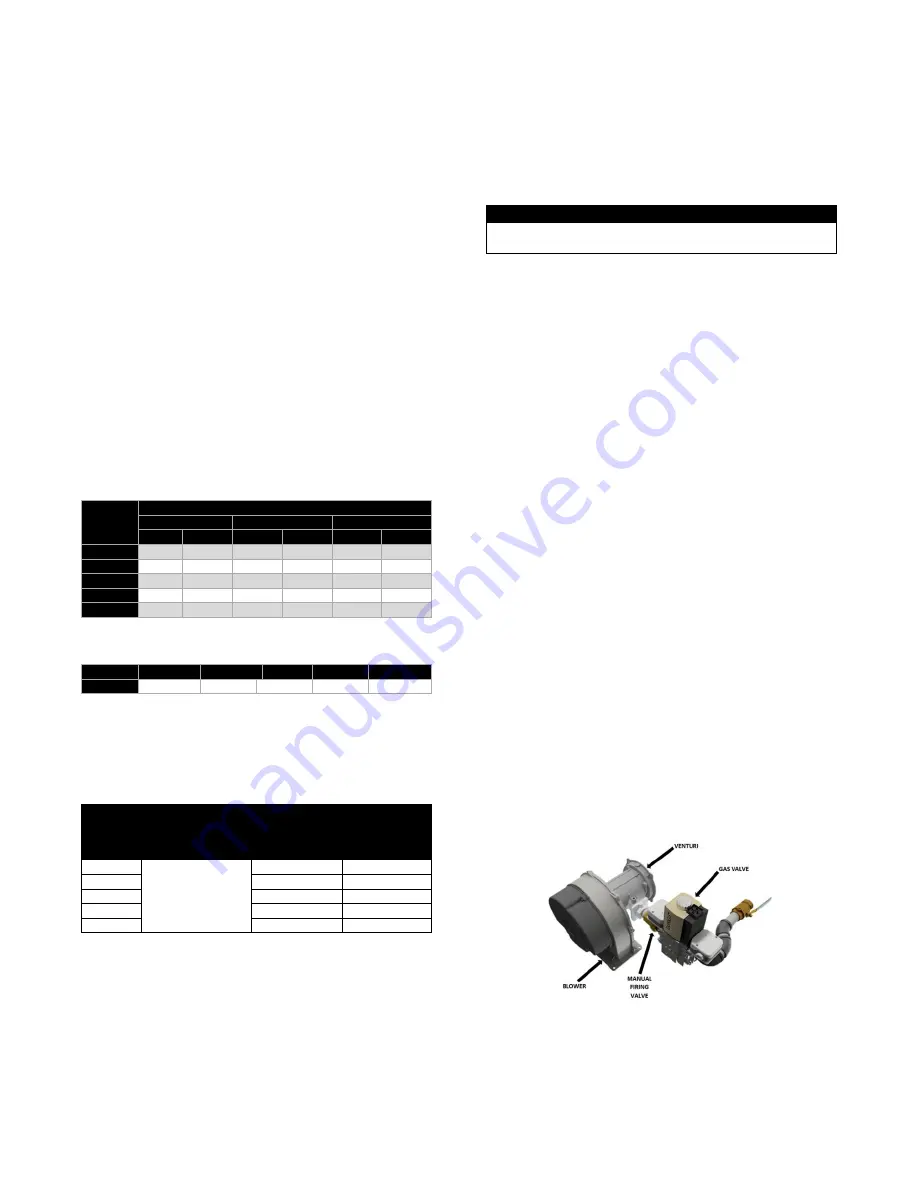
12
single-pass, counter-flow, fire-tube design. Models 400
MBH throughout 850 MBH are designed to withstand 160
PSIG of operating pressure.
∆T HEAT EXCHANGER ALGORITHM
The Valiant FT Series 2 is constantly monitoring the inlet
and outlet water temperatures.
When the ∆T approaches
60°F the burner will modulate down to prevent tripping of
the high limit and to protect the heat exchanger against
thermal shock. This setting may be changed in the Valiant
FT Series 2 control.
LOW WATER TEMPERATURE SYSTEMS
In applications where the heating system requires supply
water temperatures below 110°F, connections may be
made directly to the Valiant FT Series II. At incoming
temperatures of 120°F or lower this appliance achieves
maximum efficiency. Inlet temperatures must not drop
below 40°F to prevent freezing.
2.4.6 Flow and pressure drop at a given
∆T
Table 8: Valiant-FT Series II Flow and Pressure Drops
vs
∆T
Input
KBtu/hr
Flow and Pressure Drop at given
∆T
20°F
30°F
40°F
GPM
∆P
GPM
∆P
GPM
∆P
400
39.6
4.2
26.4
2.8
19.8
3.0
500
49.5
4.3
33
3.9
24.7
3.9
600
59.4
5.7
39.6
4.5
29.7
3.0
725
71.7
5.8
47.8
3.6
35.9
4.7
850
84.1
6.1
56.1
3.9
42
3.8
Table 9: Valiant-FT Series II Minimum Flow
Model
400
500
600
725
850
US GPM
13.2
16.5
19.8
23.9
28.0
2.5
ELECTRICAL CONNECTIONS
2.5.1 Minimum Power Requirements
Table 10: Minimum Power Requirements
Model
Voltage
Requirement
Full Load
Amps
[Amperes]
Maximum
Over
Protection
[Amperes]
400
115VAC, 60Hz,
Single Phase
7
15
500
7
15
600
7
15
725
7
15
850
7
15
The appliance, when installed, must be electrically
grounded in accordance with the requirements of the
authority having jurisdiction or in the absence of such
requirements, with the latest edition of the National
Electrical Code ANSI/NFPA No. 70. When the unit is
installed in Canada, it must conform to the Canadian
Electrical Code, C22.1, Part 1 and/or local Electrical Codes.
All wiring between the appliance and field installed devices
shall be made with wire having minimum 220ºF (105ºC)
rating. Line voltage wire external to the appliance must be
enclosed in approved conduit or approved metal clad cable.
To avoid serious damage,
DO NOT ENERGIZE
the
appliance until the system is full of water. Ensure that all air
is removed from the pump housing and piping before
beginning initial operation. Provide the appliance with
proper overload protection.
WARNING
This product must be properly grounded before any
electric current is applied to the blower or controls.
BLOWER MOTOR
The Valiant FT uses a 120V/1PH electrical supply to power
the blower motor. On ignition, after safety checks are
complete, the blower is provided with a signal to operate at
soft start level for burner ignition. After main burner ignition
is established, the motor receives a modulating signal from
the control corresponding to the rate of modulation
necessary.
AIR
PRESSURE
SWITCH,
BLOCKED
FLUE
&
CONDENSATE SWITCH
The air proving switch and blocked venting switch are wired
in series. When the error on the control shows “Air Switch
Open”, it could be a result of these switches. A minimum
pressure across the differential air switch proves the
combustion air fan. A failure of this switch to close could be
due to several factors such as, sensing line broken or loose
fitting, blocked vent, steady high wind condition or an
incorrectly set switch.
The Blocked Flue & Condensate switch is mainly due to a
blocked air intake or vent condition. When the blocked flue
switch has tripped, check the venting and/or air intake
piping for obstructions before placing the unit into operation.
Power must be shut off to the boiler and gas supply to the
appliance must be closed before attempting to investigate
reason for blocked flue condition.
PART 3 COMBUSTION COMPONENTS
Figure 19: Combustion Components Assembly
(VA600-850 gas train displayed)
3.1
AIR/ GAS RATIO CONTROL VALVE
Operation of the gas valve in combination with the
combustion air fan allows the burner input rate to vary from
Summary of Contents for Valiant-FT II Series
Page 2: ...99 0419 Rev 00...
Page 40: ...36 PART 9 PIPING DIAGRAMS Figure 40 Single Boiler Hydronic Heating Zoned Piping...
Page 41: ...37 Figure 41 Multiple Boiler Hydronic Heating Zoned Piping...
Page 42: ...38 Figure 42 Single Boiler with DHW Tank Hydronic Heating Zoned Piping...
Page 43: ...39 PART 10 PARTS LIST...
Page 44: ...40...
Page 45: ...41...
Page 46: ...42...
Page 47: ...43...
Page 48: ...44...
Page 49: ...45...
Page 50: ...46...
Page 51: ...47...
Page 52: ...48...
Page 53: ...49...
Page 54: ...50...
Page 60: ...56 PART 11 TUBING DIAGRAM...
Page 61: ...57 PART 12 WIRING DIAGRAM...
Page 62: ...58...
Page 63: ...59...