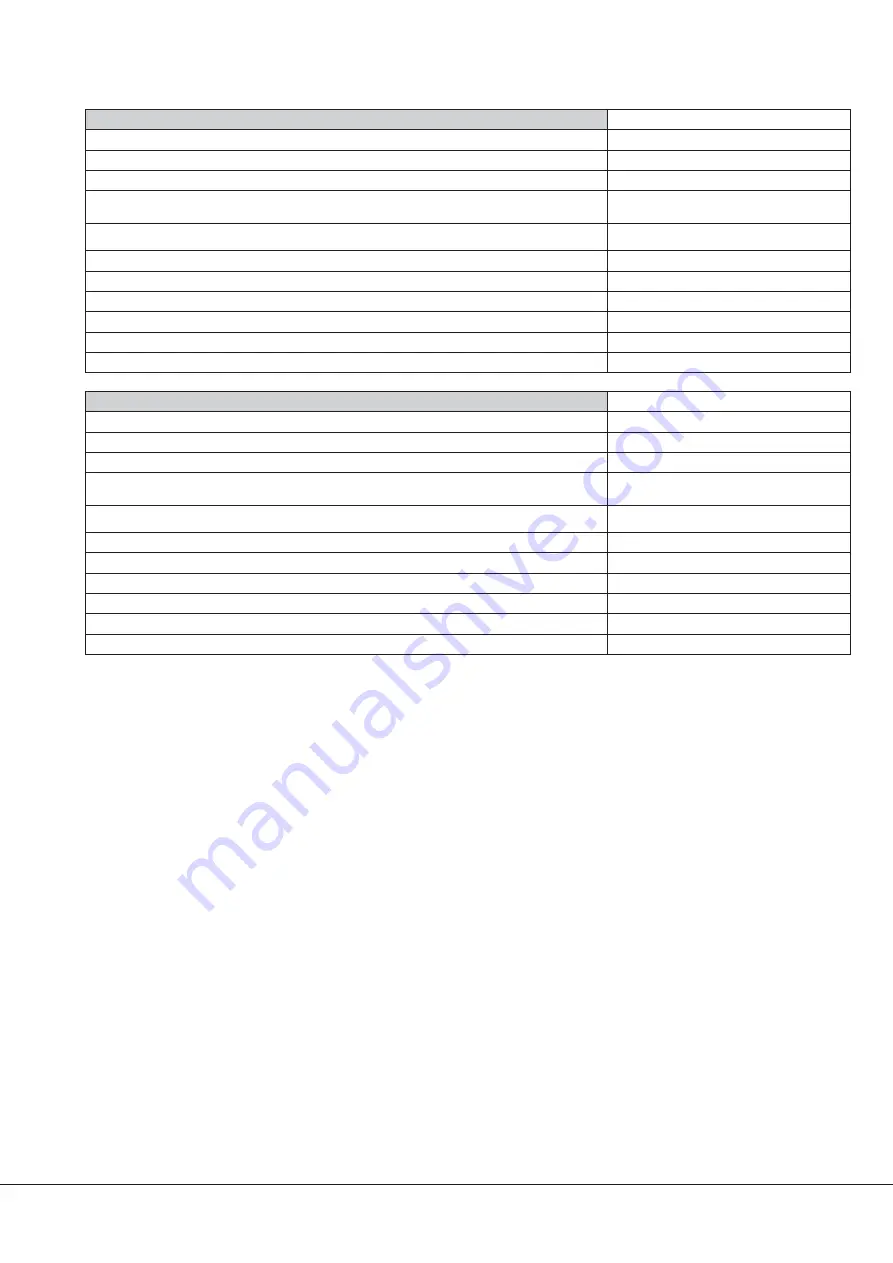
Technical data
Technical data
BC 0101 G
Nominal suction capacity
m
3
/h (cfm)
100 (59)
Ultimate pressure
hPa(mbar)/ mTorr
0,01/ 7,5
Nominal motor rating
kW
1,5
Power consumption at ultimate
pressure
kW
1,1
Nominal motor speed
min
-1
3600
Noise level (EN ISO 2151)
dB(A)
<58
Ambient temperature
°C (°F)
0-40 (32-104)
Cooling water requirement
l/ min
min 1.0
Cooling water pressure
bar
2 - 5
Cooling water temperature
°C
10 - 25
Weight
approx.
kg
117
Technical data
BC 0101 G (
NW 0090 A)
Nominal suction capacity
m
3
/h (cfm)
90 (53
)
Ultimate pressure
hPa(mbar)/ mTorr
0,01/ 7,5
Nominal motor rating
kW (50 Hz)
1,5
Power consumption at ultimate
pressure
kW (50 Hz)
0,
7
Nominal motor speed
min
-1
3000
Noise level (EN ISO 2151)
dB(A)
<58
Ambient temperature
°C (°F)
0-40 (32-104)
Cooling water requirement
l/ min
min 1.0
Cooling water pressure
bar
2 - 5
Cooling water temperature
°C
10 - 25
Weight
approx.
kg
117
Technical data
BC 0101 G
Page 19
0870704904 (En)
Summary of Contents for COBRA BC 0101 G
Page 22: ...Note...
Page 23: ...Note...