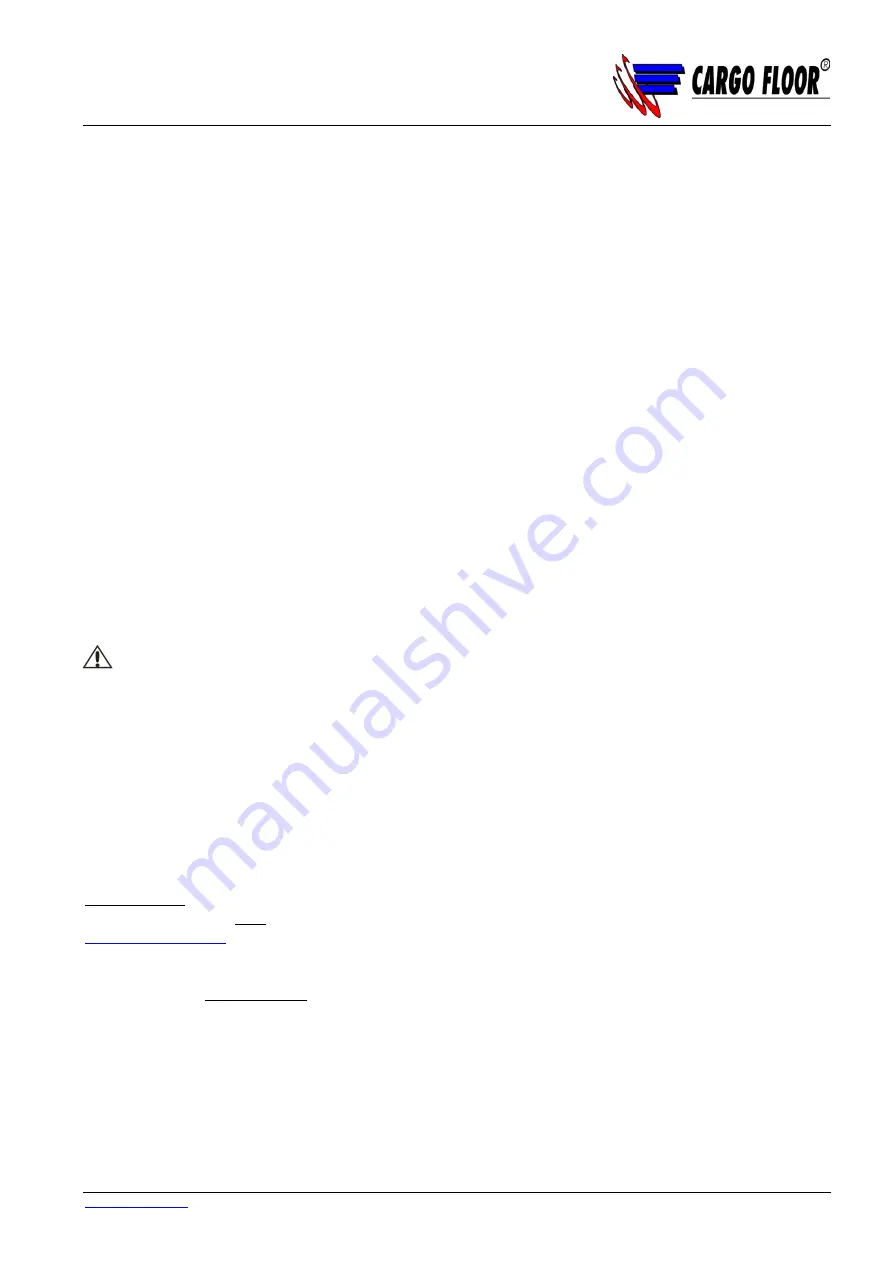
Cargo Floor B.V.
Byte 14
NL-7741 MK COEVORDEN
Phone:+31 (0)524-59 39 00
www.cargofloor.com
Replacing a cylinder CF500 SL-2 / CF500 SL-C
10-12-2013
/ NL 5 van 16
T)
Check that the correct type and quality of hydraulic oil is used. The use of incorrect oil type may cause
damage to the Cargo Floor system and the pump.
U)
Check the vehicle for correct voltage. Make sure there are no open electrical connections. A faulty
electrical system can cause damage to the Cargo Floor system and the vehicle.
V)
Check that the bulkhead, if present, is functioning smoothly and properly. A properly functioning
bulkhead ensures that the product is unloaded in a clean and quick fashion. A malfunctioning bulkhead
may extend the unloading time and cause damage to the vehicle.
W)
Use of the Cargo Floor system by unqualified personnel can cause damage to the Cargo Floor system and
the vehicle.
X)
Excessively high oil temperatures will cause damage to the Cargo Floor system and other hydraulic
components, such as the pump.
Y)
It is at all times advisable to stop the Cargo Floor system when all the piston rods are retracted. This is
usually the case when the floor profiles are positioned towards the unloading end (vehicle doors).
Unretracted piston rods may cause damage to the Cargo Floor system.
Z)
To prevent damage to the floor profiles, exercise caution and limit the dump height as much as possible.
The transport of unauthorized goods, such as aggressive, corrosive, hot, hard, sharp and viscous materials
may cause damage to the Cargo Floor system and the vehicle. Avoid loading and unloading sharp objects.
Loads that are softer than the hardness of the floor profiles will extend the service life of your system; if
in doubt, use a protective cloth or consult your dealer.
AA)
Forklift trafficable. In principle, the floors are completely trafficable and can be driven over by forklifts,
but always consult your dealer for advice on the maximum loads allowed on your vehicle.
Overloading will cause damage to the Cargo Floor system and the vehicle.
BB)
Always return emergency control(s) to their original non-activated position after use.
CC)
During the operation of the system, test the temperature of the oil by touching the side of the tank. If the
oil is so hot that you cannot continue to touch the tank, switch off the pump to allow the oil to cool off
and determine what is causing the overheating. Stop loading or unloading if the oil is too hot, as this will
irreversibly cause damage to the Cargo Floor system and the other hydraulic components.
WARNING: TOUCHING OVERHEATED OIL AND COMPONENTS CAN CAUSE BURNS AND
INJURIES!
DD)
During loading and unloading operations, the load should be spread to give an even weight distribution
over the floor area, otherwise the load may stall. Tip: when transporting pallets, place softwood boards of
300 x 18 x 2350 mm [12” x 0.75” x 92.5”] to distribute the pressure more evenly.
EE)
The constant pressing of the load against the head board or the doors can lead to extra wear of the
complete system. Also the construction can be damaged. Please consult you supplier about the optimizing
possibilities or in order to prevent problems occurring.
FF)
The user/operator/driver that is operating the Cargo Floor system is compelled to remain a safe distance
from the Cargo Floor system at all times, from the time of switching on the hydraulic pump until turning
it off. He should ensure that no dangerous situations can occur. When the process malfunctions or if other
people are present he should shut down the Cargo Floor system, or hydraulic pump, immediately
.
WARRANTY:
Warranty is subject to prior approval by Cargo Floor B.V.! To request warranty coverage, visit
to fill out and submit the warranty application form provided there; do not forget to
include your Cargo Floor system number on the form.
In the event of an EMERGENCY, operation of the Cargo Floor system can be halted as follows:
By pressing the stop button on the wired remote control unit;
By turning all switches to position “0”;
By putting the handle of the control valve in the middle position (only B and A control);
Turning off the pump;
Turning off the main switch of the power supply;
Turning off the motor of the electro-hydraulic aggregate;