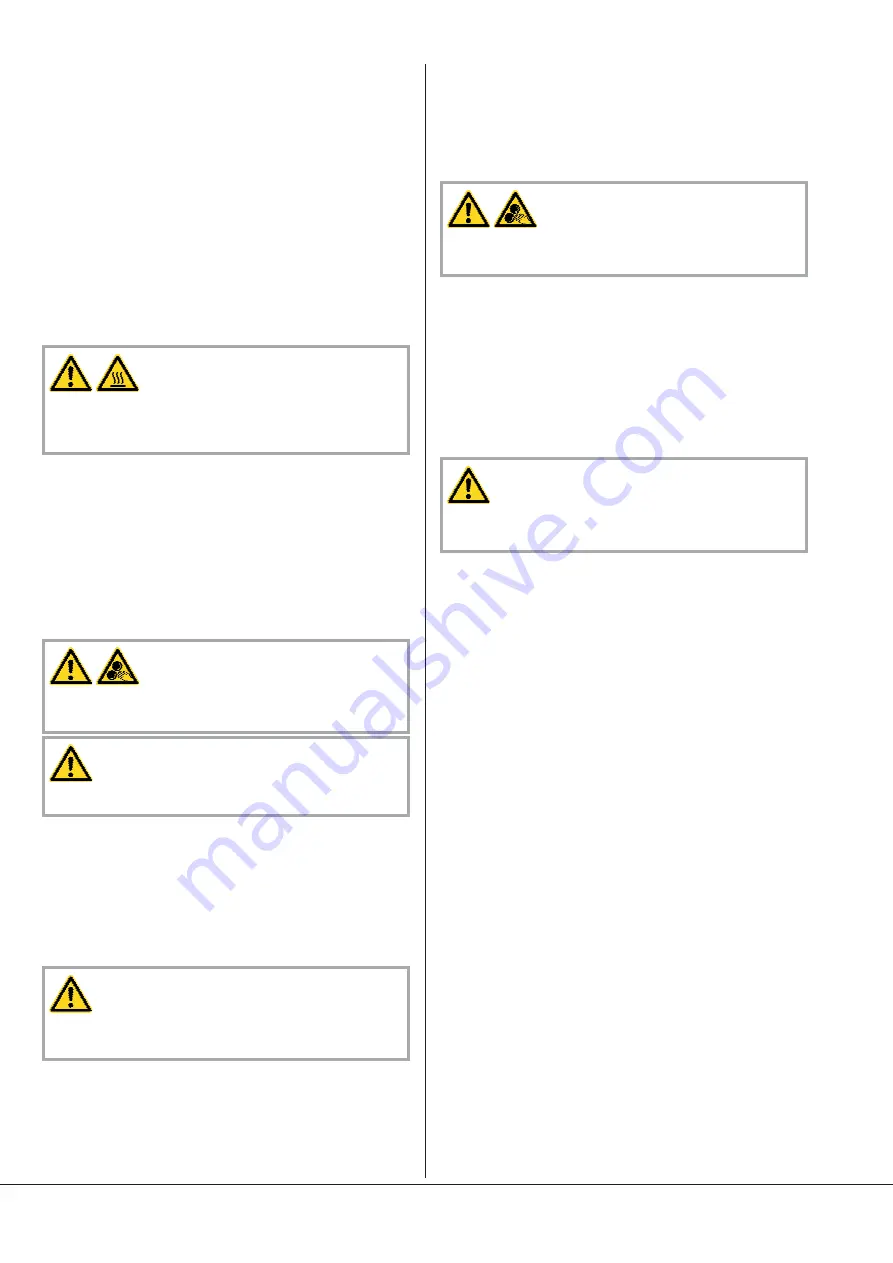
NOTE
: The levelling of the pump is facilitated by the adjustment stroke
(~30 mm) of the four machine foots.
l
Make sure that the four rollers do not touch the ground
NOTE
: In order to ensure the fixation of the pump to the ground, it is
possible to use again the four yellow brackets that were removed at
the reception of the machine.
l
Make sure that the vacuum pump is at least 1 m away from any
wall to ensure good cooling
l
Make sure that the vacuum pump is easily accessible and that the
selected installation site fulfills the requirements for
assembly/dismantling
l
Make sure that no temperature-sensitive parts (for example, of
plastic, wood, cardboard, paper, electronic parts) come into
contact with the hot surfaces of the vacuum pump
l
Make sure that the installation site or assembly area is ventilated in
such a way that adequate cooling of the vacuum pump is ensured
CAUTION
The surface temperature of the vacuum pump can exceed 50°C
when the vacuum pump is in operation.
Danger of burns!
l
Make sure that no-one can touch the vacuum pump accidentally.
If necessary, attach safeguard
l
Make sure that the oil sight glasses (OSG) are easily accessible
If oil changes are to be made on site:
u
Make sure that the oil drain and oil filler are easily accessible
Inlet connection
l
Make sure that the protection that was attached to prevent
penetration of particles during transport has been removed before
the vacuum pump is connected to the vacuum line
CAUTION
Do not put hands into the inlet aperture.
Risk of body damage !
CAUTION
The intake of liquids or solid particles can lead to the destruction of
the vacuum pump
If the sucked gas contains dusts or solid foreign bodies:
u
Make sure that a filter or protective grating is installed at the
extraction point
l
Make sure that the nominal diameter of the intake line is at least
equal to the diameter of the intake flange of the vacuum pump to
prevent a drop in the performance of the vacuum pump in the case
of a smaller cross-section
l
Make sure that the vacuum pump is connected with leakproof lines
CAUTION
When the intake lines have been connected, make sure that the
system does not leak. Leakages of dangerous substances must be
prevented!
l
Make sure that the intake lines are equipped with a shut-off device
upstream of the intake flange so that the flow of sucked gas can
be stopped
l
Make sure that the intake lines do not exercise any force on the
intake flange. Mount bellows if necessary
l
The inlet flange has the following dimension:
–
DN 50 ISO KF
In the case of long intake lines, the line cross-section should be larger
than the intake flange to prevent a drop in the performance of the
vacuum pump. If you have any doubts, contact your Busch
representative.
Discharge connection
CAUTION
Do not put hands into the outlet aperture.
Risk of body damage !
The following instructions for connection to the discharge only apply if
the sucked gas is discharged by the vacuum pump into a suitable
environment.
l
Make sure that the protection that was attached to prevent
penetration of particles during transport has been removed before
the vacuum pump is connected to the vacuum line
l
Make sure that the nominal diameter of the exhaust line is at least
equal to the diameter of the exhaust flange of the vacuum pump
to prevent a drop in the performance of the vacuum pump in the
case of a smaller cross-section
l
Make sure that the vacuum pump is connected with leakproof lines
CAUTION
When the discharge lines have been connected, make sure that the
system does not leak. Leakages of dangerous substances must be
prevented!
l
Make sure that the discharge line is mounted in such a way that
condensate cannot penetrate into the pump (siphon trap, gradient)
l
Make sure that no shut-off devices are mounted in the discharge
line
l
Make sure that the discharge lines do not exercise any force on the
discharge flange. Mount bellows if necessary
l
The discharge flange has the following dimension:
–
DN 40 ISO KF
In the case of long discharge lines the line cross-section should be
larger than the discharge flange to prevent a drop in the performance
of the vacuum pump. If you have any doubts, contact your Busch
representative.
Cooling water connection
The cooling water is generally connected with a hose.
The cooling water outlet must be unpressurised.
Connection diameter: 1/4 PT
Nitrogen connection
The nitrogen is connected with a pipe (leakproof against oxygen).
Connection diameter: 1/4 PT
Electrical connection/ Checks
l
Make sure that the regulations of the Electromagnetic
Compatibility Directive 2014/30/EU as well as standard EN norms,
safety directives and especially local and national regulations are
observed (this is the responsibility of the manufacturer of the
system into which the vacuum pump is integrated according to the
Declaration of Conformity)
l
Make sure that the mains power supply corresponds to the data on
the nameplate of the vacuum pump
l
Make sure that an overload cut-out according to EN 60204-1 is
provided for the vacuum pump
Installation and start-up
BC 0101 G
Page 10
0870704904 (En)
l
Make sure that the drive of the vacuum pump is not disturbed by
any electric or electromagnetic interferences. If you have any
doubts, contact your Busch representative
Summary of Contents for COBRA BC 0101 G
Page 22: ...Note...
Page 23: ...Note...