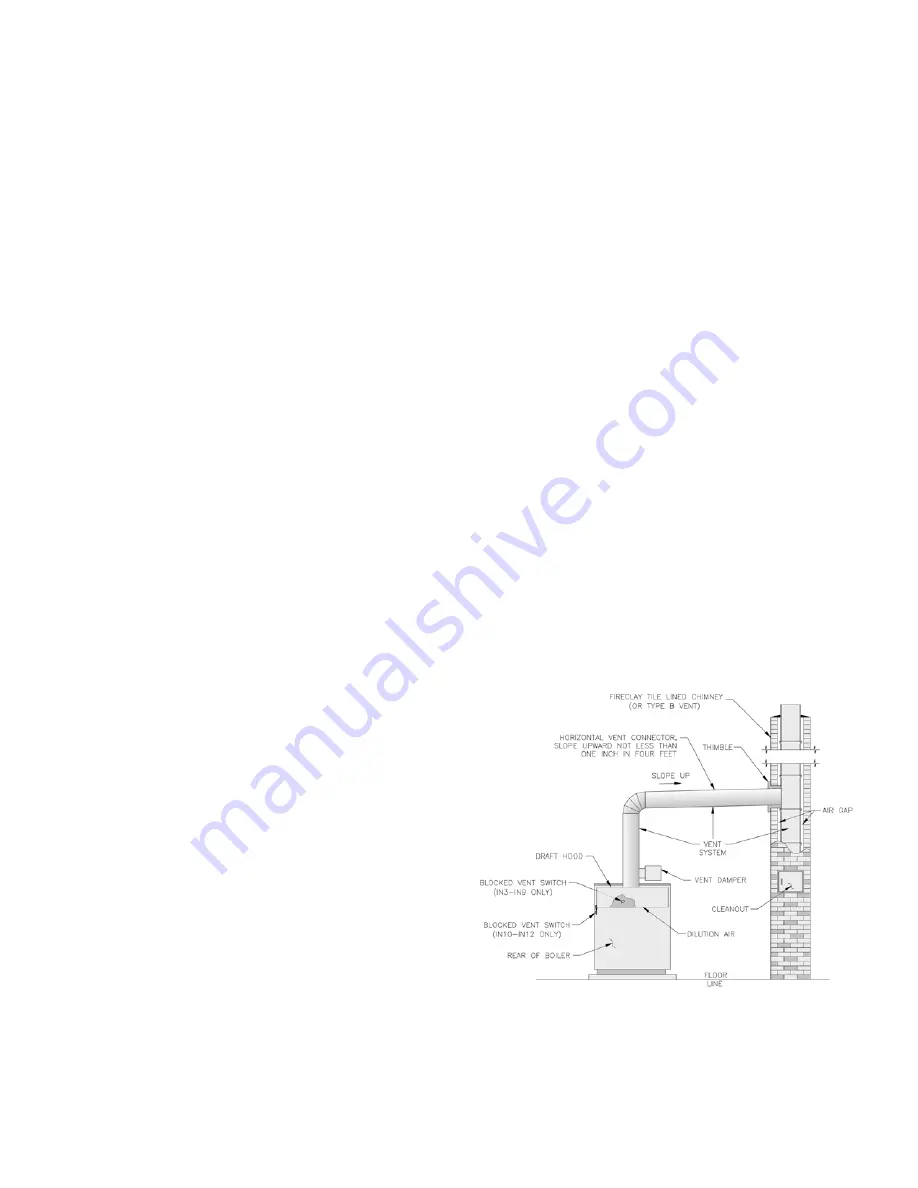
25
3. Insofar as is practical, close all building doors and
windows and all doors between the space in which
the appliances remaining connected to the common
venting system are located and other spaces of the
building. Turn on clothes dryers and any appliance
not connected to the common venting system. Turn
on any exhaust fans, such as range-hoods and
bathroom exhausts, so they will operate at maximum
speed. Do not operate a summer exhaust fan. Close
fireplace dampers.
4. Place in operation the appliance being inspected.
Follow the Lighting (or Operating) Instructions.
Adjust thermostat so appliance will operate
continuously.
5. Test for spillage at the draft hood relief opening
after 5 minutes of main burner operation. Use the
flame of a match or candle, or smoke from a
cigarette, cigar or pipe.
6. After it has been determined that each appliance
remaining connected to the common venting system
properly vents when tested as outlined above, return
doors, windows, exhaust fans, fireplace dampers and
any other gas-burning appliance to their previous
condition of use.
7. Any improper operation of the common venting
system should be corrected so the installation
conforms with the
National Fuel Gas Code
, NFPA
54/ANSI Z223.1. When resizing any portion of the
common venting system, the common venting
system should be resized to approach the minimum
size as determined using the appropriate tables in
Part 11 in the
National Fuel Gas Code
, NFPA 54/
ANSI Z223.1.
D.
Install Vent Connector
from draft hood or vent
damper to chimney. See Figure 30.
1. Do not connect into same leg of chimney serving an
open fireplace.
2. Vent pipe to chimney must not be smaller than outlet
on draft hood or vent damper. Type B is
recommended, but single-wall vent pipe may be
used. Arrange venting system so boiler is served by
vent damper device.
3. Where two or more appliances vent into a common
vent, the area of the common vent should be at least
equal to the area of the largest vent plus 50% of the
area in the additional vent(s). Do not connect the
vent of this appliance into any portion of mechanical
draft systems operating under positive pressure.
4. Horizontal run should be as short as possible. The
maximum length of an uninsulated horizontal run
must not exceed 75% of the height of the chimney.
5. Vent pipe should have the greatest possible initial
rise above draft hood consistent with headroom
available and required clearance from adjacent
combustible building structure. Vent pipe should be
installed above bottom of chimney to prevent
blockage.
6. Vent pipe should slope upward from draft hood to
chimney not less than one inch in four feet. No
portion of vent pipe should run downward or have
dips or sags. Vent pipe must be securely supported.
7. Vent pipe must be inserted into but not beyond
inside wall of chimney liner. Seal tight between vent
pipe and chimney.
E.
If an Existing Boiler is Removed:
When an existing boiler is removed from a common
venting system, the common venting system is likely to
be too large for proper venting of the appliances
remaining connected to it.
At the time of removal of an existing boiler, the
following steps shall be followed with each appliance
remaining connected to the common venting system
placed in operation, while the other appliances
remaining connected to the common venting system are
not in operation:
1. Seal any unused openings in the common venting
system.
2. Visually inspect the venting system for proper size
and horizontal pitch and determine there is no
blockage or restriction, leakage, corrosion, and other
deficiencies which could cause an unsafe condition.
Figure 30: Typical Vent Installation
Summary of Contents for INDEPENDENCE IN10 CANADA
Page 4: ... Figure 1 Dimensional Drawing ...
Page 18: ...18 Figure 25 Recommended Water Piping for Circulator Zoned Heating System ...
Page 19: ...19 Figure 25A Recommended Water Piping for Zone Valve Zoned Heating System ...
Page 28: ...28 Figure 34 Vent Damper Schematic Wiring Diagram Figure 33 Vent Damper Harness to Limit ...
Page 29: ...29 THIS PAGE LEFT INTENTIONALLY BLANK ...
Page 30: ...30 Figure 35 Wiring Diagrams Steam Continuous Ignition Standing Pilot Probe Low Water Cutoff ...
Page 32: ...32 Figure 36 Wiring Diagrams Steam Intermittent Ignition EI Probe Low Water Cutoff ...
Page 34: ...34 Figure 37 Wiring Diagrams Steam Continuous Ignition Standing Pilot Float Low Water Cutoff ...
Page 36: ...36 Figure 38 Wiring Diagrams Steam Intermittent Ignition EI Float Low Water Cutoff ...
Page 40: ...40 Figure 40 Wiring Diagrams Water Intermittent Ignition EI Intermittent Circulation ...
Page 42: ...42 Figure 41 Wiring Diagrams Water Continuous Ignition Standing Pilot Gravity Circulation ...
Page 44: ...44 Figure 42 Wiring Diagrams Water Intermittent Ignition EI Gravity Circulation ...
Page 46: ...46 Figure 43 Wiring Diagrams Water Continuous Ignition Standing Pilot Tankless Heater ...
Page 48: ...48 Figure 44 Wiring Diagrams Water Intermittent Ignition EI Tankless Heater ...
Page 51: ...51 Figure 48 Lighting Instructions Continuous Ignition System VR8200 and VR8300 Gas Valves ...
Page 52: ...52 Figure 49 Lighting Instructions Continuous Ignition System 7000 ERHC Gas Valve ...
Page 66: ...66 Honeywell Electronic Ignition Trouble Shooting Guide ...
Page 67: ...67 Honeywell Hot Surface to Pilot Trouble Shooting Guide ...
Page 80: ...80 ...
Page 84: ...84 ...
Page 87: ...87 THIS PAGE LEFT BLANK INTENTIONALLY ...
Page 88: ...88 ...