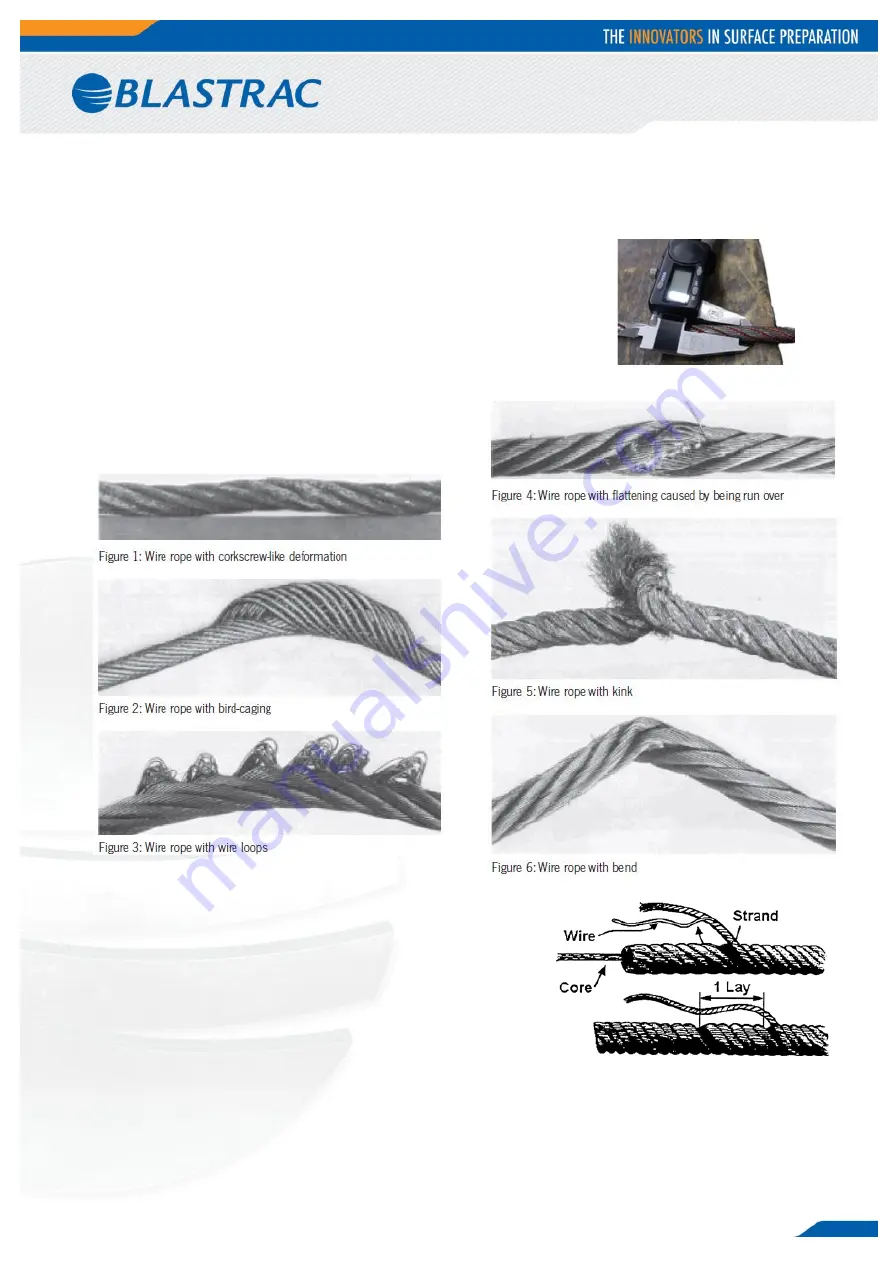
28
6.5
Regular checks of hoisting cables
Stop working immediately if defects occur during operation!
Wire ropes must be replaced immediately if a defect has been detected during the weekly check:
More than 11 broken wires over a length of 27 cm
Strong formation of rust on the surface or inside
Heat damage, indicated by burning discoloration
Reduction of the outer diameter to less than 10.0 mm
Excerpt from DIN15020:
Illustration of the most common types of
outer damage of wire ropes:
Since defective wire ropes are a danger to operational safety,
support and safety wire ropes should be inspected for damage
on a weekly basis and replaced if necessary.
To prolong the service life of wire ropes, always makes sure they
are clean and lightly lubricated. Wire ropes are to be inspected
regularly and replaced if necessary.
The system operator is responsible for replacing defective wire
ropes. The wire rope certificates for the undocked wire rope needs to be retained.
If defects occur during operation, stop work immediately, secure suspended accessequipment in accordance
with EN 1808/secure the material handling system and repair the defects immediately.
This is the responsibility of the system operator.