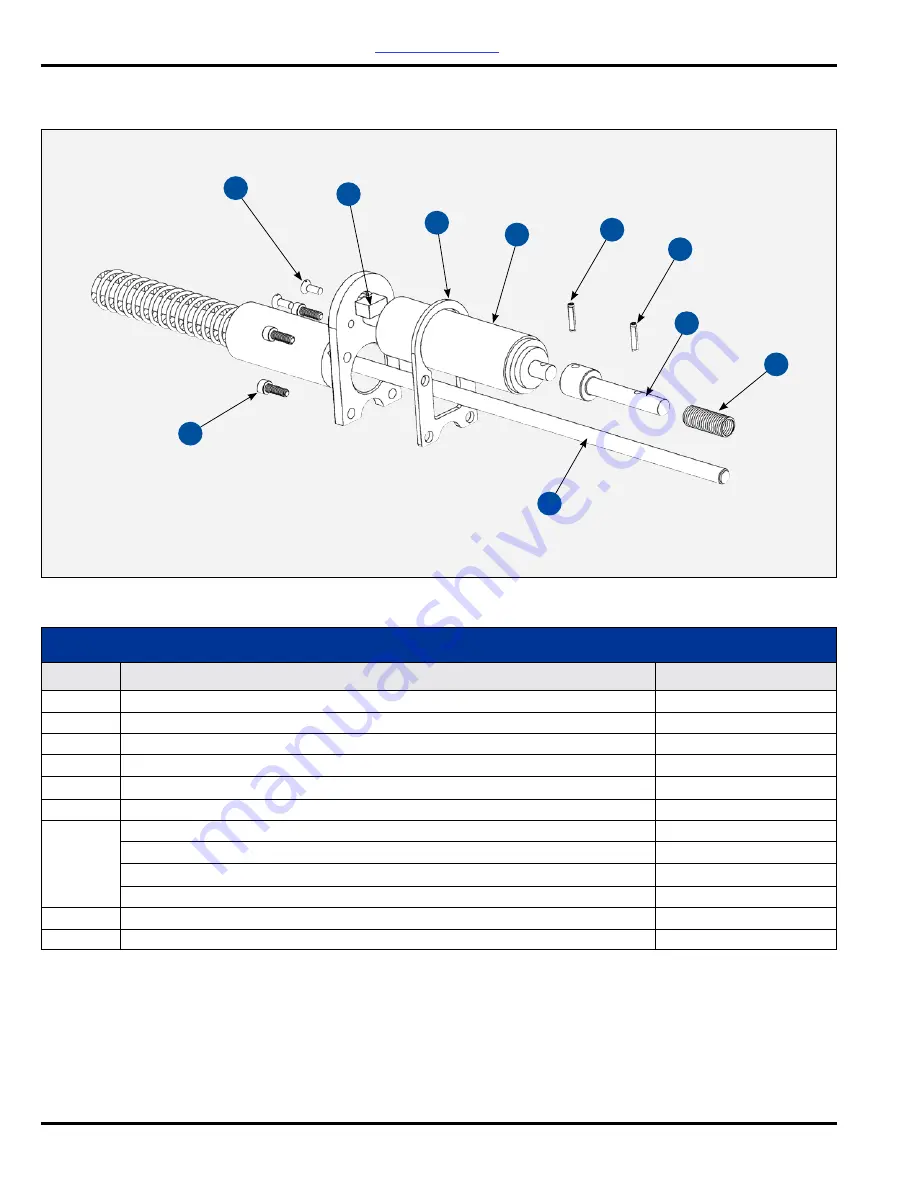
PARTS IDENTIFICATION
EN
AH-13-01-R8 (09/2022)
42 / 55
www.carlisleft.com
Figure 27: Cable /Motor Parts List
Item #
CABLE / MOTOR PARTS LIST
(Figure 27)
Description
Part #
1
Spring Pin
4359-01
2
Spring
8491-00
3
Adaptor, Drive
75757-00
4
Assembly, Electric Motor No. 2
3639-00
5
Gasket, No. 2 Handgun
3968-00
6
SHCS #8 Screw (4) Required
8301-16C
7
Assembly, Cable No. 2 Electric Motor (With Motor & Switch/Without)
7.6 m (25’) length
19371-25 / 19370-25
11 m (36’) length
19371-36 / 19370-36
15.2 m (50’) length
19371-50 / 19370-50
8
Switch
4125-00
9
Screw, Flat HD. #10
9157-24F
5
8
1
9
4
1
7
2
3
6