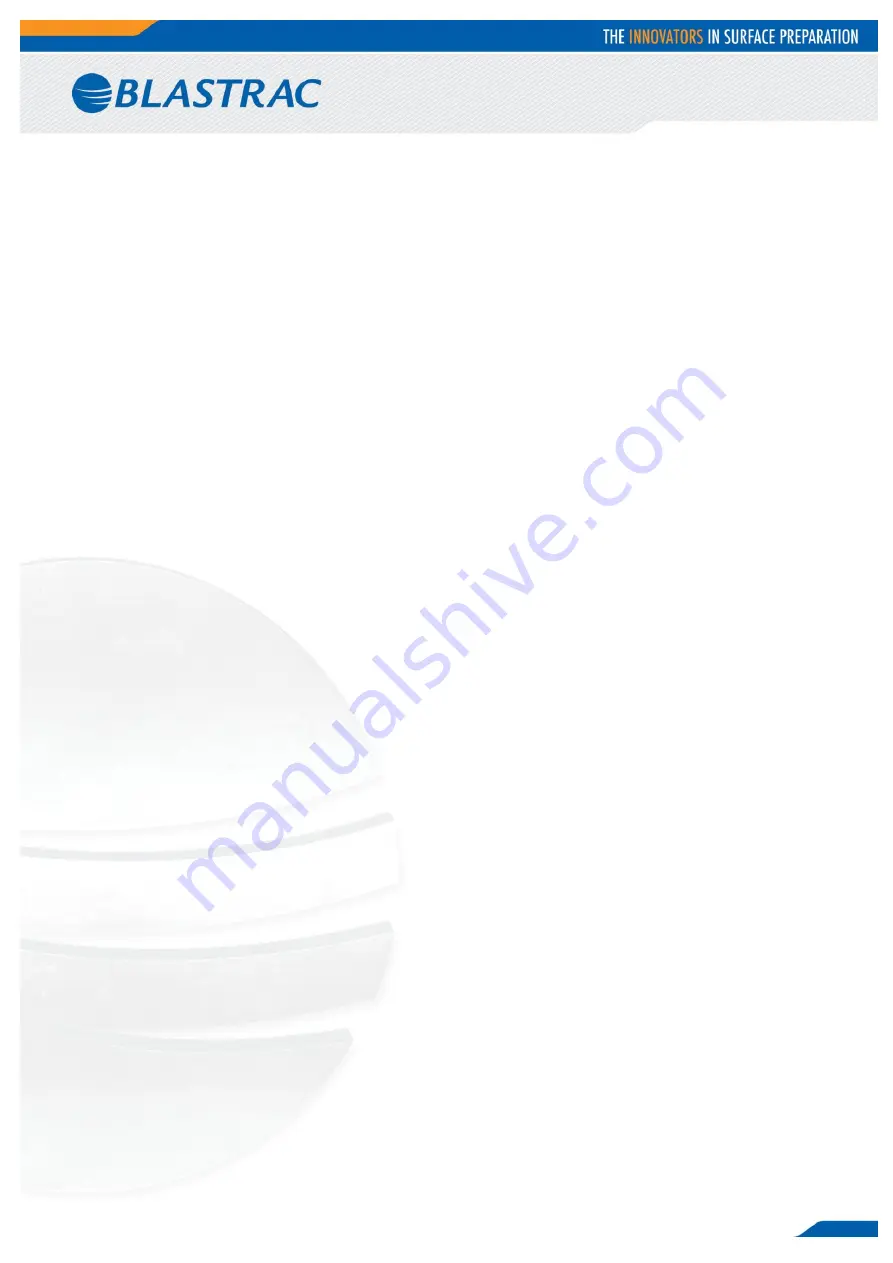
12
3.5
Shot/steelblasting safety
a)
Never pull the blast head off the surface during blasting! This could cause serious injury to yourself and
others around you!
b)
Abrasive can escape from the sides of the blast head at high speed. Wear safety glasses with lateral
protection and close-fitting protective clothing.
c)
Check the following parts daily for damage and wear to avoid unnecessary long and costly standstill on
the workplace; blastwheels, abrasive valves, magnet- and rubber sealing;
Replace the parts when you can see obvious signs of wear.
Wear grooves are acceptable until 75% of blade thickness has been worn away.
d)
Check the parts of the machine on wear and defects. Remove foreign bodies and dust deposits to prevent
clogging of the system.
e)
The cover of the spare shot hopper must be closed to keep the vacuum in the machine.
f)
The machine will heat up during blasting, don’t risk getting burned, always wear gloves and only touch
the handle grip(s) and control devices.
g)
Check the level of abrasive in the storage hopper before work starts. Refill if necessary.
h)
Remove the abrasive from the abrasive storage hopper before storage.
i)
In some cases sparks could be created by shot / steelblasting.
Vertical blasting:
a)
Check for obstacles near the electric cables or dust hose what can hooks when machine is moving up and
down.
b)
The operator must always be at a safe distance, straight behind the machine with the most optimal view
on the machine and working environment.
c)
Never pull on the machine during blasting. Wait until the blast wheels stand still before pulling the
machine from the wall.
d)
Avoid excessive inching operation caused by frequent, brief actuation of the control switches for
UP/DOWN.
e)
When lifting the machine from the ground, always use the lowest lifting speed. The steel cables must first
be tensioned at this speed; they must not be slack when the machine is lifted from the ground.
f)
It is forbidden to use the machine for the transportation of persons or goods.
g)
Welding work on the winch and the steel cable is strictly forbidden. The steel cable must not be used as
earth conductor for welding work.
h)
Only use the Blastrac approved steel cables in appropriate condition. Using any other steel cable voids all
warranty claims against Blastrac BV.
i)
Only use common multi-purpose oil or grease for lubricating the winch and steel cable. Do not use any
lubricants which contain molybdenum disulphide (MoS2) or PTFE!
Check points on the hoisting and lifting equipment
j)
Inspect the cables, rigging and winch motors for damages before every use.
k)
Daily check the functioning of the end-switch for the winch: Press down the actuator by hand, the
machine must not move upwards when the UP-button is then used on the remote control.
l)
The hoisting and lifting motors, cables and shackles have to be inspected by a certified expert.
m)
Comply with the local regulations regarding the frequency of the inspections (e.g. annually, half-yearly,
quarterly etc.)
n)
Since defective cables are a hazard to safe operation, check the steel cables for damage at weekly
intervals in accordance with chapter 6.2 and replace them, as required.
o)
In order to increase the service life of the steel cables, make sure that they are clean and slightly
lubricated.
p)
After inspection / repairs the enclosed service book at the back of the manual has to be filled in.
q)
If damage to one of safety devices, its mounting, the electrical supply cable or the safety rope occurs
during operation, you should stop work immediately and inform the supervisor. All safety-related damage
is to be reported to the system operator and the appropriate logbook entries made.
r)
The system is only allowed to be put back into operation once the damage has been repaired. This is the
responsibility of the system operator!
s)
During operation, communication between the operator and a competent person must always be ensured.
This is the responsibility of the system operator.