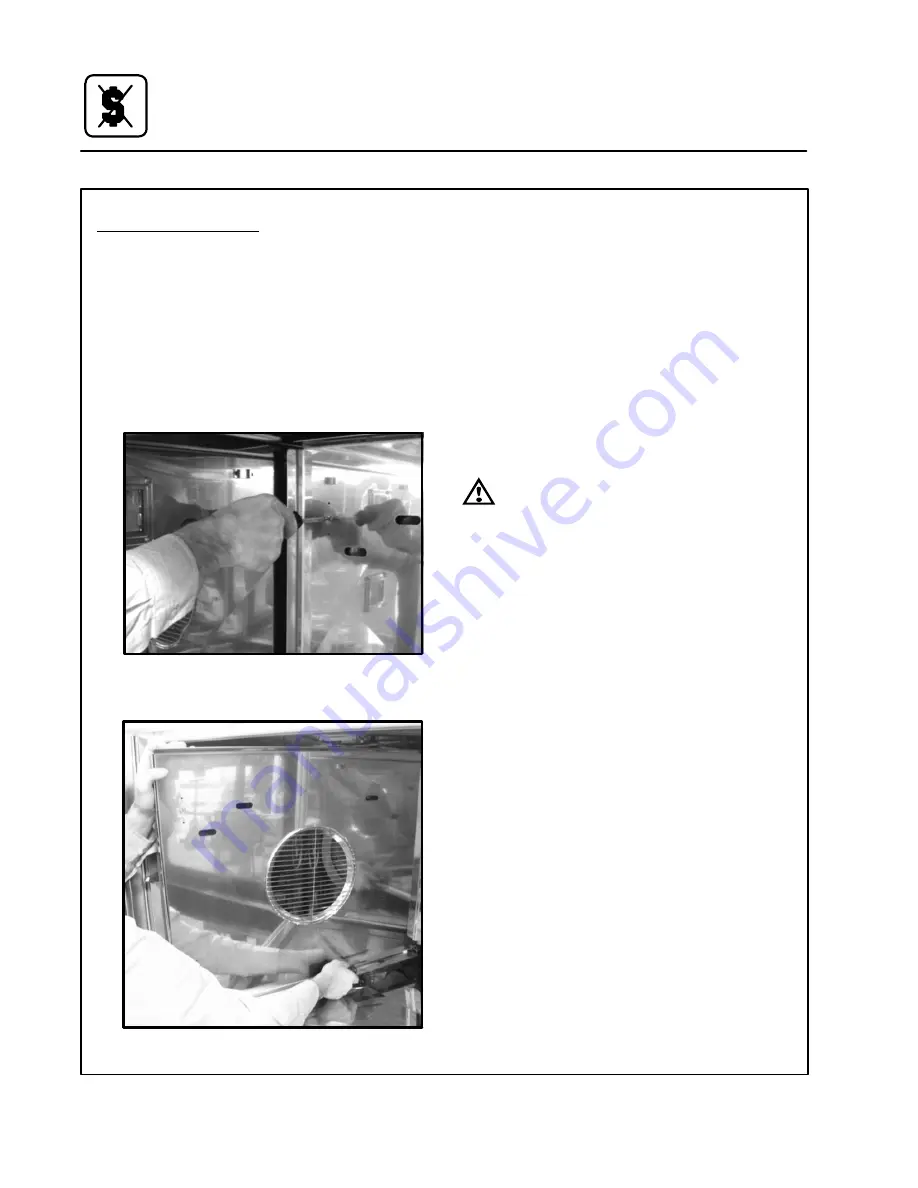
Maintenance
20
Cleaning and Preventive Maintenance
Oven Weekly Cleaning
In addition to the daily cleaning, it is necessasry to
clean behind the fan guard of this oven on a weekĆ
ly basis. This is necessary for proper functioning
of the oven. Scale will build up on the fan and heat
source leading to a less efficient oven.
1. Turn off the oven. Make sure that the oven is
cooled down to under 140
F (60
C).
2. Remove the rack guides.
3. Rotate the two screws on the left side of the fan
guard.
Figure 14
4. Remove the fan guard.
Figure 15
5. Thoroughly spray cleaner onto the fan and
heat source. Close the doors to allow the
cleaner to work.
6. After ten minutes, rinse the cleaner off. Return
the fan guard to the closed position. Rotate
the two screws to secure the fan guard.
Remove and clean the blower wheel every 6
months.
CLEANING THE EXTERIOR
The exterior of the appliance may be cleaned and
kept in good condition with a light oil. Saturate a
cloth and wipe the appliance when it is cold; wipe
dry with a clean cloth.
WARNING!!
DO NOT spray the outside of the appliance
with water or clean with a water jet. CleanĆ
ing with a water jet can impregnate chloĆ
rides into the stainless steel, causing the
onset of corrosion.
PREVENTIVE MAINTENANCE
The best preventive maintenance measures are
āāāthe āāāproper āāinitial āāinstallation āāof āāthe equipment and
a program for cleaning the appliance routinely.
The oven requires no lubrication. Contact the facĆ
tory, the factory representative or a local Blodgett
service company to perform maintenance and reĆ
pairs should they be required.