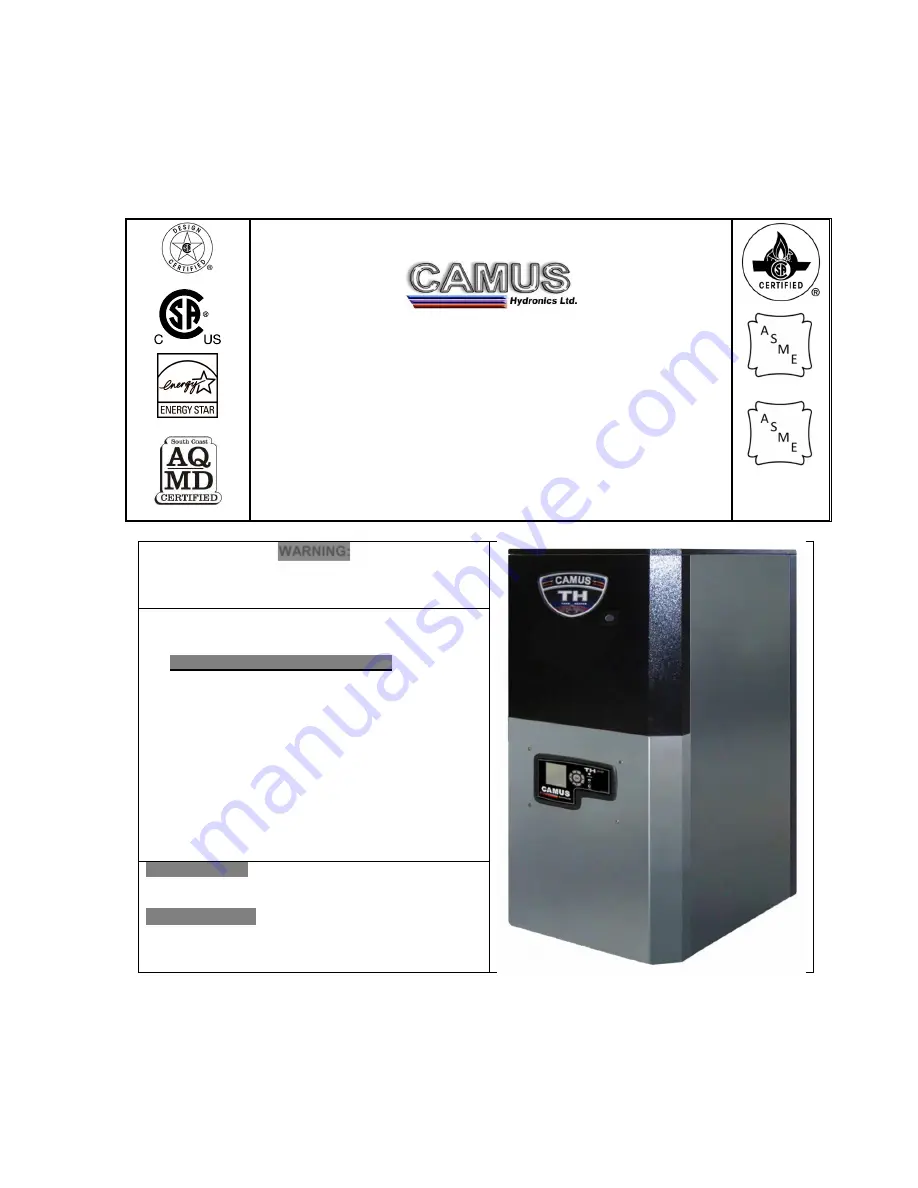
6226 Netherhart Road, Mississauga, Ontario, L5T 1B7
99-0079
Rev. 0.3
INSTALLATION OPERATION
AND SERVICE MANUAL
GAS FIRED RESIDENTIAL AND COMMERCIAL STAINLESS
STEEL TANK HEATERS
TH SERIES
HOT WATER SUPPLY
Models
;
TH082 ,102, 152, 202, 252,
292, 392, 502
H
HLW
WARNING:
If the information in these instructions is not followed
exactly, a fire or explosion may result causing property
damage, personal injury or death
Do not store or use gasoline or other flammable
vapours and liquids in the vicinity of this or any
other appliance.
WHAT TO DO IF YOU SMELL GAS
o
Do not try to light any appliance,
o
Do not touch any electrical switch; do not
use any phone in your building,
o
Immediately call your gas supplier from a
neighbour’s phone. Follow the gas
supplier’s instructions,
o
If you cannot reach your gas supplier, call
the fire department.
Qualified installer, service agency or the
gas supplier must perform installation and
service.
To the Installer: After installation, these instructions
must be given to the end user or left on or near the
appliance.
To the End User: This booklet contains important
information about this appliance. Retain for future
reference.
CAMUS HYDRONICS LTD.