Analog|Analog 2 Section, set
Analog Input 2 Destination
(24)
to
DiaRatio (445)
. With an empty core on the winder, perform the 0% calibration
under Calibrate Analog Input. Load or simulate a full roll and perform the 100%
calibration.
6.5.5 A signal proportional to line speed should be connected to one of the analog or
frequency inputs. (The following assumes that the line speed signal is connected to
the Frequency Input. If an input other than this is used, make changes to the following
setup accordingly.) In the Setup|Programming|Inputs|Frequency Section set the
Frequency Input Destination (63)
to
Line Speed (443)
. With the line stopped,
perform the 0% calibration under Calibrate Frequency Input. Next, run the line up to
full speed and perform the 100% calibration. The Bias and Gain parameter for the
analog or frequency input should be 0.00% and 100.00% respectively (default).
6.5.6 With the drive stopped, select torque mode by changing Setup|Programming|Current
Loop|
Drive Mode (109,110)
from Velocity to Torque. In the Setup|Programming|Misc
Parameters|Internal Links Section, modify
Internal Link 3 Source (370)
from
Ramp
Output (225)
to
Total Torque (455)
. (The above assumes that the factory preset
configuration is loaded.)
6.5.7 Navigate to the Setup|Programming|Applications|CTCW Section. Start the Elite Pro
drive with 0% line speed reference. Slowly increase the
Static Friction Torque (462)
parameter until the winder just begins to turn. Decrease slightly until the winder stops
turning. Increase the line speed to 100%. Slowly increase
Friction Compensation
(448)
until
Winder Speed (452)
is equal to or slightly above 100%. Use care to supply
only enough compensation to reach 100%.
6.5.8 The
Inertia Compensation (449)
adjustment is made to match the acceleration rate
of the winder to the acceleration rate of the line by compensating for inertia. This can
easily be done by using a dual trace oscilloscope (preferably storage type) to compare
the line and winder speed signals during acceleration. Otherwise, material can be
loaded and observed during acceleration. Slackening of the material indicates too little
compensation while tightening indicates too much compensation.
6.5.9 Material should now be loaded. The
Tension Setpoint (441)
should be adjusted to
provide the desired tension level on the material. Verify proper tension through
acceleration up to and at full line speed.
6.5.10 In many applications, the best rolls are "built" when tension is highest at the core and
mid-diameter and decreases or tapers off during the remaining diameter increase.
Taper Diameter (456)
sets the diameter level where tapering begins. The amount of
tapering is controlled by the
Taper Percentage (457)
parameter. These settings are
usually adjusted by winding material and observing the roll to determine the point at
which constant tension problems begin to occur. Most likely, any problem noticed at a
Summary of Contents for Elite Pro EPN020-000
Page 10: ...10 Figure 4 ...
Page 80: ...80 Prints ...
Page 81: ...81 ...
Page 82: ...82 ...
Page 83: ...83 ...
Page 85: ...85 ...
Page 88: ...88 ...
Page 89: ...89 ...
Page 90: ...90 ...
Page 91: ...91 ...
Page 92: ...92 ...
Page 93: ...93 ...
Page 94: ...94 ...
Page 95: ...95 ...
Page 96: ...96 ...
Page 97: ...97 ...
Page 98: ...98 ...
Page 99: ...99 ...
Page 100: ...100 ...
Page 101: ...101 ...
Page 102: ...102 ...
Page 103: ...103 ...
Page 104: ...104 ...
Page 105: ......
Page 106: ...106 PRO SOFT ...
Page 107: ...107 WARE BLOCK DIAGRAM ...
Page 108: ...108 ...