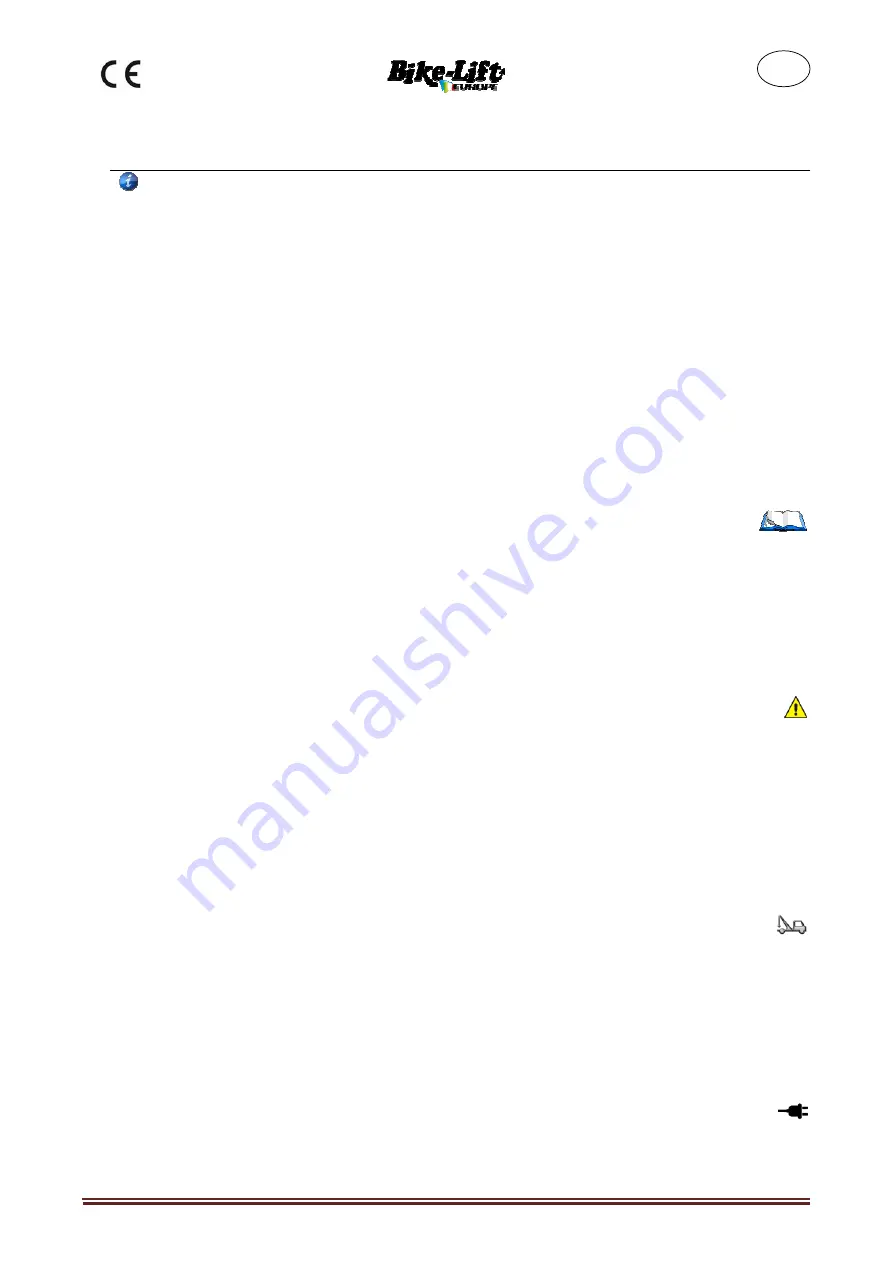
Operating manual No.
057-2-6-0013-R0
Version 2021
Page 2
EN
Summary
1
1.1
Preface ............................................................................................................................................... 4
1.2
Prohibitions........................................................................................................................................ 5
1.3
Warranty ............................................................................................................................................ 5
1.3.1
Warranty conditions .................................................................................................................. 5
1.3.2
Insurance ................................................................................................................................... 5
1.4
Manufacturer identification .............................................................................................................. 6
1.5
Technical assistance and spare parts ................................................................................................ 6
1.6
EC Declaration of conformity ............................................................................................................ 7
1.7
Normative references ........................................................................................................................ 8
1.8
Key ..................................................................................................................................................... 9
2
Machine description .................................................................................................................... 10
2.1
Machine name ................................................................................................................................. 10
2.2
Machine identification ..................................................................................................................... 10
2.3
Machine description ........................................................................................................................ 11
2.4
Intended use .................................................................................................................................... 12
2.5
Technical specifications ................................................................................................................... 13
3
Safety section .................................................................................................................................... 15
3.1
Environmental working values ........................................................................................................ 15
3.2
Sound level ...................................................................................................................................... 15
3.3
Residual risks ................................................................................................................................... 15
3.4
Operator protections ....................................................................................................................... 16
3.5
Safety systems ................................................................................................................................. 16
3.6
Pictograms ....................................................................................................................................... 17
4
Transport and handling section ....................................................................................................... 18
4.1
Transport, handling and storage ..................................................................................................... 18
4.2
Packaging and transport .................................................................................................................. 18
4.3
Unloading and handling ................................................................................................................... 18
4.4
Receipt and check ............................................................................................................................ 19
4.5
Storage ............................................................................................................................................. 19
5
Installation section .......................................................................................................................... 20
5.1
Power ............................................................................................................................................... 20
5.2
Putting into service .......................................................................................................................... 21
Information section ............................................................................................................................. 4
Summary of Contents for TWIN-ARMS MTA 516
Page 36: ...Operating manual No 057 2 6 0013 R0 Version 2018 Page 37 EN SPARE PARTS TECHNICAL DRAWINGS ...
Page 37: ...Operating manual No 057 2 6 0013 R0 Version 2018 Page 39 EN ...
Page 38: ...Operating manual No 057 2 6 0013 R0 Version 2018 Page 39 EN NOTES ...
Page 39: ...Operating manual No 057 2 6 0013 R0 Version 2018 Page 39 EN NOTES ...