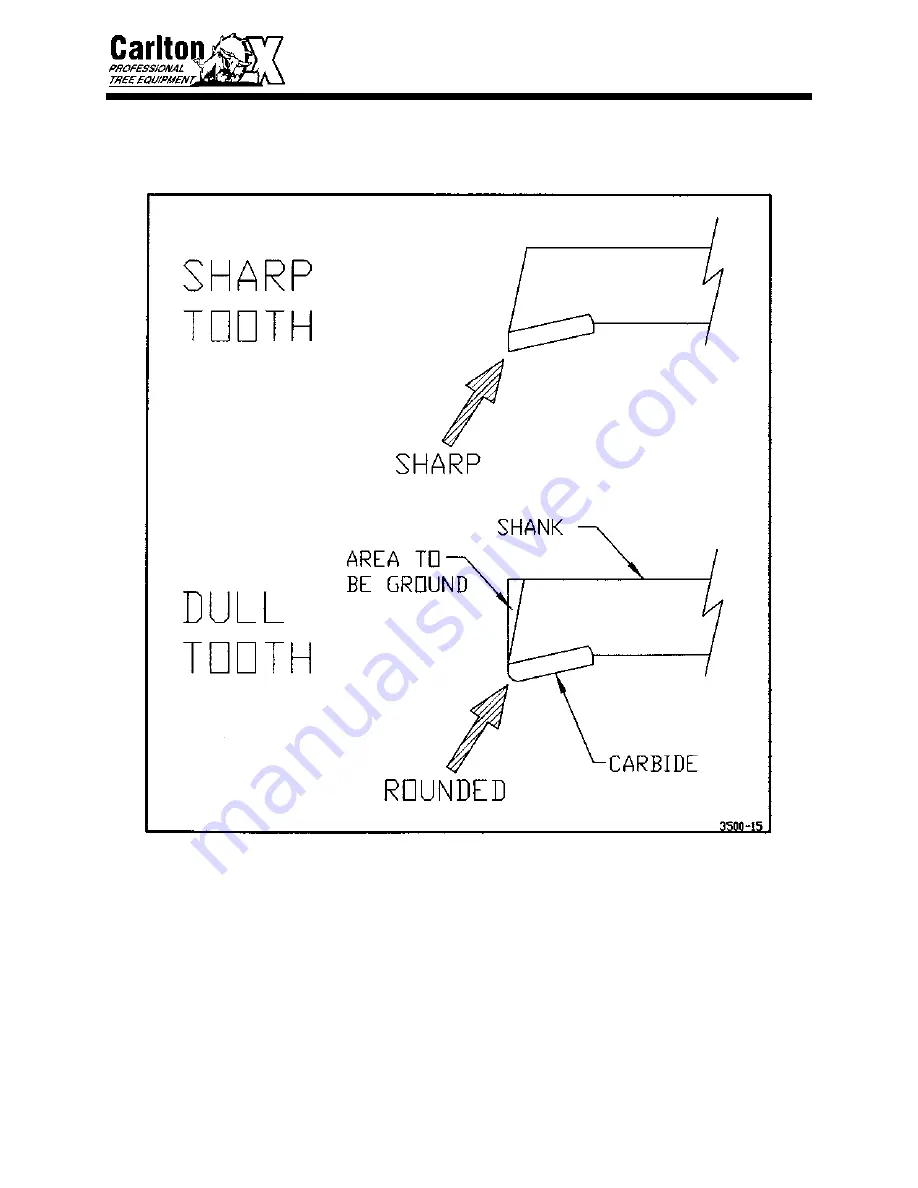
SP8018
TRX
SERVICING CUTTER WHEEL
44
TOOTH SHARPENING
Begin by chamfering shank back past edge of carbide. You do this because if it is
not back far enough the shank will hit the stump instead of the carbide, thus
causing a lot of vibration. Once the shank is angled far enough back, then begin
sharpening carbide.
•
Cut shank with a standard rock and cut carbide with a silicone carbide or diamond
rock.
CAUTION: GRINDING CARBIDE CAN BE A HEALTH HAZARD. Use facemask to
prevent breathing in harmful material while grinding.
Summary of Contents for SP8018 TRX
Page 2: ......
Page 4: ......
Page 5: ...SP8018 TRX SAFETY ALERT ...
Page 6: ......
Page 7: ...SP8018 TRX SAFETY ALERT ...
Page 8: ......
Page 9: ...SP8018 TRX SAFETY ALERT ...
Page 10: ......
Page 11: ...SP8018 TRX SAFETY ALERT ...
Page 12: ......
Page 14: ......
Page 16: ......
Page 18: ......
Page 20: ......
Page 25: ...SP8018 TRX MACHINE SPECIFICATIONS 5 ...
Page 57: ...SP8018 TRX SERVICING BELTS 37 Replacing Poly Chain Belt ...
Page 70: ...SP8018 TRX MACHINE WIRING 50 REMOTE WIRING DIAGRAM ...
Page 73: ...SP8018 TRX BOOM ASSEMBLY 53 ENGINE SLIDE ASSEMBLY ...
Page 75: ...SP8018 TRX BOOM ASSEMBLY 55 ...
Page 79: ...SP8018 TRX BOOM ASSEMBLY 59 ...
Page 86: ......
Page 87: ......
Page 88: ......
Page 89: ......
Page 90: ......
Page 91: ......
Page 92: ......
Page 93: ......
Page 94: ......
Page 95: ......
Page 96: ......
Page 97: ......
Page 98: ......
Page 99: ......
Page 100: ......
Page 101: ......