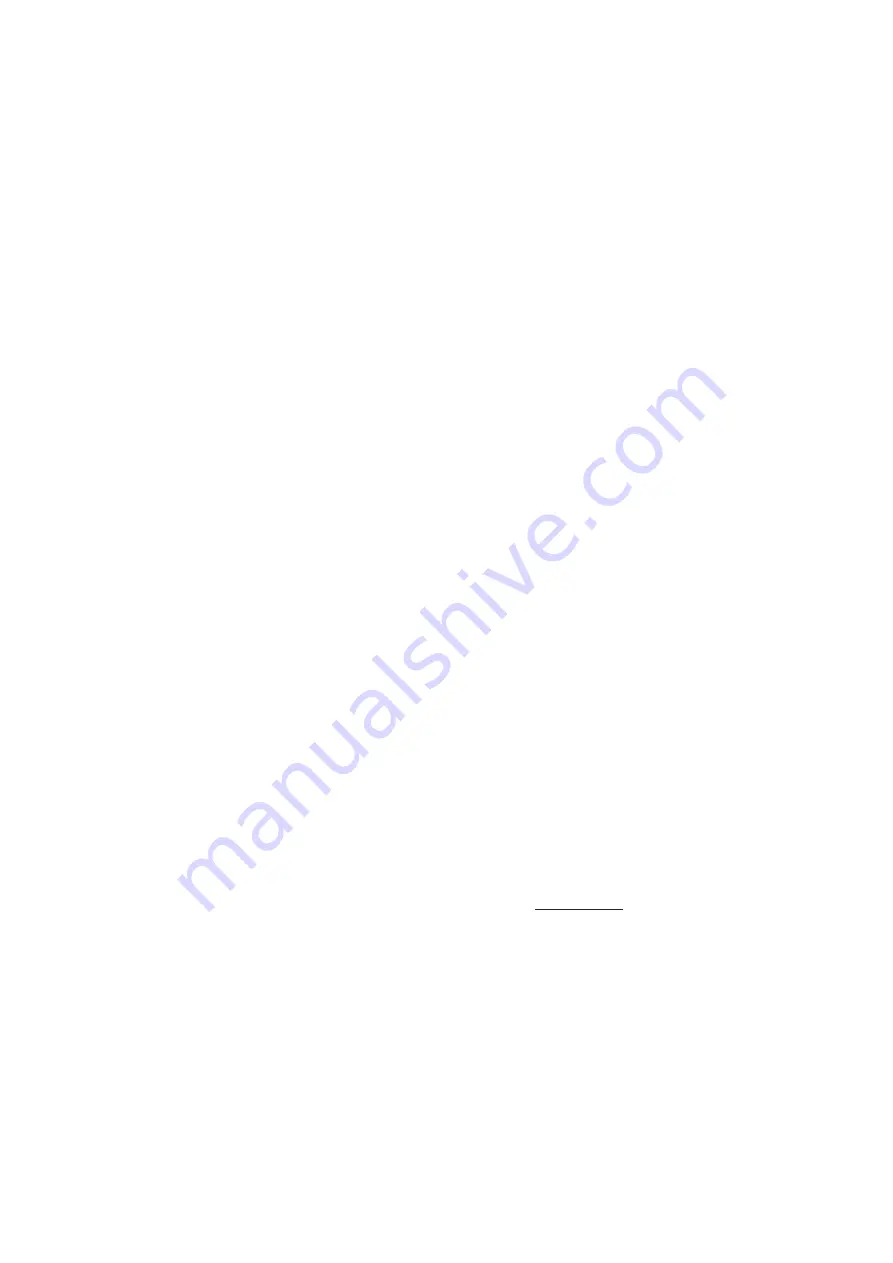
burster
Digital Panelmeter
Model 9180
Page
Note:
The following information may be amended without prior notice. No part of this document may be reproduced or
processed using electronic system without prior consent in writing.
burster provides no warranty of any kind respect to this material, including the implied warranty of merchantable
quality and fitness for purpose.
burster is not liable under any circumstances for errors, incidental damage or consequential loss sustained in
connection with the function or use of this material.
© 2000
burster
präzisionsmeßtechnik gmbh & co kg
All rights reserved
Edition 3/2000
Manufacturer
burster präzisionsmeßtechnik gmbh & co kg
Talstr. 1 - 5
P.O.Box 1432
76593 Gernsbach 76587 Gernsbach
Digital Panelmeter
Model 9180
Summary of Contents for 9180
Page 2: ...Model 9180 burster Digital Panelmeter Page ...
Page 3: ...burster Digital Panelmeter Model 9180 Page ...
Page 4: ...Model 9180 burster Digital Panelmeter Page ...
Page 8: ...Model 9180 burster Digital Panelmeter Page ...
Page 12: ...Model 9180 burster Digital Panelmeter Page ...
Page 104: ...Model 9180 burster Digital Panelmeter Page ...
Page 105: ...burster Digital Panelmeter Model 9180 Page 6 1 A P P E N D I X Example BASIC ...
Page 106: ...Model 9180 burster Digital Panelmeter Page 1 ...
Page 107: ...burster Digital Panelmeter Model 9180 Page 2 ...
Page 108: ...Model 9180 burster Digital Panelmeter Page 3 ...
Page 109: ...burster Digital Panelmeter Model 9180 Page 4 ...