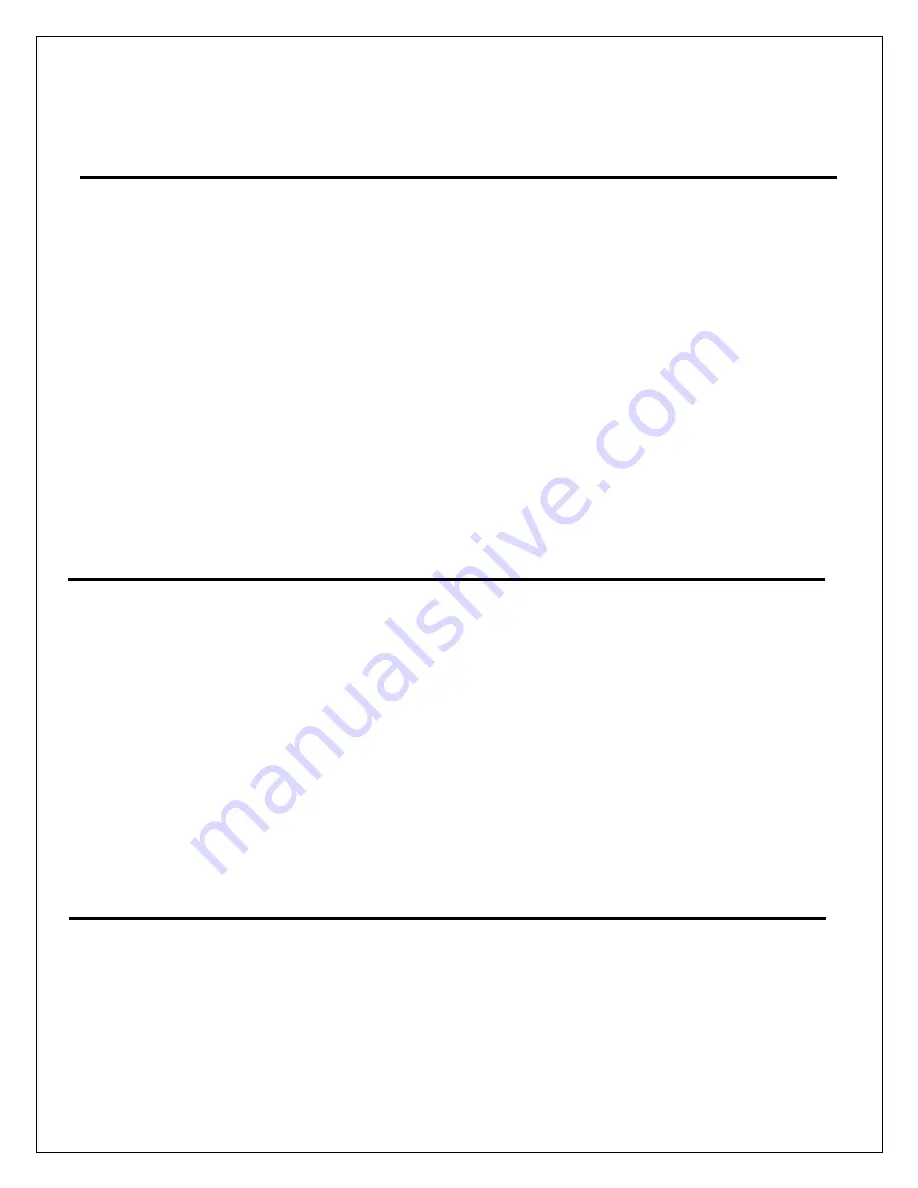
16
voltage or desired maximum motor speed. Stop the drive.
6. Test the Jog function (Digital Input 3) and adjust
Jog Reference (221)
(located in
Setup|Programming|Setpoints Section) for desired speed.
7.
If parameters were not saved when exiting the programming section, navigate to
QP15 screen and select P2 to Save.
6.3 Adjustment Procedure: Constant Horsepower
6.3.1 Initially setup Elite Pro as a Velocity Regulator via Section 6.2 to run at the motor's
base speed via tachometer or encoder feedback with closed loop field control.
6.3.2 In the Setup|Programming|Field Crossover Section, set the following:
a.
Field Crossover Enable (423)
to True
b.
Min Field Current Demand (424)
to nameplate top speed field current.
6.3.3 Go to the Setup|Programming|Velocity Loop section and set
100% RPM Level (199)
to the new top speed motor RPM. Go to the Setup|Programming|Fault Logic section
and set
Velocity Feedback Loss Inhibit (248)
to True.
6.3.4 If using a tachometer for feedback, rescale the tach voltage feedback to the top speed
voltage via jumpers J5,6 & 7 on control board. Otherwise, rescale the encoder
feedback by changing Setup|Programming|Calibration|
100% Encoder RPM (125)
to
the new top speed motor RPM.
6.3.5 If parameters were not saved when exiting the programming section, navigate to
QP15 screen and select P2 to Save.
6.3.6 Start drive and slowly increase the external speed reference. Field Current should
slowly begin decreasing when the
Armature Feedback (194)
reaches the
Field
Crossover Setpoint (425)
which is typically set to 85%. Continue increasing external
speed reference to maximum and verify rated armature voltage and top speed field
current levels.
6.4 Adjustment Procedure: Torque Regulator
6.4.1 Adjust external torque reference (Analog Input 1) at terminal 10 to 0 volts.
6.4.2 Apply A.C. power to the control.
6.4.3 Using the HMI, go to the Setup|Programming|Calibration section and set the following
parameters to match the nameplate values:
Nameplate Motor Armature Current (123)
Nameplate Motor Armature Voltage (128)
6.4.4 Setup Field output via Section 6.2.5.
6.4.5 Go to the Setup|Programming|Current Loop section, and set
Drive Mode (109,110)
to
Torque.
6.4.6 If desired, go to the Setup|Programming|Accel/Decel section, and set desired
accel/decel settings. Overspeed protection can be tailored by adjusting the
Overspeed Level (223)
in the Setup|Programming|Fault Logic section.
6.4.7 If parameters were not saved when exiting the programming section, navigate to
QP15 screen and select P2 to Save.
6.4.8 Drive setup is now complete. Momentarily pressing the Run pushbutton will start the
drive and provide torque commanded by the external reference.
6.5 Adjustment Procedure: CTCW (Constant Tension Center Winder)
6.5.1 Verify proper connection and operation of the Elite Pro by setting up the drive as a
velocity regulator (refer to section 6.1 and 6.2).
6.5.2 In the Setup|Programming|Applications|CTCW Section, set the following:
a.
Diameter Select (442)
depending upon the desired diameter calculation
method.
b.
Diameter Memory Reset (447)
to True.
c.
Tension Setpoint (441)
to 0.00%.
d.
Core (446)
to the ratio of the core diameter to that of the max diameter:
Summary of Contents for Elite Pro EPN020-000
Page 10: ...10 Figure 4 ...
Page 80: ...80 Prints ...
Page 81: ...81 ...
Page 82: ...82 ...
Page 83: ...83 ...
Page 85: ...85 ...
Page 88: ...88 ...
Page 89: ...89 ...
Page 90: ...90 ...
Page 91: ...91 ...
Page 92: ...92 ...
Page 93: ...93 ...
Page 94: ...94 ...
Page 95: ...95 ...
Page 96: ...96 ...
Page 97: ...97 ...
Page 98: ...98 ...
Page 99: ...99 ...
Page 100: ...100 ...
Page 101: ...101 ...
Page 102: ...102 ...
Page 103: ...103 ...
Page 104: ...104 ...
Page 105: ......
Page 106: ...106 PRO SOFT ...
Page 107: ...107 WARE BLOCK DIAGRAM ...
Page 108: ...108 ...