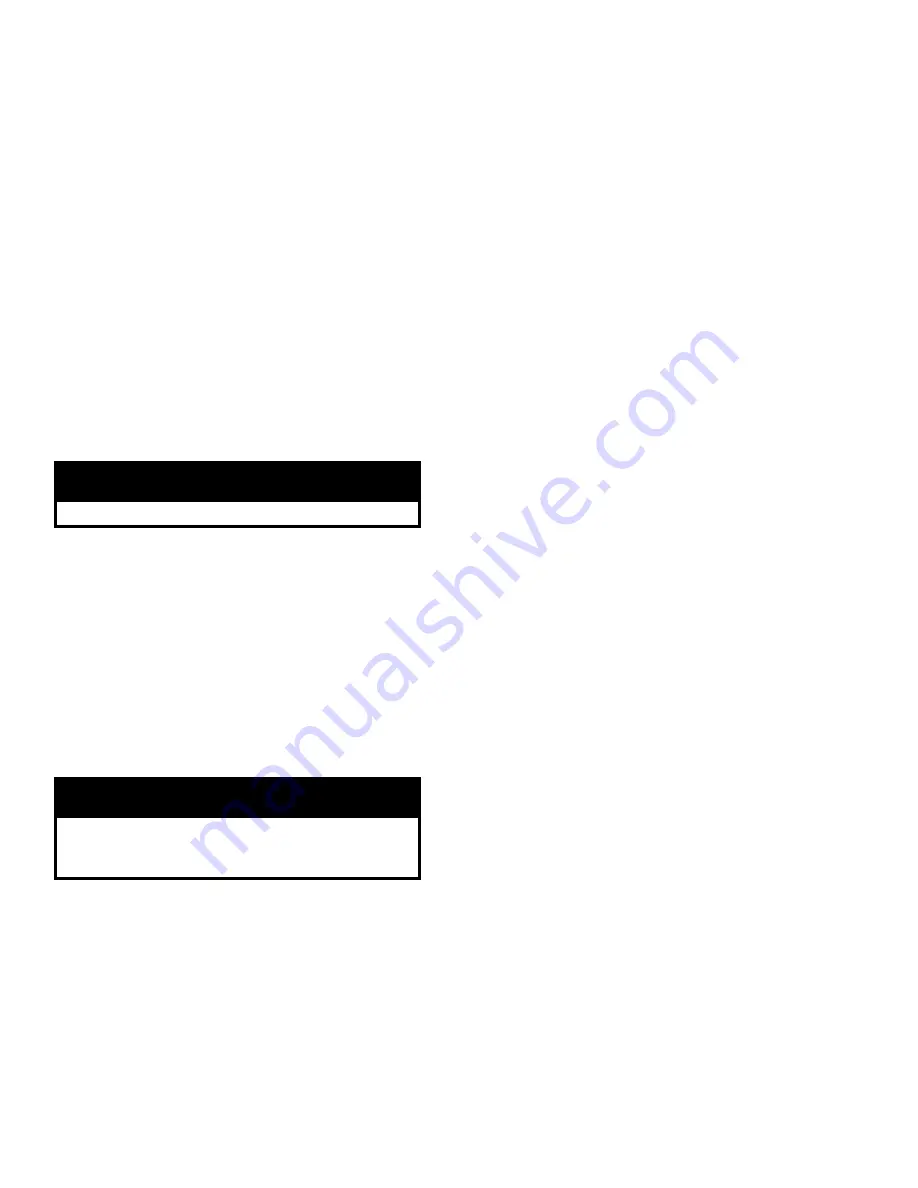
58
2. Adjust thermostat to highest setting.
3. Check main burner flames. See Figure 56 or 57.
Flame should have clearly defined inner cones with
no yellow tipping. Orange-yellow streaks caused by
dust should not be confused with true yellow
tipping.
4. Adjust thermostat to normal setting.
G.
Check thermostat operation.
Raise and lower
temperature setting to start and stop boiler operation.
H.
Check ignition system shutoff.
Gas valve should close
and pilot and main burners extinguish.
1. Continuous Ignition (Standing Pilot): disconnect
thermocouple from gas valve.
2. Electronic Ignition (EI): disconnect igniter/sensor
cable from ignition module terminal "9".
I.
Check low water cutoff (steam only).
1. Adjust thermostat to highest setting.
2. With boiler operating, open drain and slowly drain
boiler.
CAUTION
Do not drain below gauge glass.
3. Main burners will extinguish when water level drops
below low water cutoff. Water should still be visible
in gauge glass. Verify limit, thermostat or other
controls have not shut off boiler.
4. Adjust thermostat to lowest setting. Refill boiler to
normal water line.
J.
Check Limit.
1. Adjust thermostat to highest setting.
2. Steam: Observe pressure gauge. When pressure is
indicated, adjust limit to setting below observed
pressure. Main burners should extinguish.
WARNING
Failure to properly adjust gas input rate will result
in over firing or under firing of the appliance.
Improper and unsafe boiler operation may result.
3. Water: Observe temperature gauge. When
temperature exceeds limit set point main burners
should extinguish.
4. Adjust limit to setting above observed reading. Main
burners should reignite.
5. Adjust thermostat to lowest setting. Adjust limit to
desired setting.
K.
Adjust gas input rate to boiler.
Natural Gas.
1. Adjust thermostat to highest setting.
2. Check manifold gas pressure. Manifold pressure is
listed on Rating Label.
a. Models IN3-IN12 with Standing Pilot, IN3-IN9
with Hot Surface to Pilot and IN3-IN11 with
Electronic Ignition. Adjust gas valve pressure
regulator as necessary (turn adjustment screw
counterclockwise to decrease manifold pressure,
or clockwise to increase manifold pressure). If
pressure can not be attained, check gas valve
inlet pressure. If less than minimum gas supply
pressure listed on Rating Label, contact gas
supplier for assistance.
b. Model IN12 with Electronic Only.
i
. Turn off gas valve not having pilot control.
ii
. On gas valve with pilot control, adjust gas
valve pressure regulator to obtain required
manifold pressure, or if unattainable, highest
pressure without forcing adjustment screw
(turn adjustment screw counterclockwise to
decrease manifold pressure, or clockwise to
increase manifold pressure).
iii
. Turn on gas valve not having pilot control.
Adjust gas valve pressure regulator to obtain
required manifold pressure. Manifold
pressure may not change during initial turns
of adjustment screw.
3. Clock gas meter for at least 30 seconds. Use Table
10 to determine gas flow rate in Cubic Feet per
Hour.
4. Determine Input Rate. Multiply gas flow rate by gas
heating value.
5. Compare measured input rate to input rate stated on
Rating Label.
a. Boiler must not be overfired. Reduce input rate
by decreasing manifold pressure. Do not reduce
more than 0.3 inch w.c. If boiler is still overfired,
contact your Governale distributor or Regional
Office for replacement Gas Orifice.
b. Increase input rate if less than 98% of Rating
Label input. Increase manifold gas pressure no
more than 0.3 inch w.c. If measured input rate is
still less than 98% of rated input:
i
. Remove Main Burners per procedure in
Section X: Service Instructions.
ii
. Remove gas orifices. Drill one (1) drill size
larger (drill size is stamped on orifice).
iii
. Reinstall gas orifices and main burners.
Measure input rate.
6. Recheck Main Burner Flame.
7. Return other gas-fired appliances to previous
conditions of use.
Summary of Contents for INDEPENDENCE IN10 CANADA
Page 4: ... Figure 1 Dimensional Drawing ...
Page 18: ...18 Figure 25 Recommended Water Piping for Circulator Zoned Heating System ...
Page 19: ...19 Figure 25A Recommended Water Piping for Zone Valve Zoned Heating System ...
Page 28: ...28 Figure 34 Vent Damper Schematic Wiring Diagram Figure 33 Vent Damper Harness to Limit ...
Page 29: ...29 THIS PAGE LEFT INTENTIONALLY BLANK ...
Page 30: ...30 Figure 35 Wiring Diagrams Steam Continuous Ignition Standing Pilot Probe Low Water Cutoff ...
Page 32: ...32 Figure 36 Wiring Diagrams Steam Intermittent Ignition EI Probe Low Water Cutoff ...
Page 34: ...34 Figure 37 Wiring Diagrams Steam Continuous Ignition Standing Pilot Float Low Water Cutoff ...
Page 36: ...36 Figure 38 Wiring Diagrams Steam Intermittent Ignition EI Float Low Water Cutoff ...
Page 40: ...40 Figure 40 Wiring Diagrams Water Intermittent Ignition EI Intermittent Circulation ...
Page 42: ...42 Figure 41 Wiring Diagrams Water Continuous Ignition Standing Pilot Gravity Circulation ...
Page 44: ...44 Figure 42 Wiring Diagrams Water Intermittent Ignition EI Gravity Circulation ...
Page 46: ...46 Figure 43 Wiring Diagrams Water Continuous Ignition Standing Pilot Tankless Heater ...
Page 48: ...48 Figure 44 Wiring Diagrams Water Intermittent Ignition EI Tankless Heater ...
Page 51: ...51 Figure 48 Lighting Instructions Continuous Ignition System VR8200 and VR8300 Gas Valves ...
Page 52: ...52 Figure 49 Lighting Instructions Continuous Ignition System 7000 ERHC Gas Valve ...
Page 66: ...66 Honeywell Electronic Ignition Trouble Shooting Guide ...
Page 67: ...67 Honeywell Hot Surface to Pilot Trouble Shooting Guide ...
Page 80: ...80 ...
Page 84: ...84 ...
Page 87: ...87 THIS PAGE LEFT BLANK INTENTIONALLY ...
Page 88: ...88 ...