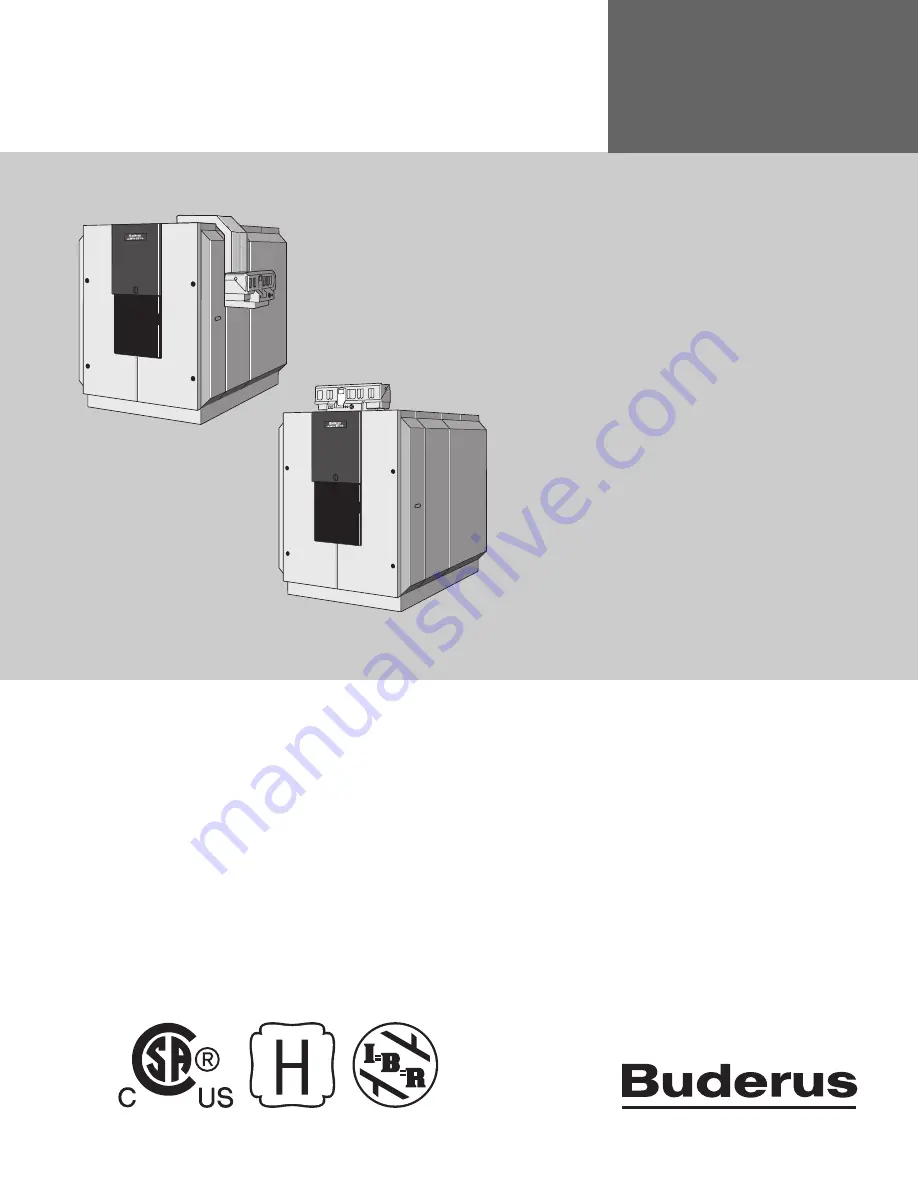
For contractors
Read carefully prior to
installation and mainte-
nance
WARNING:
If installation, adjustment, modification, oper-
ation or maintenance of the heating system is carried out
by an unqualified person, this may result in personal injury
or property damage.
The directions of this installation manual must be followed
precisely.
If support or additional information is required, contact a
qualified service company, service provider or the gas
company.
WARNING:
Observe the safety instructions of this installation manual
before placing the heating appliance in operation.
The operating manual is a component of the technical
documentation and must be handed over to the operator
of the heating system. Explain to the owner or operator
how to use the heating system using the operating
instructions. Make sure that he has been familiarized with
all information required for the operation of the heating
system.
NOTICE:
In the Commonwealth of Massachusetts this
boiler must be installed by a licensed plumber or gas fitter.
This manual is available in the English and French lan-
guage.
Please keep this manual for future reference.
Installation and Service
Instructions
Low-temperature oil/
gas boiler
Logano G615
6 720 642 625-00.1O
Boilers for oil/gas-fired power burners
6 720
647
2
07(
201
0/
12) U
S
/CA