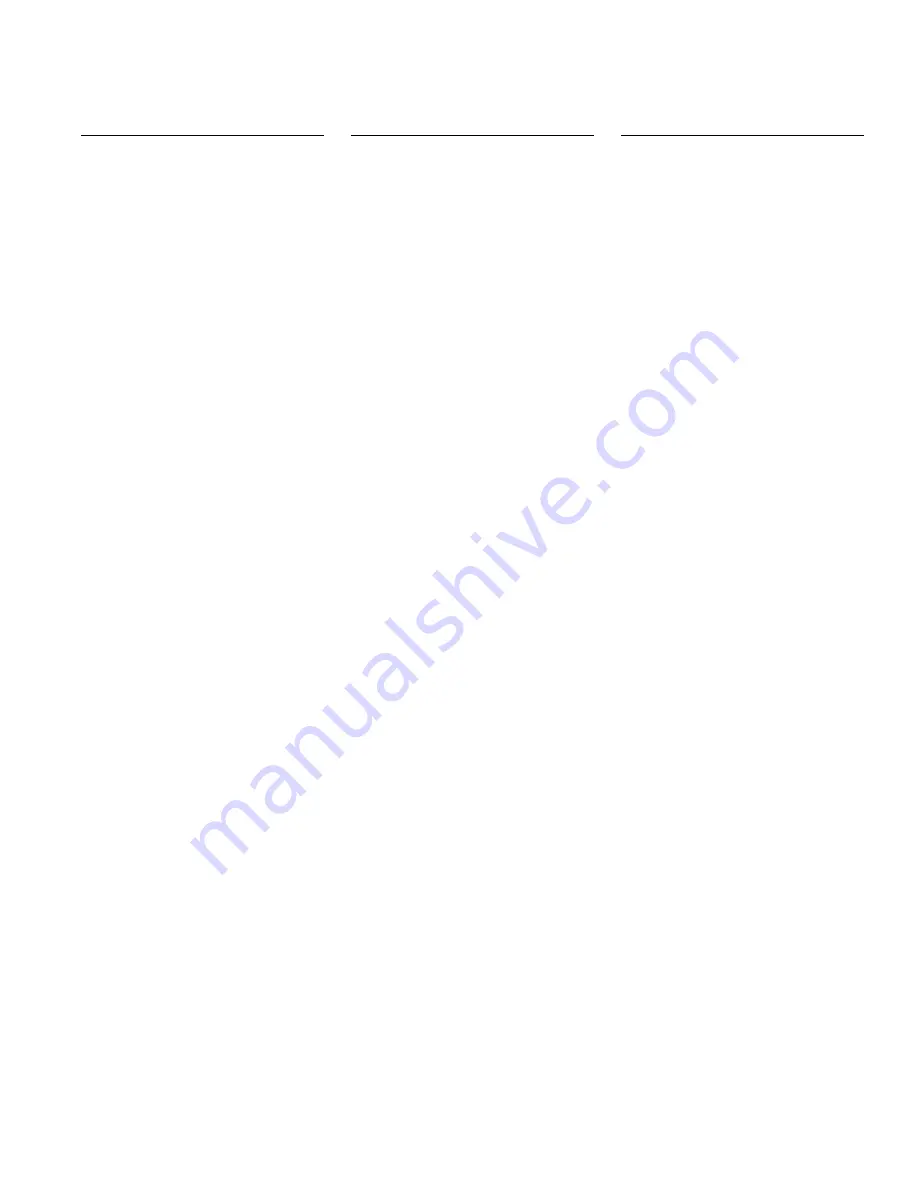
Page 11
TROUBLESHOOTING (cont.)
PROBLEM
PROBABLE CAUSE
REMEDY
BREWING CIRCUIT (cont.)
Dripping from sprayhead
Weak beverage
Drip out time too long
1. Lime build up
2. Brew Solenoid Valve
1. Sprayhead
2. Water temperature
3. Funnel loading
1. Funnel Tip
Inspect the tank assembly for ex-
cessive lime deposits. Delime as re-
quired.
Refer to
Service - Brew Solenoid
Valve for testing procedures. See
page 16
A five-hole stainless steel spray-
head must be used for proper ex-
traction.
Place an empty brew funnel on an
empty vessel of at least 4 gallons
beneath the sprayhead. Initiate
brew cycle and check the water
temperature immediately below the
sprayhead with a thermometer. The
reading must not be less than 5
°
F
below set temperature. Adjust the
temperature setting to increase the
water temperature. Refer to
Initial
Set-up instructions.
The packet must be centered in the
funnel and the bed of tea leaves lev-
eled by shaking gently.
The brew funnel should be cleaned
thoroughly before each brew cycle
to lessen the chance of tea leaf par-
ticles clogging the funnel tip.
33030 052600