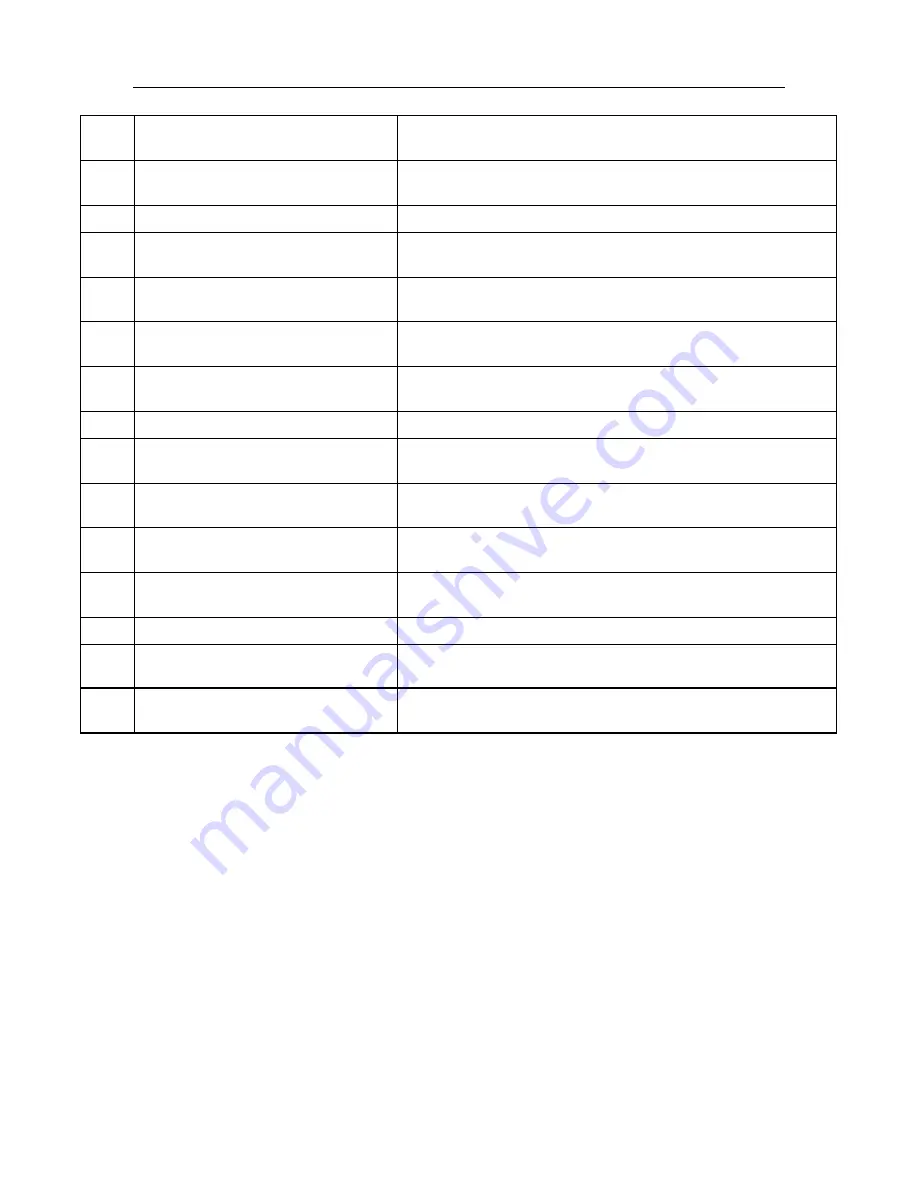
PART 1 – SYSTEM OVERVIEW
27
Lifter 4 Hot un-switched output
Un-switched 24 V max AC Line, 50/60 Hz, max 2 A
See note above.
32
Lifter 4 Neutral un-switched output
Un-switched 24 V max AC Neutral, 50/60 Hz, max 2 A
See note above.
37
Chassis Ground
18 AWG wire
36
Lifter 5 up switched output
Switched 24 V max AC, 50/60 Hz, 2 A max.
See note above.
35
Lifter 5 down switched output
Switched 24 V max AC, 50/60 Hz, 2 A max.
See note above.
31
Lifter 5 Hot un-switched output
Un-switched 24 V max AC Line, 50/60 Hz, max 2 A
See note above.
30
Lifter 5 Neutral un-switched output
Un-switched 24 V max AC Neutral, 50/60 Hz, max 2 A
See note above.
34
Chassis Ground
18 AWG wire
29
Lifter 6 up switched output
Switched 24 V max AC, 50/60 Hz, 2 A max.
See note above.
23
Lifter 6 down switched output
Switched 24 V max AC, 50/60 Hz, 2 A max.
See note above.
24
Lifter 6 Hot un-switched output
Un-switched 24 V max AC Line, 50/60 Hz, max 2 A
See note above.
17
Lifter 6 Neutral un-switched output
Un-switched 24 V max AC Neutral, 50/60 Hz, max 2 A
See note above.
16
Chassis Ground
18 AWG wire
19
Input for External AC Lifter supply –
Hot
24 V max AC, 50/60 Hz, or 24 V max DC
6.3 A max. See note above.
20
Input for External AC Lifter supply –
Neutral
24 V max AC, 50/60 Hz, or 24 V max DC
6.3 A max. See note above.
Summary of Contents for 1100 CD
Page 20: ...Figure 1 3 Slowdown Marker ...
Page 34: ...BLANK ...
Page 56: ...BLANK ...
Page 58: ...Tools 40 Torch Lifter Controls 26 Tracer Function Keys 21 28 ...
Page 63: ...PART 7 DRAWINGS PART 7 DRAWINGS ...
Page 64: ...BLANK ...