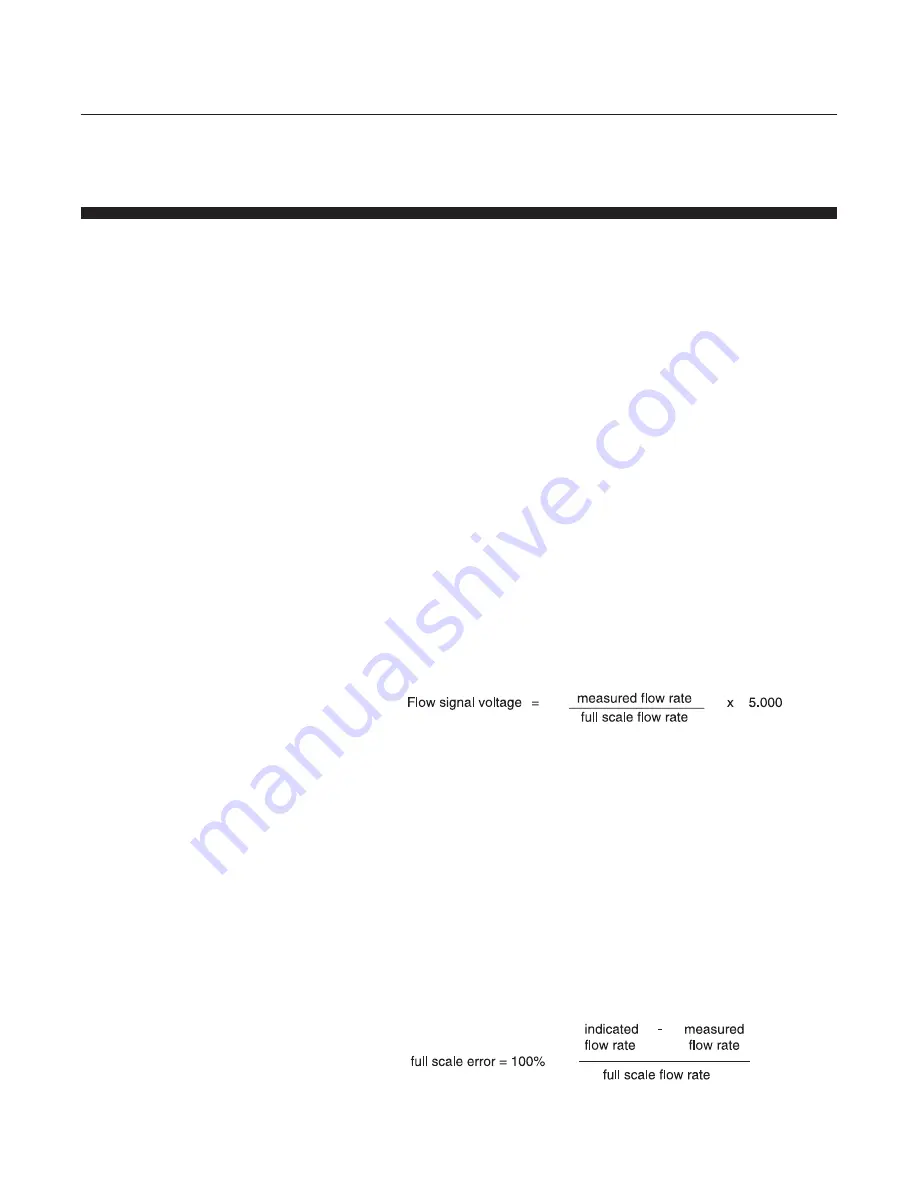
3-3
Brooks
®
Model 5860
i
Section 3 Operation
Installation and Operation Manual
X-TMF-5860i-MFM-eng
Part Number: 541B110AAG
November, 2008
potentiometer (refer to Figure 3-3) until the desired output signal is
obtained.
3-4 Calibration Procedure
NOTE 1:
Calibration of the Model 5860
i
mass flowmeter requires the use
of a digital voltmeter (DVM) a flow control valve or mass flow controller to
set the flow rate and a precision flow standard calibrator such as the
Brooks Vol-U-Meter
®
. It is recommended that the calibration be performed
only by trained and qualified service personnel.
NOTE 2:
If the mass flow meter is to be used on a gas other than the
calibration gas, apply the appropriate sensor conversion factor. Refer to
Section 4-5.
a. Adjust the anticipate potentiometer fully clockwise (20 turns). Then
adjust the anticipate potentiometer 10 turns counterclockwise to
center the potentiometer. This will provide a rough adjustment of this
circuit and make the flow signal stable for calibration.
b. Connect the DVM positive lead to the 0-5V signal output, pin 2, and
the negative lead to signal common (TP4). Adjust the zero
potentiometer for an output of 0mV ±2mV.
c. Increase the flow rate until the flow signal output equals 5.000V.
Connect the DVM positive lead to the TP2 (linearity voltage)and the
negative lead to TP4 (signal common). Adjust the linearity
potentiometer for an output of 0.0V (zero volts).
d. Connect the DVM positive lead to the 0-5V signal output (pin 2) and
the negative lead to TP4 (circuit common). Measure the flow rate
using suitable volumetric calibration equipment. Adjust the flow rate
to the proper full scale flow.
Adjust the span potentiometer until the voltage at pin 2 is 5.000V.
e. Measure the voltage at TP1. The voltage at TPl is -100 times the
output voltage of the sensor. This voltage can range from -1.2 to -12
volts, however it is recommended that this voltage stay between 2.0
and 9.0 volts for proper operation. If the recommended voltage
range exceeds this then the desired accuracy and/or signal stability
may not be achieved. If one of the limits is reached check the
restrictor sizing procedures. Refer to Section 4-6.
f. Shut off the flow. Connect the DVM positive lead to flow signal output
(pin 2) and the negative lead to TP4. Readjust the zero
potentiometer for an output of 0mV ±2mV as necessary.
g. Increase the flow rate for a flow signal output of 50% (2.500V) and
measure the flow rate. Calculate the error as a percentage of full
scale.