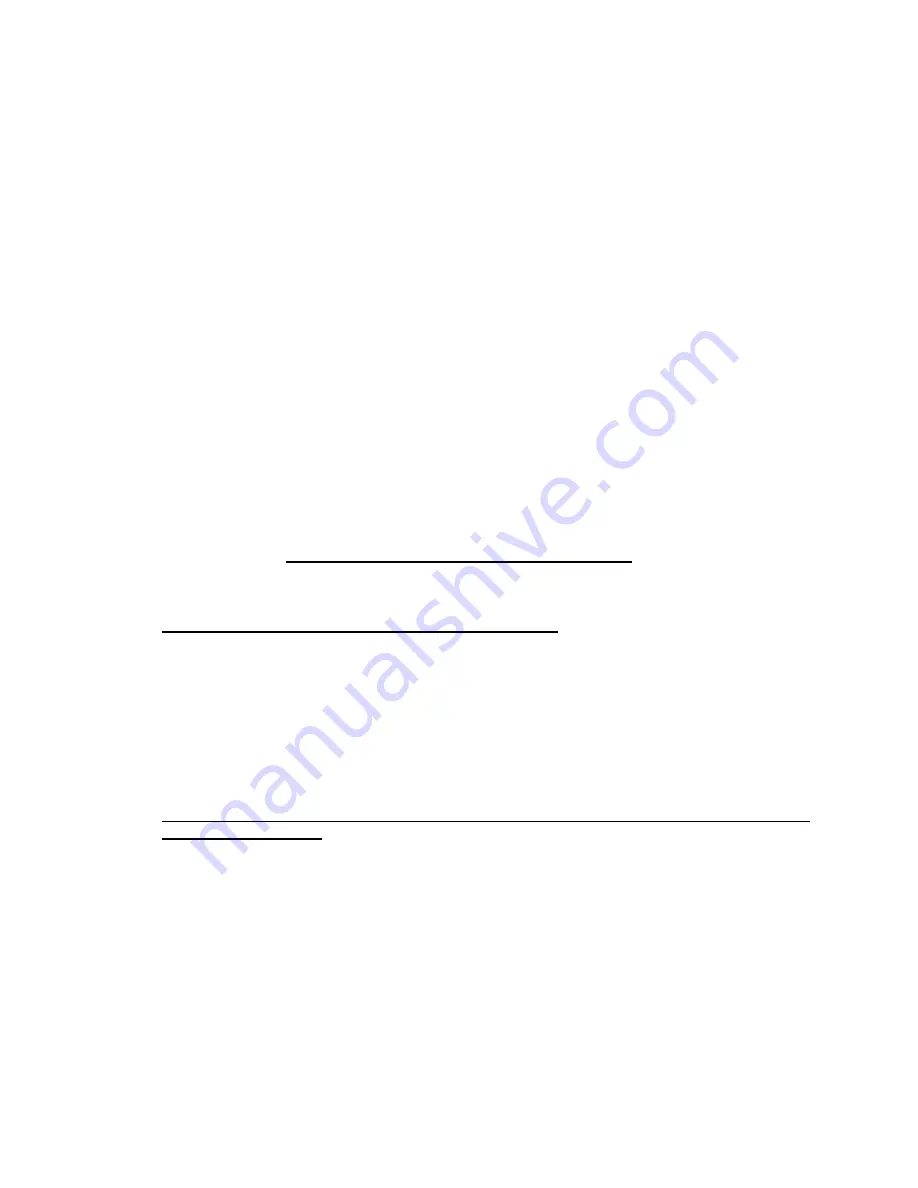
Bettis P/N 127073E
Revision “A”
Page 22 of 37
3.7.3
Apply NOP pressure to the pressure port in inner end cap (3-10) and allow the actuator to
stabilize.
3.7.4
Apply a commercial leak testing solution to the following areas:
3.7.4.1 Joint between inner end cap (3-10) and cylinder (3-70). This checks cylinder to
inner end cap o-ring seal.
3.7.4.2 The port hole in the outer end cap (3-80). This checks the piston D-seal to
cylinder (3-70), o-ring seal (4-70), and rod T seal (4-50).
3.7.4.3 The vent check port hole in housing. This checks Polypak seal (4-30) that seals
piston rod (3-40) to inner end cap (3-10).
3.7.4.6 Remove pressure from the pressure inlet port.
3.7.5
If an actuator was disassembled and repaired, the above leakage test must be performed
again.
SECTION 4 - FIELD CONVERSIONS
4.1
FAIL MODE REVERSAL (CW TO CCW, OR CCW TO CW)
4.1.1
Remove Spring Module per Section 5.3.
4.1.2
Remove Pneumatic Power Module per Section 5.5.
4.1.3
Re-install the Spring Module onto the opposite end of housing (1-10) as it was previously
located per Section 5.4.
4.1.4
Re-install the Override Cylinder Assembly into Spring Module per Section 5.2.
4.2
CONVERTING DOUBLE ACTING ACTUATOR TO SPRING RETURN WITH OVERRIDE
CYLINDER ASSEMBLY
4.2.1
Remove Blind End Cap per steps 4.2.1.1 and 4.2.1.2.
4.2.1.1 Remove hex cap screws (5-20), with spring lockwashers (5-30), from blind end
cap (5-10).
4.2.1.2 Remove blind end cap (5-10) from end of housing (1-10).
4.2.2
If Pneumatic Power Module needs to be relocated due to fail mode requirements (fail
counter-clockwise) use Section 5.5 for removal and Section 5.6 for installation.