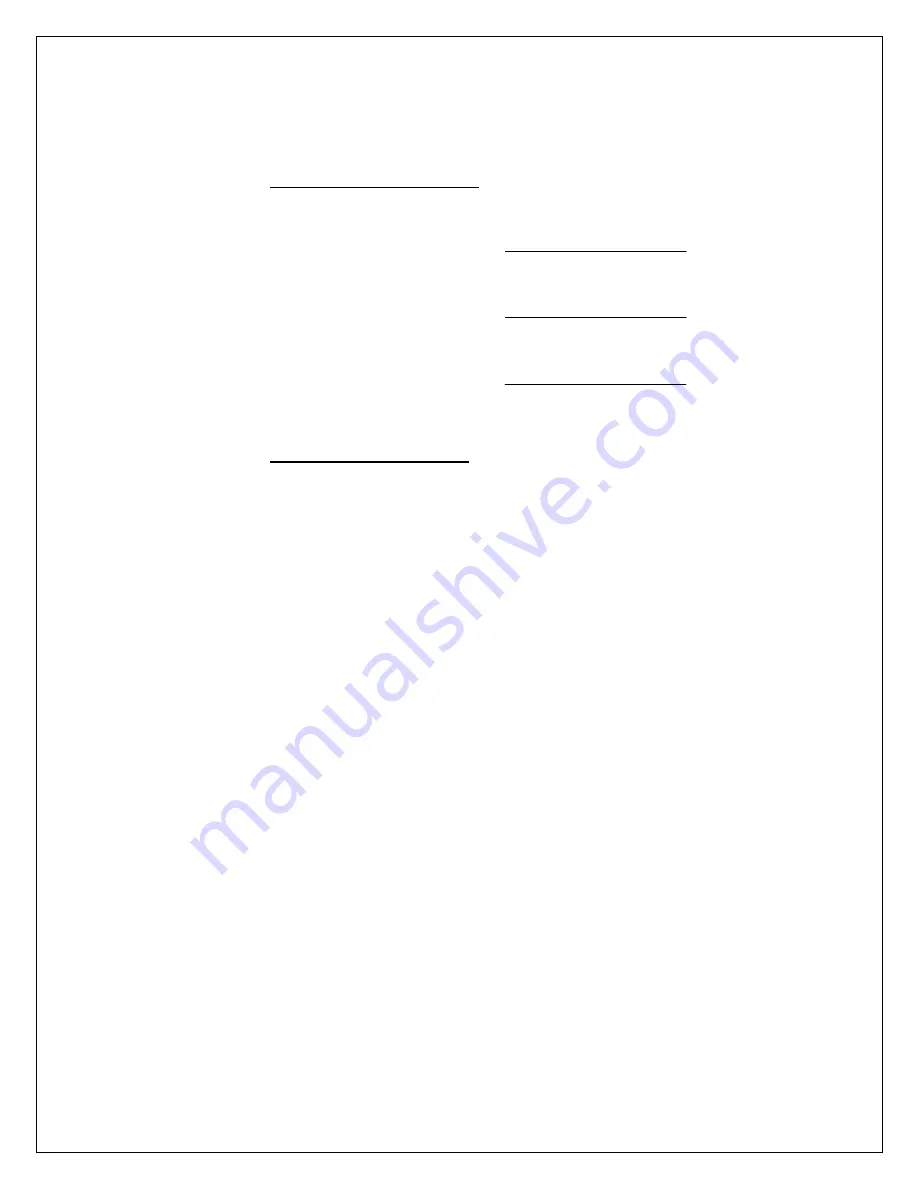
15
b. Set
Tachometer Type (127)
to AC or DC.
6.2.5 The field supply can operate in either closed loop current control or open loop voltage
control. Setup the field supply as follows depending on the desired mode of operation.
Note that the field setup parameters are under the Setup|Programming|Field Loop
section.
Closed Loop Current Control
a.
Set Field I Demand(339) as follows:
•
EPx020-000 thru EPx060-000 Models
100
8
×
=
A
Amps
Field
Nameplate
(339)
Demand
I
Field
•
EPx075-000 thru EPx150-000 Models:
100
10
×
=
A
Amps
Field
Nameplate
(339)
Demand
I
Field
•
EPx200-000 thru EPx600-000 Models:
100
12
×
=
A
Amps
Field
Nameplate
(339)
Demand
I
Field
b. Set
Open Loop Field Select (329)
to False.
Open Loop Voltage Control
a. Set
Field Economy Enable (332)
to False.
b. Adjust
Open Loop Field Setpoint (330)
until
Field Voltage (335)
equals
the motor nameplate rating.
c.
Set Field Economy Enable (332)
to True.
6.2.6 If parameters were not saved when exiting the programming section, navigate to
QP15 screen and select P2 to Save.
6.2.7 During the following steps the motor will be rotated. If excessive speed or wrong
direction of rotation could damage the load, it may be wise to de-couple the load until
proper control is verified. All parameters in this section are located in the
Setup|Programming|Velocity Loop section unless specified otherwise.
1. Momentarily close the Run pushbutton (Digital Input 1) at terminal 31. The armature
contactor should close. Slowly increase the external speed reference to approximately
20%. Observe the direction of rotation and if wrong, correct by removing control power
and reversing the motor armature or field wires. If used, observe proper polarization of
the series field winding per the instructions in Section 4.2.
2. Proper tachometer or encoder operation can be checked while running in Armature
Feedback (AFB). As above, run the drive at 20% speed. Monitor
Armature Feedback
(AFB, 194)
and compare this level with
Tachometer Feedback (TFB, 195)
or
Encoder Feedback (EFB, 196)
. If the levels are approximately equal, then TFB or
EFB can be selected with
Feedback Select (197)
when the drive is stopped. (The
following feedback parameters in this step are located in
Setup|Programming|Calibration Section.) If the TFB or EFB signals are the wrong
polarity, set
Invert FB (126)
to True. If the TFB level is not correct, verify proper
scaling per jumpers J5, J6, and J7. If an AC tachometer is used, set
Tachometer
Type (127)
to AC. If the EFB level is not correct, verify the
Encoder Lines (124)
and
100% Encoder RPM (125)
are set correctly.
3. If the drive is a regenerative model and the application requires reverse direction,
close the Reference Invert contact (Digital Input 4). Verify that the motor reverses
direction.
4. The Stop and Emergency Stop functions should be tested initially from a low
operating speed. Refer to Section 4.3 for descriptions of these stopping methods.
5. Run drive and increase the reference to maximum. Use the
Forward Max Speed
Scale (190)
and
Reverse Max Speed Scale (191)
to adjust for rated armature
Summary of Contents for Elite Pro EPN020-000
Page 10: ...10 Figure 4 ...
Page 80: ...80 Prints ...
Page 81: ...81 ...
Page 82: ...82 ...
Page 83: ...83 ...
Page 85: ...85 ...
Page 88: ...88 ...
Page 89: ...89 ...
Page 90: ...90 ...
Page 91: ...91 ...
Page 92: ...92 ...
Page 93: ...93 ...
Page 94: ...94 ...
Page 95: ...95 ...
Page 96: ...96 ...
Page 97: ...97 ...
Page 98: ...98 ...
Page 99: ...99 ...
Page 100: ...100 ...
Page 101: ...101 ...
Page 102: ...102 ...
Page 103: ...103 ...
Page 104: ...104 ...
Page 105: ......
Page 106: ...106 PRO SOFT ...
Page 107: ...107 WARE BLOCK DIAGRAM ...
Page 108: ...108 ...