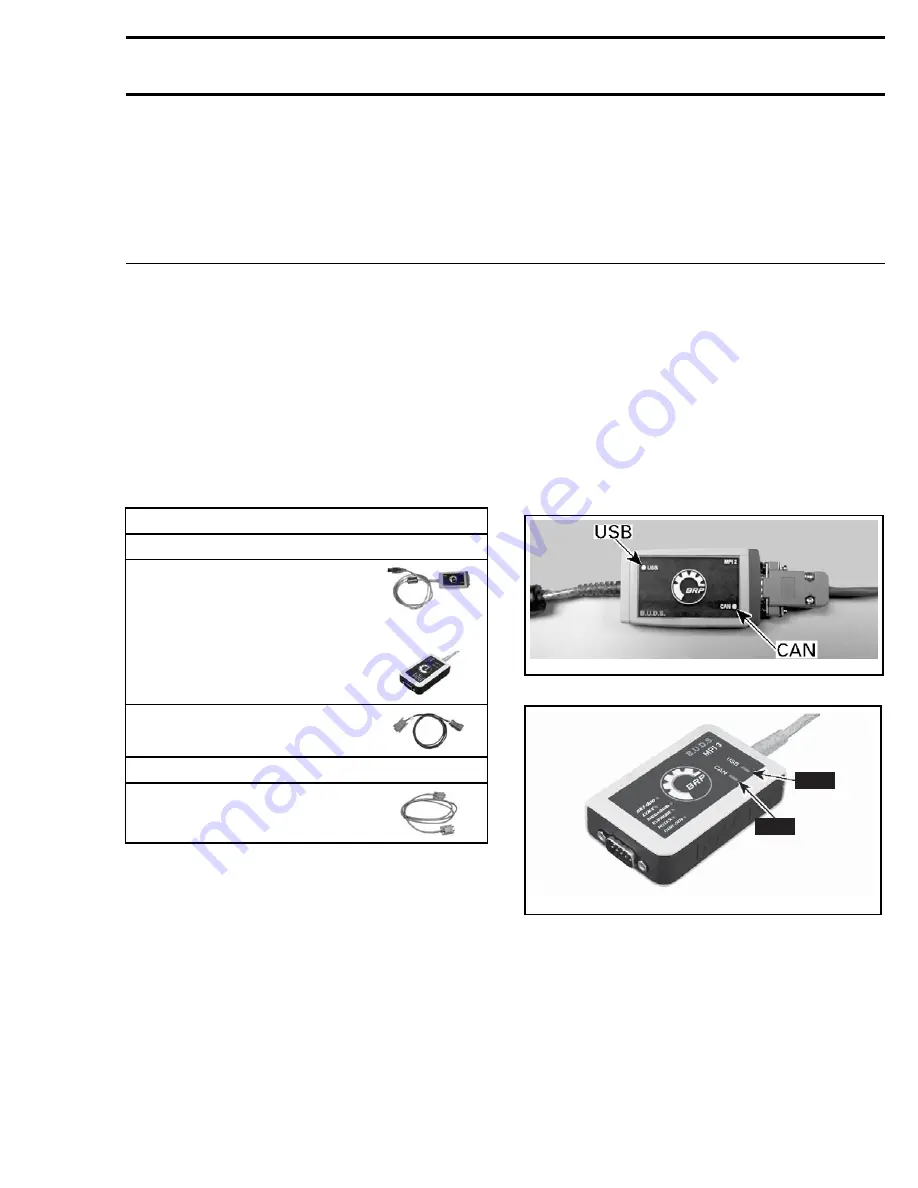
Subsection 03 (COMMUNICATION TOOLS AND B.U.D.S.)
COMMUNICATION TOOLS AND
B.U.D.S.
SERVICE TOOLS
Description
Part Number
Page
DIAGNOSTIC CABLE ....................................................................
710 000 851 ......................................... 1, 3
MPI-2 INTERFACE CARD ..............................................................
529 036 018 ............................................. 1
MPI-3 INTERFACE CARD ..............................................................
529 036 353 ............................................. 1
GENERAL
Refer to
PROCEDURES
for instructions on the
communication tools.
If communication problems occur, refer to
TROU-
BLESHOOTING
in this subsection.
REQUIRED TOOLS
MANDATORY TOOLS
A personal computer (laptop or desktop)
MPI-2 INTERFACE CARD
(P/N 529 036 018)
OR
MPI-3 INTERFACE CARD (P/N 529
036 353)
DIAGNOSTIC CABLE
(P/N 710 000 851)
OPTIONAL TOOL
Extension cable
available at electronic retail outlets.
Do not exceed 7.5 m (25 ft)
TROUBLESHOOTING
DIAGNOSTIC TIPS
IMPORTANT:
Make sure all connections are
made and vehicle is powered up
before starting
B.U.D.S.
to allow proper communication between
the vehicle and the BRP Utility and Diagnostic
Software (B.U.D.S.)
Multi-Purpose Interface Card
Connection Troubleshooting
MPI Status Lights
The MPI card includes 2 status lights that indicate
the connection condition: USB and CAN.
Both
lights must be GREEN
to function properly. Oth-
erwise, refer to the following charts.
vdd2006-001-151_b
MPI-2 CARD
CAN
USB
vmr2016-128-001_a
MPI-3 CARD
Prerequisite for USB Communication:
– PC Computer turned on.
– MPI card connected to PC computer.
vmr2016-128
1