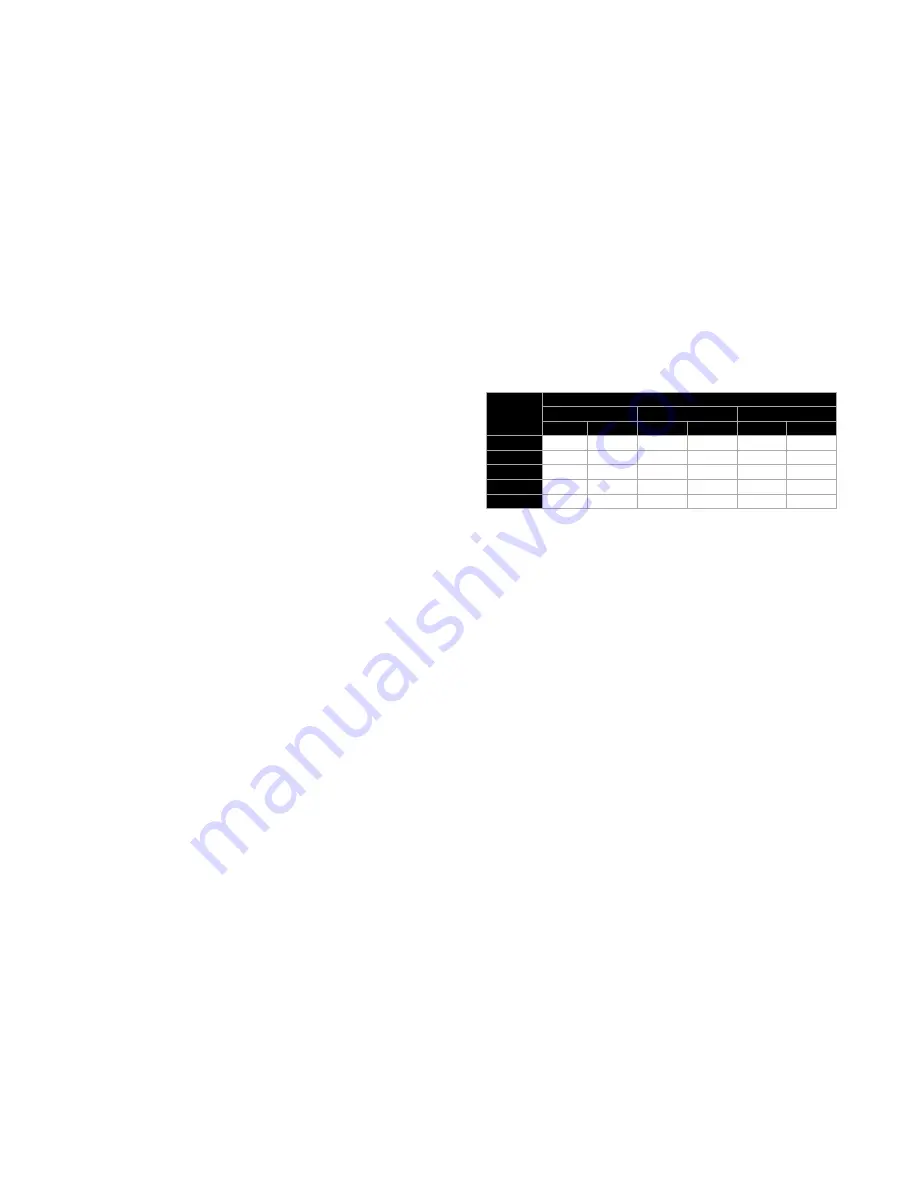
9
2.2.5
Removal of existing appliance (if applicable)
When an existing appliance is removed from a common
venting system, the common venting system is likely to be
too large for proper venting of the appliances remaining
connected to it. At the time of removal of an existing
appliance, the following steps must be followed with each
appliance remaining connected to the common venting
system placed in operation, while the other appliances
remaining connected to the common venting system are not
in operation.
1. Seal any unused openings in the common venting
system.
2. Visually inspect the venting system for proper size and
horizontal pitch and determine that there is no blockage,
restriction, leakage, corrosion, or other deficiency,
which could cause an unsafe condition.
3. Insofar as is practical, close all building doors and
windows and all doors between the space in which the
appliances remaining connected to the common venting
system are located and other spaces of the building. If
applicable turn on the clothes dryers and any appliances
not connected to the common venting system. Turn on
any exhaust fans, such as range hoods and bathroom
exhausts, so they will operate at maximum speed. Do
not operate a summer exhaust fan. Close fireplace
dampers.
4. Place in operation the appliance being inspected.
Follow the lighting instructions. Adjust thermostat so
that appliance operates continuously.
5. If provided, test for spillage at the draft control device
relief opening after 5 minutes of main burner operation.
Use a cold mirror, or the flame of a match or candle.
6. After it has been determined that each appliance
remaining connected to the common venting system
properly vents when tested as outlined above, return
doors, windows, exhaust fans, fireplace dampers and
any other gas-burning appliance to their previous
condition of use.
Any improper operation of the common venting system
should be corrected so that the installation conforms to the
National Fuel Gas Code, ANSI Z223.1/NFPA 54 and/or the
Natural Gas and Propane Installation Code, CSA B149.1-
15 and CSA B149.2-15 Installation Codes. When resizing
any portion of the common venting system, the common
venting system should be resized to approach the minimum
size as determined using the appropriate tables in Chapter
13 of the National Fuel Gas Code, ANSI Z223.1/NFPA 54
and /or the Natural Gas and Propane Installation Code,
CSA B149.1-15 and CSA B149.2-15 Installation Codes.
2.3
GAS CONNECTION
Verify that the appliance is supplied with the type of gas
specified on the rating plate. Consult factory for
installations at high altitude.
2.3.1 Gas Piping
Safe operation of the Valiant FT requires that the gas line
size chosen be sufficient to handle the total installed
capacity, within an acceptable range of pressure drop
across the piping, and at the available pressure. Gas pipe
size may be larger, but not smaller, than the appliance
connection.
The gas pipe line can be sized using the Spitzglass formula;
q = 3550 X k X (h/l X SG)
1/2
Where;
q = gas volume flow (cfh)
k = [d
5
/ (1 + 3.6 / d + 0.03 d)]
1/2
d = inside pipe diameter (in)
SG = specific gravity
1 CFH = 1 MBH
Table 5 below can be used for gas line sizing data (based
on 0.30” W.C. pressure drop and 0.60 Specific Gravity).
Please verify pipe size requirements with gas supplier.
Table 5: Recommended Gas Pipe Size for Single
Appliance
Input
KBtu/hr
Equivalent Length from NG Meter or LP Regulator
100 FT
101-200 FT
201-300 FT
NAT.
L.P.
NAT.
L.P.
NAT.
L.P.
400
1 ¼”
1”
1 ½”
1 ¼”
2”
1 ½”
500
1 ½”
1 ¼”
2”
1 ½”
2”
1 ½”
600
1 ½”
1 ¼”
2”
1 ½”
2”
1 ½”
725
2”
1
½”
3”
2 ½”
3”
2 ½”
850
2”
1 ½”
3”
2 ½”
3”
2 ½”
Installation of a union at the appliance gas line connection
is required for ease of service and removal of the gas train.
Install a manual main gas shutoff valve, outside of the
appliance as required by local codes.
Optional gas controls may require routing of bleeds and
vents to the atmosphere, outside the building when required
by local codes. Larger models of this appliance may be
supplied with a gas pressure relief valve. This valve is
designed to relieve lockup pressure in excess of the high
gas pressure switch setting. It must be piped to discharge
excess gas pressure through the valve to a safe location in
accordance with local codes.
All gas connections must be made with pipe joint compound
resistant to the action of liquefied petroleum and natural
gas. All piping must comply with local codes and
ordinances.
Use new, properly threaded black iron pipe free
from burrs. Avoid flexible gas connections. Internal
diameter of flexible gas lines may not provide appliance
with proper volume of gas. A trap (drip leg) must be
provided in the inlet gas connection to the appliance.
2.3.2 Gas Supply Pressure
Gas supply pressure must be maintained within the
specified range in Table 6. Before operating the appliance,
the complete gas train and all connections must be purged
of air and tested using soap solution. The appliance and its
individual gas shut-off valve must be disconnected from the
supply piping when pressure testing the gas supply piping
at pressures above ½ PSI.
Summary of Contents for Valiant-FT II Series
Page 2: ...99 0419 Rev 00...
Page 40: ...36 PART 9 PIPING DIAGRAMS Figure 40 Single Boiler Hydronic Heating Zoned Piping...
Page 41: ...37 Figure 41 Multiple Boiler Hydronic Heating Zoned Piping...
Page 42: ...38 Figure 42 Single Boiler with DHW Tank Hydronic Heating Zoned Piping...
Page 43: ...39 PART 10 PARTS LIST...
Page 44: ...40...
Page 45: ...41...
Page 46: ...42...
Page 47: ...43...
Page 48: ...44...
Page 49: ...45...
Page 50: ...46...
Page 51: ...47...
Page 52: ...48...
Page 53: ...49...
Page 54: ...50...
Page 60: ...56 PART 11 TUBING DIAGRAM...
Page 61: ...57 PART 12 WIRING DIAGRAM...
Page 62: ...58...
Page 63: ...59...