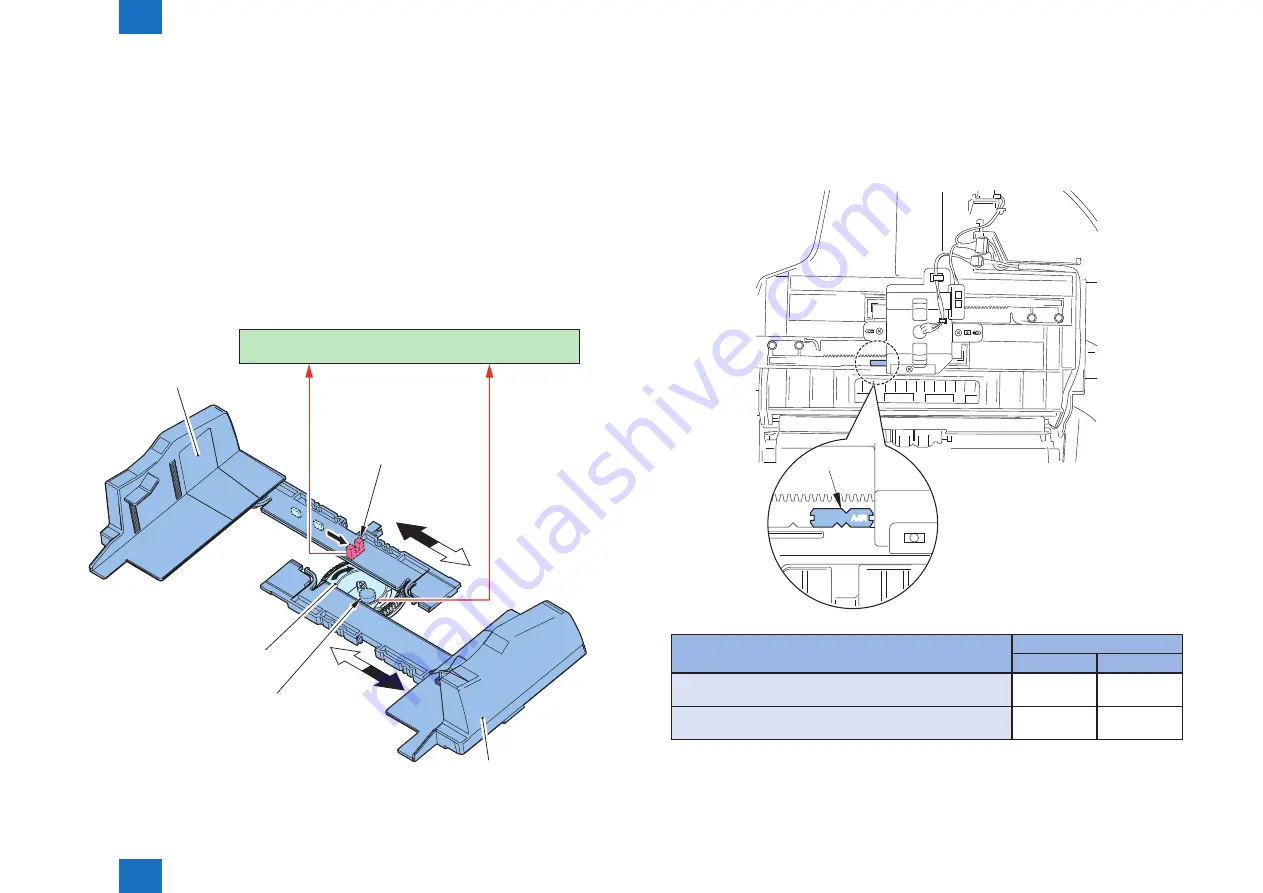
2
2
2-39
2-39
Technology > Controls > DADF > Original Size Detection
Technology > Controls > DADF > Original Size Detection
Detection of width direction
The size of original in width direction is detected by the original width volume (VR) and the
AB/ Inch identification sensor (SR7) on the original pickup tray.
The original width volume (VR) operates together with the slide guide and its resistance value
is changed to analog as the slide guide is moved. The DADF driver PCB (PCB1) reads these
changes in resistance as the original size signal (VR) and converts it into the size in width
direction.
The AB/ Inch identification sensor (SR7) is installed inside the original pickup tray to perform
the width detection between A4 and LTRR, or between A5R and STMTR correctly on the
original width volume (VR). The AB/ Inch identification sensor (SR7) outputs AB/ Inch
detection signal (A4LT_S) “1” when the original width is “127 mm or longer and shorter than
148 mm” or “197 mm or longer and shorter than 214 mm”.
AB/Inch determination
sensor (SR7)
Original width volume (VR)
A
4L
T_
S
V
R
Slide guide
(Front)
Slide guide
(Rear)
Gear
DADF driver PCB
F-2-79
The stop position of the slide guide can be changed by changing (turning around) the
attaching of the positioning roll [1] of the slide guide as shown below.
There is a groove on the rail of the slide guide so that the slide can stop at specific default
sizes. Some sizes, however, are extremely close to each other, possibly causing the slide
to stop at the wrong position. To make sure that the slide is at the correct position, the stop
position is adjusted with the positioning roll [1].
[1]
A4R
A4R
Engraved mark of slide guide positioning wheel (surface)
Stop position of slide guide
1 groove
2 grooves
A4R
A4R
A4R
LTRR
INCH
LTRR
A4R
LTRR
F-2-80
T-2-16
Summary of Contents for F-1
Page 14: ...2 2 Technology Technology Basic configuration Controls Service Work ...
Page 72: ...3 3 Periodic Servicing Periodic Servicing Periodic Servicing List ...
Page 135: ...5 5 Adjustments Adjustments Overview Adjustment Method ...
Page 175: ...Appendix Service Tools General Circuit Diagram ...