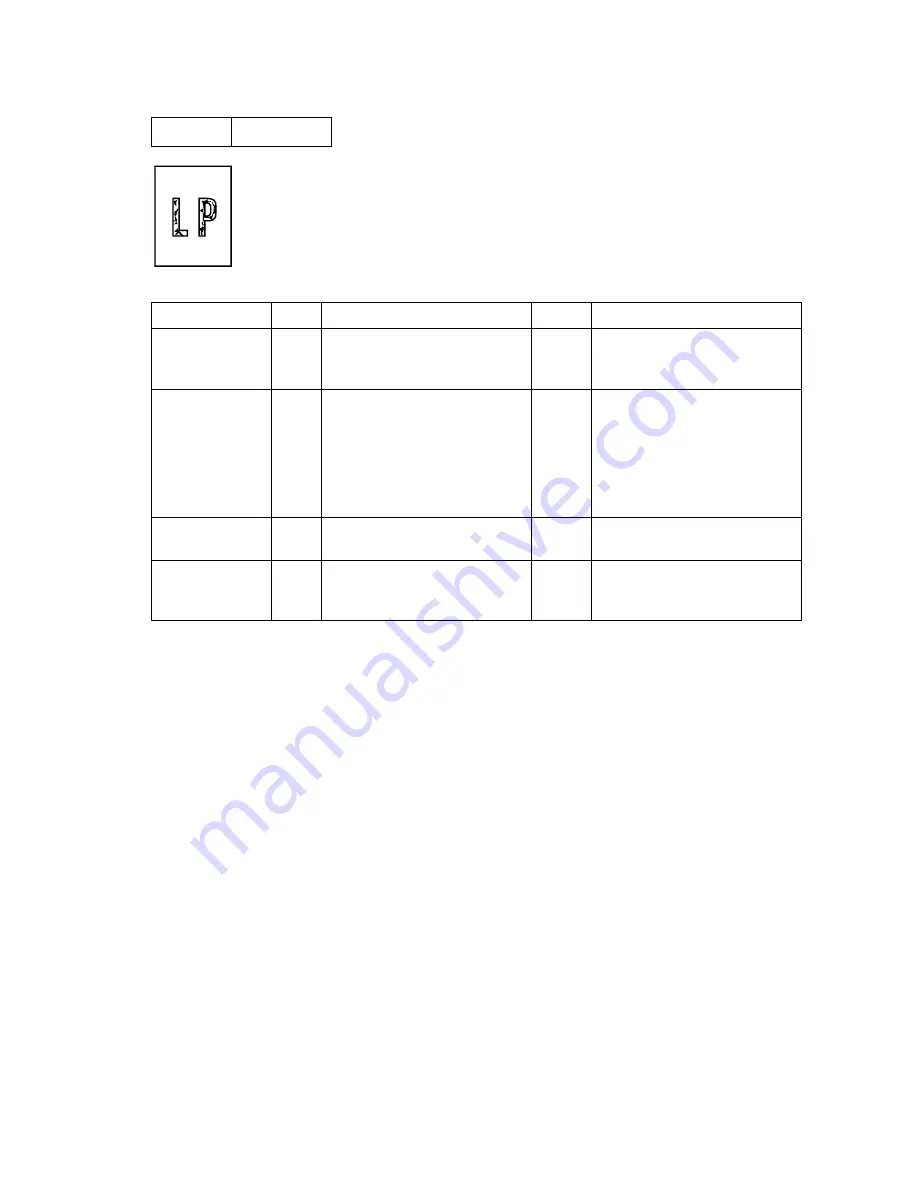
IV-14
I-11
Poor fixing
<Printing>
Possible cause
Step
Check
Result
Remedy
Printing paper
1
Is thick paper of more than 42
lb. weight in use?
Yes
Instruct the user to use paper
of the recommended weight
and thickness.
Toner sensing
failure
2
Is the problem solved by
replacing the drum unit or the
toner cartridge?
(When printing is faint.)
Yes
Toner is empty.
The toner sensing is defective,
clean the toner sensor.
If the wiper in the toner
cartridge is broken, replace the
toner cartridge with a new one.
Thermistor
failure
3
Is the thermistor fitted
correctly?
No
Fit the thermistor correctly.
Low-voltage
power supply
PCB failure
4
Is the problem solved by
replacing the low-voltage
power supply PCB?
Yes
Replace the low-voltage power
supply PCB.
Summary of Contents for HL-P2000
Page 1: ......
Page 27: ...II 8 1 3 8 Engine I O Fig 2 10 shows the engine interface circuit Fig 2 10 ...
Page 69: ...III 28 4 PACKING Fig 3 48 Documents Accessory carton Pad Pad Printer Bag Carton Drum Unit ...
Page 115: ...Appendix 5 Main PCB Circuitry Diagram 1 3 CODE UK3981000 B512018 CIR 1 3 NAME A 6 ...
Page 116: ...Appendix 6 Main PCB Circuitry Diagram 2 3 CODE UK3981000 B512018 CIR 2 3 NAME A 7 ...
Page 117: ...Appendix 7 Main PCB Circuitry Diagram 3 3 CODE UK3981000 B512018 CIR 3 3 NAME A 8 ...
Page 118: ...Appendix 8 Panel Sensor PCB Circuit Diagram CODE UK4010000 B48K303CIR NAME A 9 ...
Page 119: ...Appendix 9 Scanner Panel PCB Circuit Diagram CODE UK3982000 B512019 CIR NAME A 10 ...
Page 120: ...Appendix 10 Scanner Sensor PCB Circuit Diagram A 11 B512020 CIR CODE UK3983000 NAME ...
Page 170: ......
Page 249: ...APPENDIX A 9 HP LaserJet IIP EPSON FX 850 IBM Propritner XL EPSON FX 850 ...
Page 260: ...Aug 98 84U007BE0 PARTS REFERENCE LIST MODEL MFC P2000 HL P2000 R LASER PRINTER ...