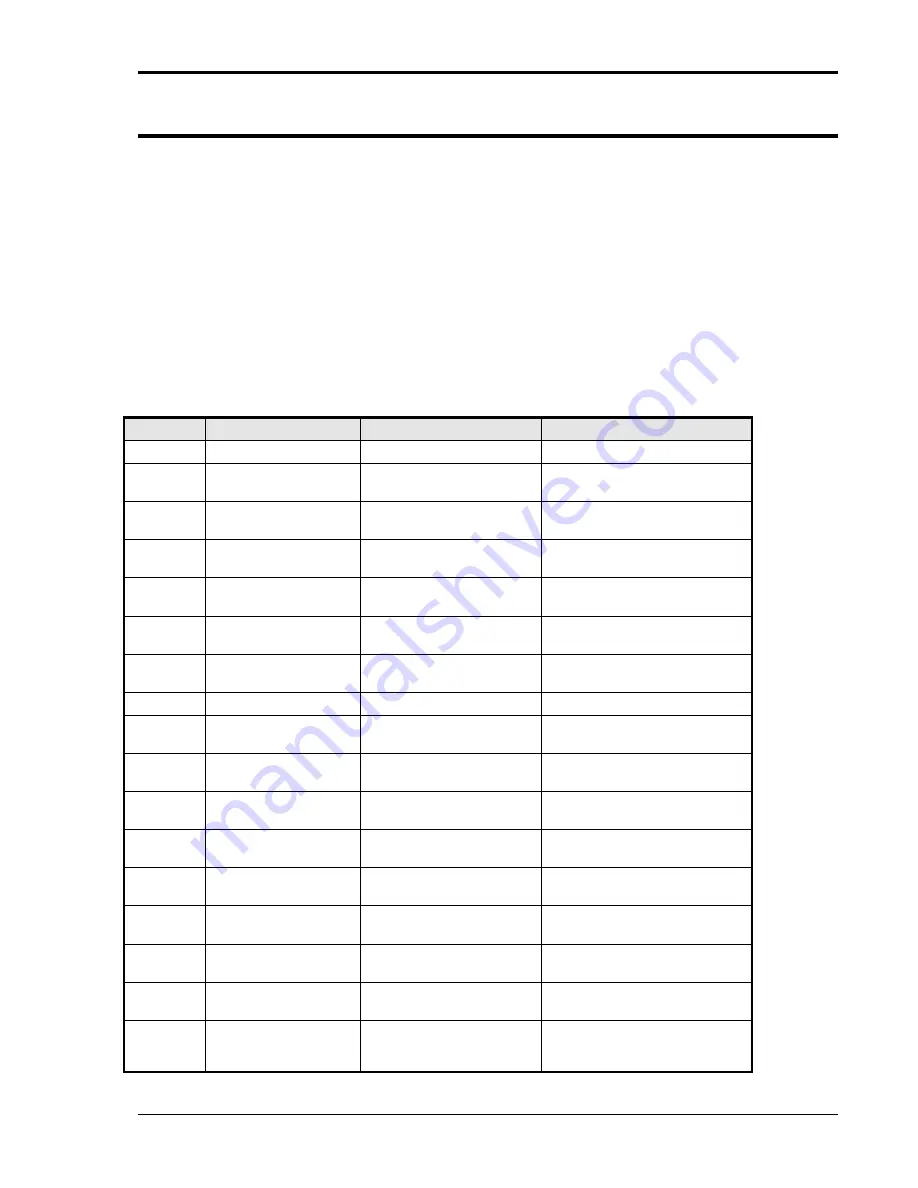
User Manual
AMETEK Programmable Power
BPS Series
146
12.
Error Messages
Any errors that occur during operation from either the front panel or the remote control interface will
result in error messages. Error messages are displayed in the upper left hand corner of the LCD display.
They are also stored in the error message queue from which they can be queried using the SYST:ERR?
Query. The error queue has a finite depth. If more error messages are generated than can be held in the
queue, a queue overflow message will be put in the last queue location. To empty the queue, use the error
query until the No Error result is received.
Errors appearing on the LCD will generally remain visible until the user moves to another screen. If
multiple error messages are generated in succession, only the last message will be visible as there is only
space for one error message on the LCD display.
The same area of the display is also used to display status messages. While error messages always have a
negative error number, status messages have a positive number.
The table below displays a list of possible error and status messages along with their possible cause and
remedy.
Number
Message String
Cause
Remedy
0
"No error"
No errors in queue
-100 "Command
error"
Unable to complete requested
operation
Unit may be in a mode inconsistent
with request.
-102
"Syntax error"
Command syntax incorrect.
Misspelled or unsupported
command
-103
"Invalid separator"
SCPI separator not recognized
See SCPI section of programming
manual.
-104
"Data type error"
Data type invalid.
Check command for supported data
types
-108
"Parameter not allowed"
One or more additional
parameters were received.
Check programming manual for
correct number of parameters
-109 "Missing
parameter"
Too few parameters received
for requested operation
Check programming manual for
correct number of parameters
-110
"Command header error"
Command header incorrect
Check syntax of command.
-111
"header separator error"
Invalid command separator
used.
Use semi-colon to separate
command headers
-112
"Program mnemonic too
long"
Syntax error
Check programming manual for
correct command syntax
-113 "Undefined
header"
Command not recognized
error
Check programming manual for
correct command syntax
-120
"Numeric data error"
Data received is not a number
Check programming manual for
correct command syntax
-121
"Invalid character in
number"
Number received contains
non-numeric character(s)
Check programming manual for
correct command syntax
-123
"Exponent too large"
Exponent in number exceeds
limits
Check programming manual for
correct parameter range
-128
"Numeric data not
allowed"
Number received when
number is not allowed.
Check programming manual for
correct command syntax
-168
"Block data not allowed"
Block data was sent.
Check programming manual for
correct command syntax
-200 "Execution
error"
Command could not be
executed
Command may be inconsistent
with mode of operation such as
programming frequency when in