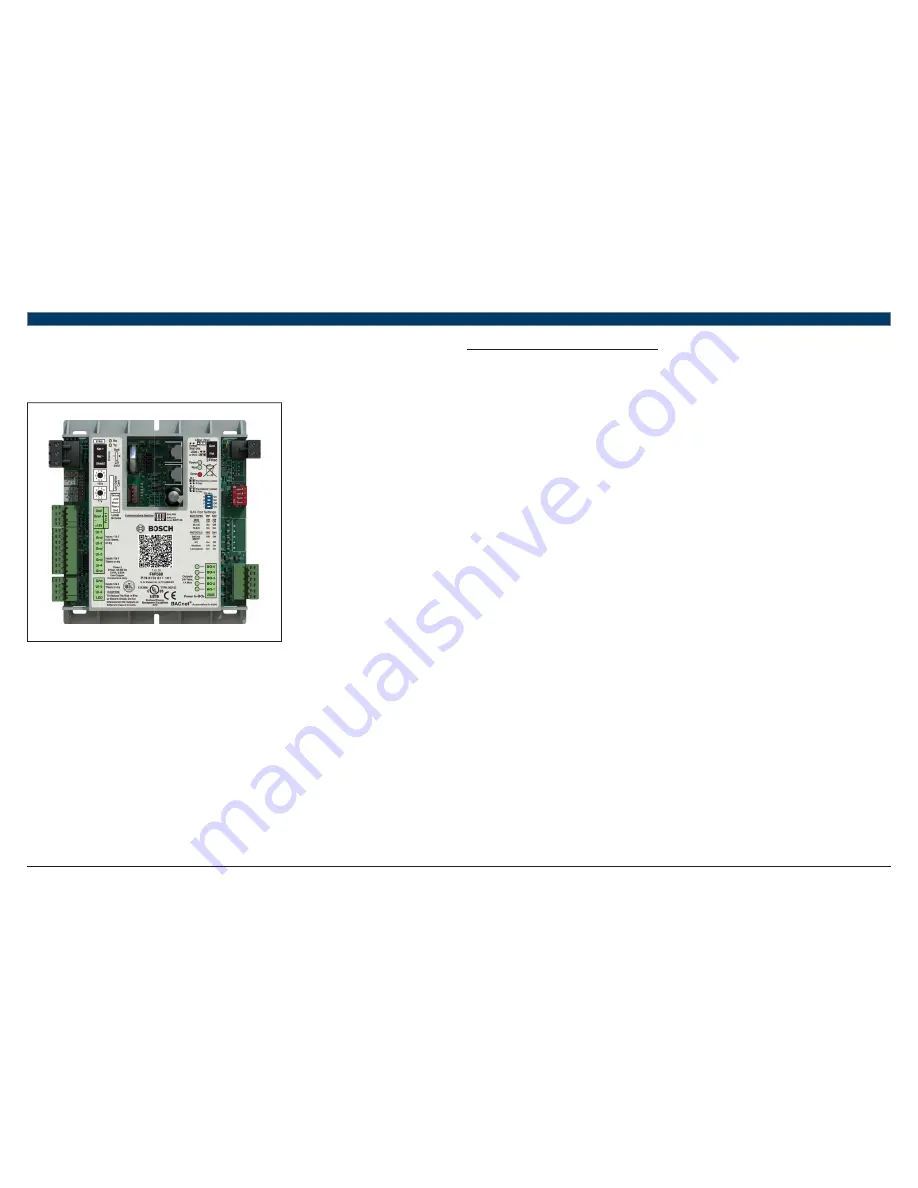
Applications Manual FHP560 Controller
| 3
Bosch Thermotechnology Corp.
Data subject to change
Page____ of ____
2 FHP560 Overview
The FHP560 Multi-Protocol Heat Pump controller is used in most con
fi
gure-to-order applications requiring integration of Direct Digital Control
(DDC) systems. The controller is BACnet native but is
fl
exible enough to integrate into existing Building Automation Systems (BAS) via a choice of
the most widely used protocols including: BACnet MS/TP, N2, Modbus, and LON (requires additional hardware). The FHP560 may be run either in
stand-alone operation mode, or with the DDC network by integrating with a BAS.
Fig. 1 FHP560 Controller
The FHP560 is packaged with a highly sophisticated yet easily con
fi
gurable software (version 7.05.03) that suits the different heat pump
applications. User parameters and options relating to the physical build of the corresponding heat pump unit (e.g. number of compressors,
reversing valve, reheat coil, etc) are usually programmed at the factory to facilitate a seamless integration in the
fi
eld. However, commissioning
of the controller in the
fi
eld is required to ensure the setup exactly matches the requirements of the jobsite. User settings of the factory standard
software, such as the time and test and balance set points, are usually set up during the installation and commissioning process.
When properly connected to a Bosch Water Source Heat Pump (WSHP), the FHP560 controller works in tandem with the onboard Unit Protection
Module (UPM) to protect the unit compressor from faults such as high/low pressure, high condensate, freeze evaporator/condensor coils, and
brown-outs. The controller monitors the alarm contacts of the UPM board, then decodes and broadcasts any fault conditions that may arise over a
network if one is available.
The controller also works with multi-functional ZS room sensors that, depending on model, are capable of reading not only the zone temperature,
but also CO
₂
and relative humidity levels. When wired correctly, the controller commands the heat pump unit to operate in heating or cooling
mode, and can also provide commands for other options such as hot gas reheat to manage relative humidity while cooling. The operating
parameters of the unit may be communicated to a BAS over the DDC network if available.
2.1 Key Features/Bene
fi
ts
Flexible and easily configured software package for options including:
—
Hot Gas Reheat
—
Auxiliary Electric Heat
—
Condenser Water Valve Control
—
Loop Pump Control
—
Field supplied Fresh Air Damper Control
—
Water-Side Economizer
—
Boilerless Electric Heat Control
—
Air Economizer
Provides multi-protocol communications for seamless integration with systems running industry standard protocols such as:
—
BACnet MS/TP
—
Johnson Controls N2
—
Modbus
—
Lon Works (additional hardware required for Lon).
Ruggedly built for quality and reliability
Stand-alone operation or networked DDC operation capable
Removable wiring connectors for ease of field service
Allows application parameters to be saved and recovered following power loss