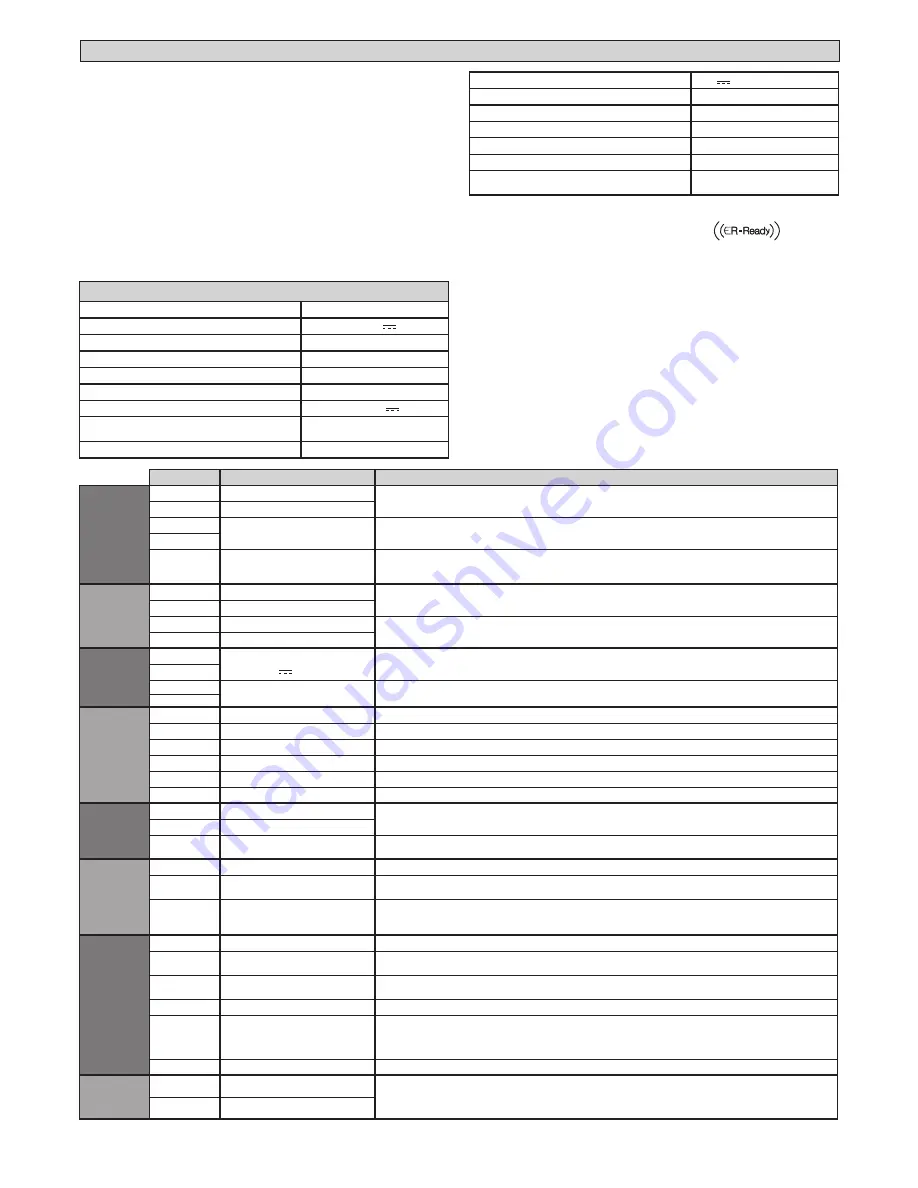
10
- ZARA BTL2
D812059 00100_02
INSTALLATION MANUAL
1) GENERAL INFORMATION
The ZARA BTL2 control panel comes with standard factory settings. Any change
must be set by means of the TRiMMER and DiP SWiTCH settings.
The Control unit completely supports the EELiNK protocol.
its main features are:
- Control of 1 or 2 24V BT motors
Note: 2 motors of the same type must be used.
- Electronic torque control with obstacle detection
- Separate inputs for safety devices
- Built-in radio receiver rolling code with transmitter cloning.
The board has a terminal strip of the removable kind to make maintenance
or replacement easier. it comes with a series of prewired jumpers to make the
installer’s job on site easier.
The jumpers concern terminals: 70-71, 70-72, 70-74. If the above-mentioned
terminals are being used, remove the relevant jumpers.
TESTING
TheZARA BTL2 panel controls (checks) the start relays and safety devices (pho-
tocells) before performing each opening and closing cycle.
if there is a malfunction, make sure that the connected devices are working
properly and check the wiring.
2) TECHNICAL SPECIFICATIONS
Power supply
220-230V 50/60 Hz*
Low voltage/mains insulation
> 2MOhm 500V
Operating temperature range
-20 / +55°C
Thermal overload protection
Software
Dielectric rigidity
mains/LV 3750V~ for 1 minute
Motor relay switching current
10A
Maximum motor power
40W + 40W (24V )
Accessories power supply
24V ~ (demand max. 0,2A)
24V ~ safe
Solenoid lock
24V ~ max. 15W
Flashing light
24V max. 25W
Fuses
see Fig. C
N° of combinations
4 billion
Max.n° of transmitters that can be memorized 63
Maximum work time
3 minutes
Maximum power
130W
Maximum cycle
S3 13s -1-13s-1x30 pause
90 min.
(*other voltages to order)
Usable transmitter versions:
All ROLLING CODE transmitters compatible with
3) TUBE ARRANGEMENT Fi g. A
install the electrical system referring to the standards in force for electrical systems
CEi 64-8, iEC 364, harmonization document HD 384 and other national standards.
4) TERMINAL BOARD WIRING Fig. C
WARNINGS - When performing wiring and installation, refer to the standards in
force and, whatever the case, apply good practice principles.
Wires carrying different voltages must be kept physically separate from each other,
or they must be suitably insulated with at least 1mm of additional insulation.
Wires must be secured with additional fastening near the terminals, using devices
such as cable clamps.
All connecting cables must be kept far enough away from the dissipater.
WARNING! For connection to the mains power supply, use a multicore cable
with a cross-sectional area of at least 3x1.5mm
2
of the kind provided for by
the regulations in force.
To connect the motors, use a cable with a cross-sectional area of at least
1.5mm
2
of the kind provided for by the regulations in force. By way of example,
if the cable is run outside (unprotected), it must be at least type H07RN-F,
while if it is run inside (in a raceway), it must be at least type H05 VV-F.
Terminal
Definition
Description
Po
w
er supply
L
LiNE
Single-phase power supply
220-230V ~50/60 Hz*
N
NEUTRAL
JP2
TRANSF PRiM
Transformer primary winding connection, 220-230V
~*
JP5
JP4
TRANSF SEC
Board power supply:
24V~ Transformer secondary winding
24V= Buffer battery power supply
M
ot
or
10
MOT 1 +
Connection motor 1. Time lag during closing. (T4)
11
MOT 1 -
14
MOT 2 +
Connection motor 2. Time lag during opening. 2s
15
MOT 2 -
Au
x
20
BLiNKER
24V
(MAX. 1A)
Flashing light 24V output max. 25W. Contact stays closed while leaf is operating.
21
28
Solenoid lock
24V ~ max. 15W
29
Limit swit
ches
40
Not used
41
Not used
42
SW1
Limit switch motor 1
43
SW2
Limit switch motor 2
44
Not used
45
Not used
A
cc
essories po
w
er
supply
50
24V-
Accessories power supply output.
51
24V+
52
24 Vsafe+
Tested safety device power supply output (photocell transmitter and safety edge transmitter).
Output active only during operating cycle.
Commands
60
Common
START and OPEN inputs common
61
START
START command button (N.O.).
Operation according to “3/4-STEP” logic
62
OPEN
OPEN command button (N.O.).
Gate opened with this command. if the input stays closed, the leaves stay open until the contact is opened.
When the contact is open, the automated device closes following the TCA time, where activated.
Saf
et
y de
vic
es
70
Common
STOP, PHOT and BAR inputs common
71
STOP
The command stops movement. (N.C.)
if not used, leave jumper inserted.
72
PHOT (**)
PHOTOCELL input (N.C.).
Operation according to “PHOTOCELL/PHOTOCELL DURiNG CLOSiNG” logic. if not used, leave jumper inserted.
73
FAULT 1
Test input for safety devices connected to PHOT.
74
BAR (**)
BAR safety edge input (N.C.).
Configurable according to the “BAR/ 8K2” logic.
The command reverses movement for 2 sec.
if not used, leave jumper inserted.
75
FAULT 2
Test input for safety devices connected to BAR.
A
nt
enna
Y
ANTENNA
Antenna input.
Use an antenna tuned to 433MHz. Use RG58 coax cable to connect the Antenna and Receiver. Metal bodies
close to the antenna can interfere with radio reception. if the transmitter’s range is limited, move the antenna
to a more suitable position.
#
SHiELD
(*) Other voltages available on request
(*) If “D” type devices are installed (as defined by EN12453), connect in unverified mode, foresee mandatory maintenance at least every six months.