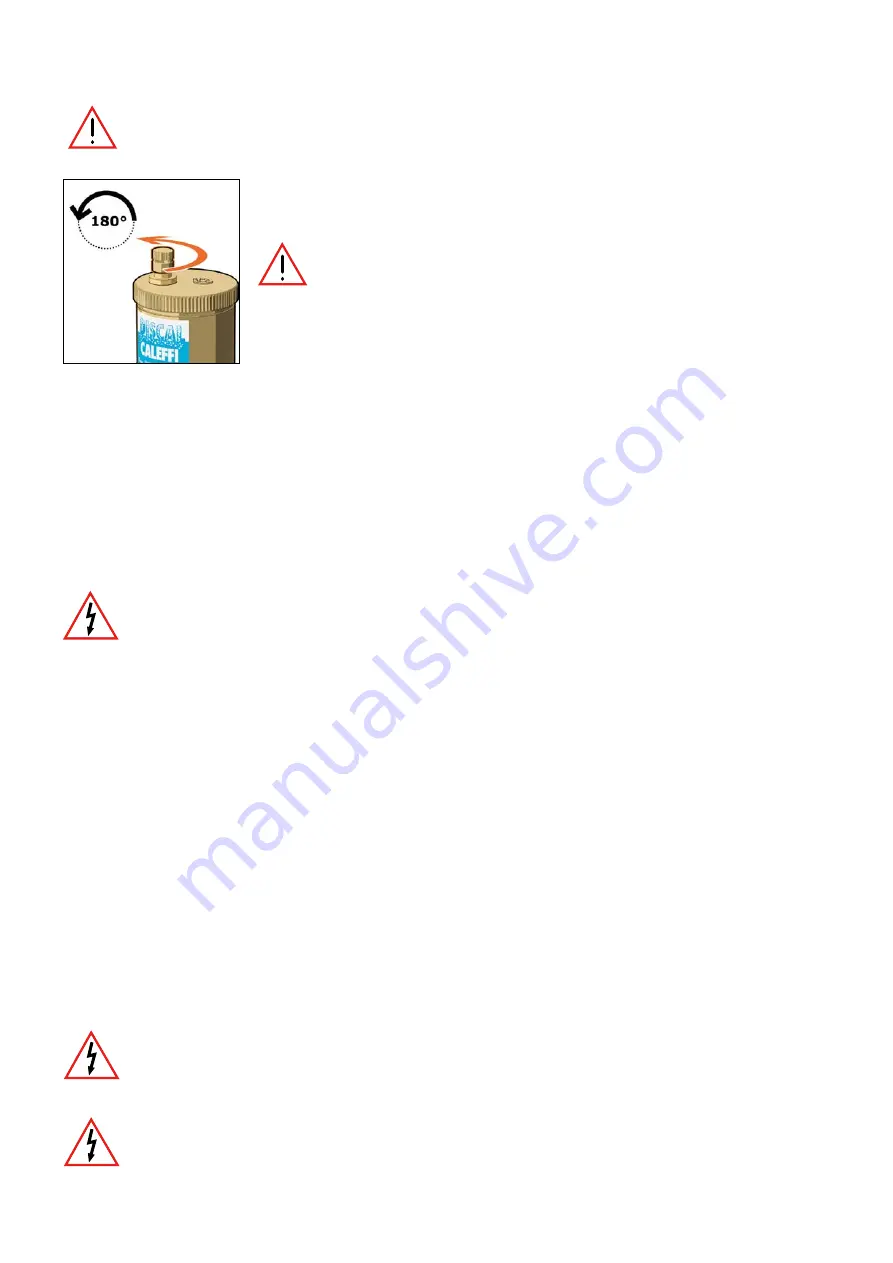
19
20
11 Commissioning
Commissioning must be carried out according to the regulations in force by qualified personnel.
Check that the cold water supply pressures are within the operating limits of the device.
Check that the temperature of the hot drain water has a value complying with the regulations in force.
NOTE. To ensure the strainer correct operation, check that the air vent cap is sufficiently loose (1/2 turn from
completely closed).
Attention
: the device performs a check during the filling phase from V2 at the end of the wash and
if the drain cocks is left closed, an alarm is generated. The device checks the correct opening of the
air vent to avoid injecting air into the system after each cleaning with filling from the domestic line.
For all information regarding the strainer digital regulator management, refer to the programming manual H0005275
At the first start-up, a careful analysis must be carried out to check that there are no leaks and the assembly is correct: the filling must be carried out
gradually in order to allow the correct expulsion of air by the vent valve.
Once the seals have been checked, the device can be electrically supplied: once the system is electrically supplied, it performs a series of checking
operations before starting the filtering function. After providing electric supply or after a reset, the system closes the inlet and drain valve and opens
again the inlet valve after carrying out a filling operation: these steps allow to limit the amount of water in the system drained and return the system
to the correct operating conditions.
Check that the pressure in the domestic water mains is in the strainer operating range (minimum 3 bar) to guarantee an effective cleaning of the
filtering discs.
11.1 Filling and hydraulic test under pressure
Important! Do not supply electricity to the controller until it is indicated.
1. Check that the inlet valve is in the open position and if necessary move it manually until it reaches the complete valve opening.
2. Check that the drain valve is in the closed position and if necessary move it manually until it reaches the closed position.
3. Check that the controller is not electrically supplied.
4. Check that the air vent cap opens.
5. Slowly open the shut-off valve upstream of the device inlet and pressurize the system.
6. Wait for the device to fill.
7. Check for leaks: if leaks or seepage are found, close the shut-off valve upstream of the device and correct the anomalies found. Now it is possible
to wait until the qualified personnel arrive to make the electrical connections for the device electric supply.
8. With pressurised device, power the controller: if it was previously electrically supplied or if an alarm was present, perform a "Device reset".
9. After a few seconds the yellow light will turn on to indicate that the device is carrying out some operations (filling and internal checks).
10. Wait for the yellow light to go off: in the meantime it is still possible to access the internal device configuration menus to set the date and time
and the type of cleaning to be performed.
11.2 First start-up
When the filtering system is started up for the first time, the "initial cleaning" function can be activated in the regulator menu. This function can be used
to wash the system using the medium contained in the system. This avoids to drain large quantities of medium and avoids the need for complicated
venting operations. When the set differential is reached, a washing cycle is immediately started. The system stops the initial cleaning function when the
set time is reached or when the
D
P is lower than the set one.
Depending on the type of installation it may be necessary to close the by-pass valve.
Check that the flow rates are compatible with the characteristics of the strainer and with other elements of the system
System stop procedure
Before turning off the regulator it is necessary to stop the flow of liquid to be filtered closing the system input motorised valve (V1). Turn
off the electric supply to the regulator and manually close the inlet valve (V1).
System prolonged closing
If the system is closed, remove the electric supply to the regulator, manually close the inlet valve (V1).