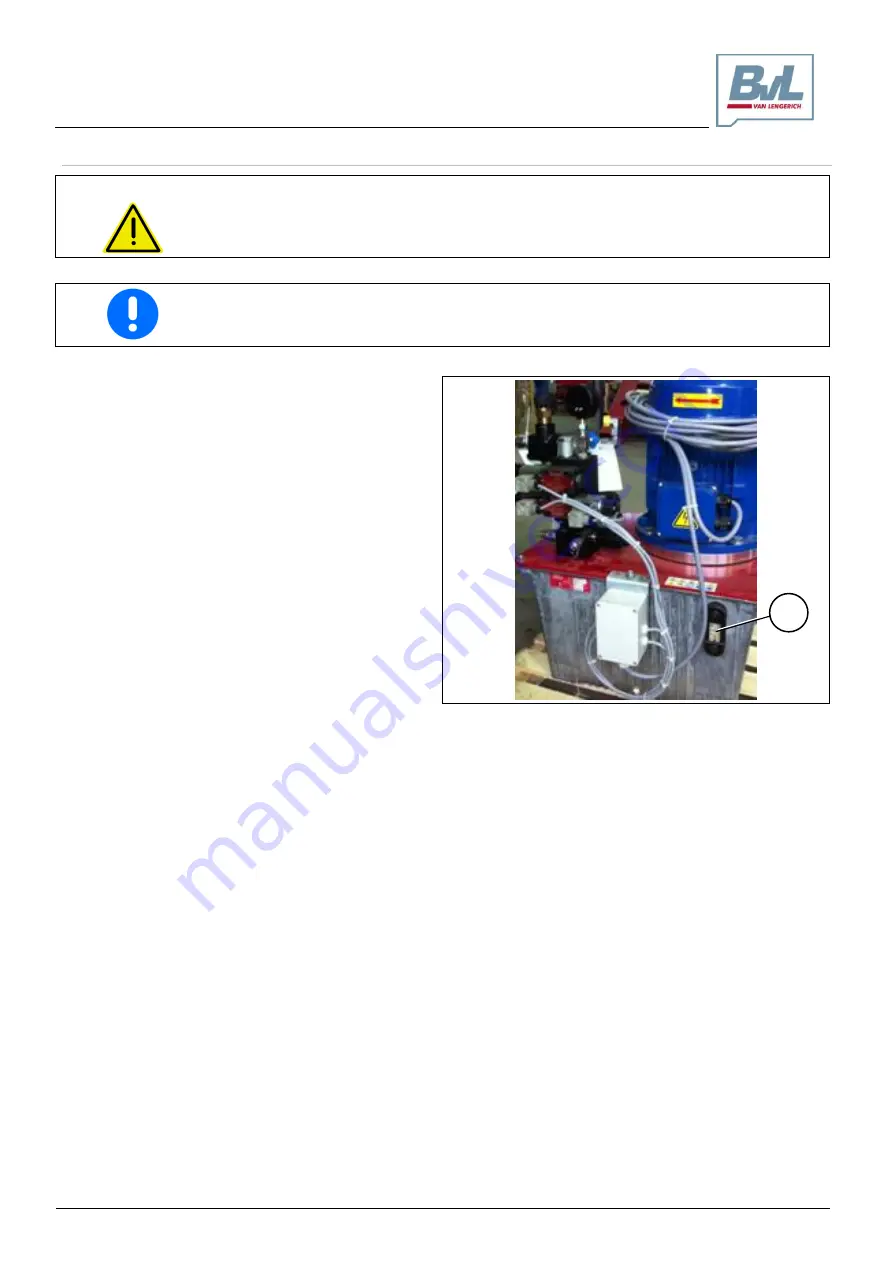
Cleaning
, maintenance and repairs
V-Mix Fix
Plus
Translation of the original assembly and operating manual
65
7.9.1
Checking the hydraulic oil level
WARNING
If oil is spilled during an oil change / oil refill, the resulting slip hazards can cause
personal injury!
Clean up spilled oil immediately with a binding agent.
Check the hydraulic oil level daily before starting your work day.
1.
Read the hydraulic oil level at the oil sight glass
(1).
2.
Top off hydraulic oil if the oil level is below the
min. mark. Observe chapter "Refilling hydraulic
oil", page 66 in this regard.
Fig. 7-10 Hydraulic unit (sample photo)
1