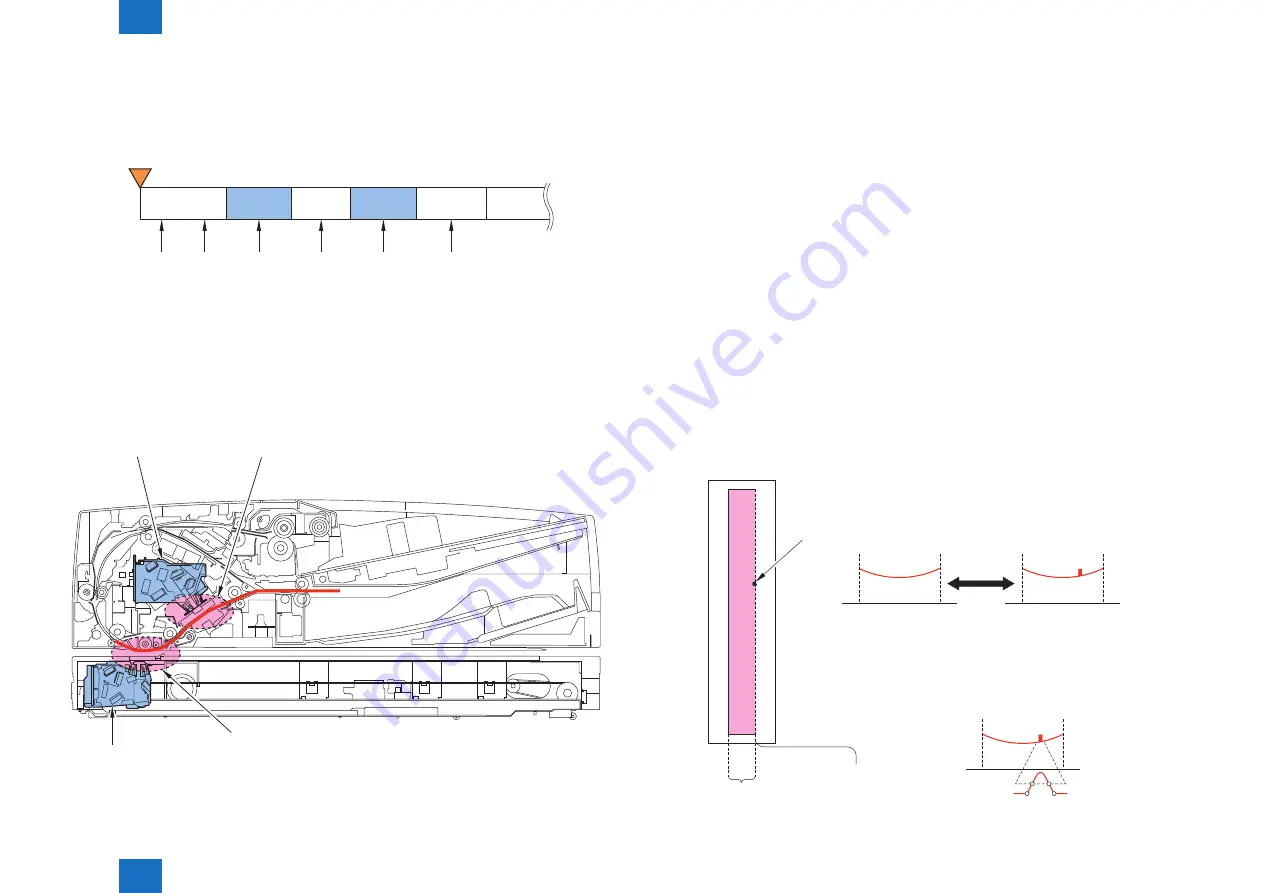
2
2
2-34
2-34
Technology > Controls > DADF > Original Scanning Assembly
Technology > Controls > DADF > Original Scanning Assembly
●
Dust Detection Control
Overview
The timing of dust detection is as follows.
[2]
[1]
[2]
[2]
[3]
[3]
Start key
ON
Before stream
reading
1st sheet
scanned
2nd sheet
scanned
Between
sheets
After scan
Standby
[1]
White plate dust detection control
[2]
Steam reading glass / Scanning glass dust detection control,
Dust detection correction control (continuous lines)
[3]
Dust detection correction control (noncontinuous lines)
Scanner unit
(DADF)
- White plate dust detection
- Stream reading glass dust detection
- Dust detection correction (continuous lines)
- Dust detection correction (noncontinuous lines)
Scanner unit
(Reader)
- White plate dust detection
- Scanning glass dust detection
- Dust detection correction (continuous lines)
- Dust detection correction (noncontinuous lines)
F-2-68
F-2-69
White plate dust detection control
In this machine, the fans cool down the inside of the DADF to prevent the overheating at
stream reading operation. As a result, dust in the DADF may stick to the white plate and it
may cause the lines on the image.
To reduce the influence from the dust, the white plate dust detection and correction are
performed.
(1) White plate dust detection
The machine compares the shading coefficient obtained from shift shading and the shading
coefficient obtained from fixed shading to identify the presence/absence of dust and, if any,
identifies the coordinates and width of the area.
(2) White plate dust correction
If the machine detects the dust as a result of white plate dust detection, it interpolates the
shading coefficient of the area using the shading coefficient of both sides so as to decrease
the effects of the presence of dust. It executes the shading correction using the shading
coefficient obtained after the interpolation.
When the dust is detected as a result of white plate dust detection, the machine interpolates
the shading coefficient of the dust area using the shading coefficient of both sides so as to
reduce the effects of the dust. The shading correction is executed after the interpolation.
[Detection Algorithm]
[Correction Algorithm]
Computation of shading
coefficient
(shift shading to
reference area)
Computation of shading
coefficient
(from fixed shading to
shading correction position)
Detection of coordinates of
start of dust and width
Correction of dust area
coefficient using data of both sides
- Fixing shading
position
- Shading correction
position
Reference area
(Shading coefficient
computation area)
White plate
Area
of dust
Comparison
F-2-70
Summary of Contents for F-1
Page 14: ...2 2 Technology Technology Basic configuration Controls Service Work ...
Page 72: ...3 3 Periodic Servicing Periodic Servicing Periodic Servicing List ...
Page 135: ...5 5 Adjustments Adjustments Overview Adjustment Method ...
Page 175: ...Appendix Service Tools General Circuit Diagram ...