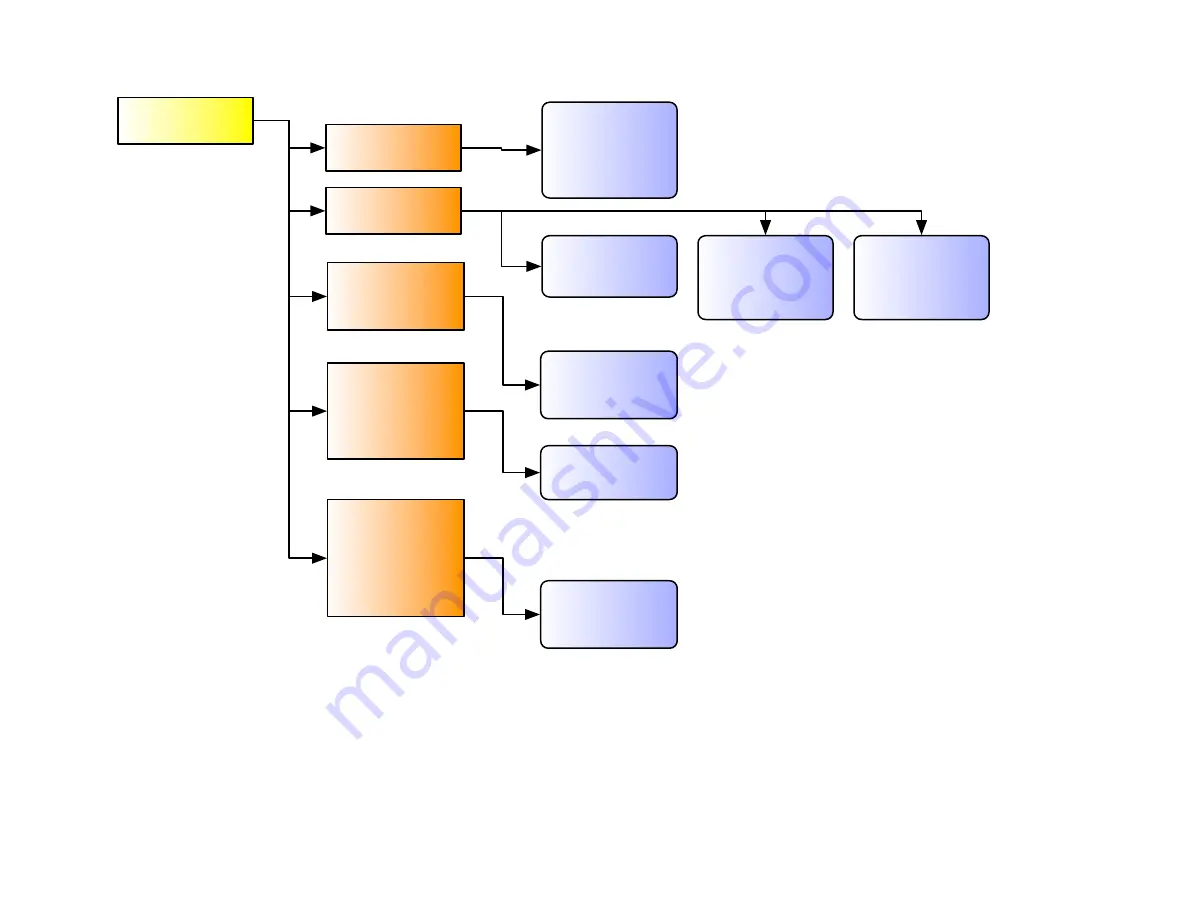
Doesn't Move at
all
Speed pots are
not turned up
Turn up speed
pot adjustments
preset 1-4. Set
speed per ANSI
chart in manual
RTDP Reads 0
PLC not in RUN
mode, Move
switch to RUN
PLC Output relay
not working
Replace PLC if
relays are not
making
Enable jumper on
KB motor control
is missing.Rev. 'E'
series & above
Replace jumper
Screws on Blue
terminal block on
KB motor control
are not secure
Rev. 'E' series &
above
Tighten set
screws 1/2 turn
past 'snug'
Troubleshooting Guide
Check
Transducer / A/D
converter wiring
for securness
A/D Converter or
transducer is
damaged