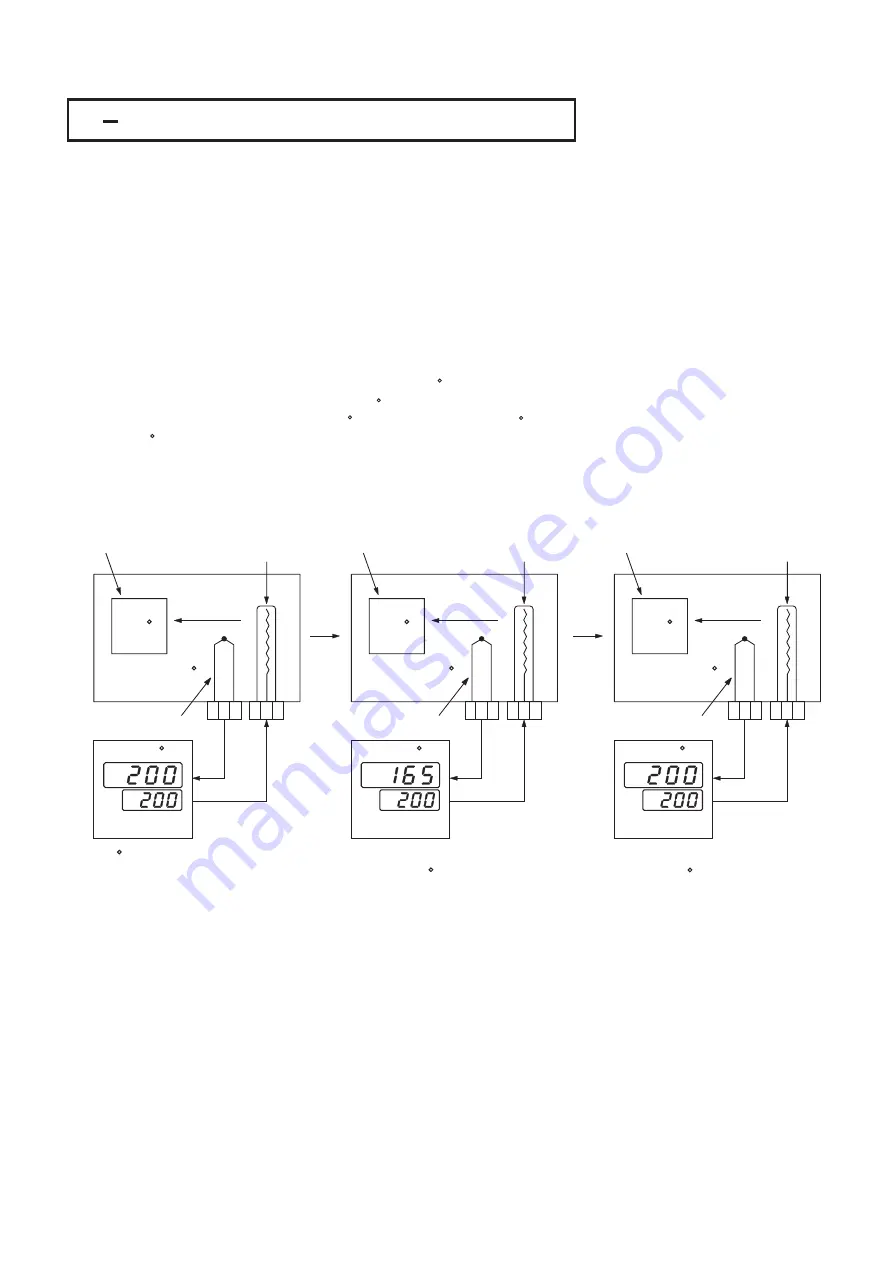
3 16 PV1 Shift
3 16 PV1 Shift
165 C
165 C
200 C
C
C
C
Heat
Transfer
Heat
Transfer
Heat
Transfer
200 C
200 C
235 C
Sensor
Sensor
Sensor
Subject
Subject
Subject
Heater
Heater
Heater
35 C temperature
difference is observed
SHIF= 0
Adjust SHIF
SHIF= -35 C
Supply more heat
Display is stable
SHIF= -35 C
PV=SV
Figure 3.20
PV1 Shift Application
Figure 3.20
PV1 Shift Application
UM25001C
55
In certain applications it is desirable to shift the controller display value from
its actual value. This can be easily accomplished by using the PV1 shift
function.
In certain applications it is desirable to shift the controller display value from
its actual value. This can be easily accomplished by using the PV1 shift
function.
Press the " scroll " key to the parameter SHIF. The value you adjust here, either
positive or negative, will be added to the actual value. The SHIF function will
.
alter PV1 only
Press the " scroll " key to the parameter SHIF. The value you adjust here, either
positive or negative, will be added to the actual value. The SHIF function will
.
alter PV1 only
Here is an example. A process is equipped with a heater, a sensor and a
subject to be warmed up. Due to the design and position of the components in
the system, the sensor could not be placed any closer to the part. Thermal
gradient ( different temperature ) is common and necessary to an extent in any
thermal system for heat to be transferred from one point to another. If the
difference between the sensor and the subject is 35 C, and the desired
temperature at the subject to be heated is 200 C, the controlling value or the
temperature at the sensor should be 235 C. You should input -35 C as to
subtract 35 C from the actual process display. This in turn will cause the
controller to energize the load and bring the process display up to the set point
value.
Here is an example. A process is equipped with a heater, a sensor and a
subject to be warmed up. Due to the design and position of the components in
the system, the sensor could not be placed any closer to the part. Thermal
gradient ( different temperature ) is common and necessary to an extent in any
thermal system for heat to be transferred from one point to another. If the
difference between the sensor and the subject is 35 C, and the desired
temperature at the subject to be heated is 200 C, the controlling value or the
temperature at the sensor should be 235 C. You should input -35 C as to
subtract 35 C from the actual process display. This in turn will cause the
controller to energize the load and bring the process display up to the set point
value.